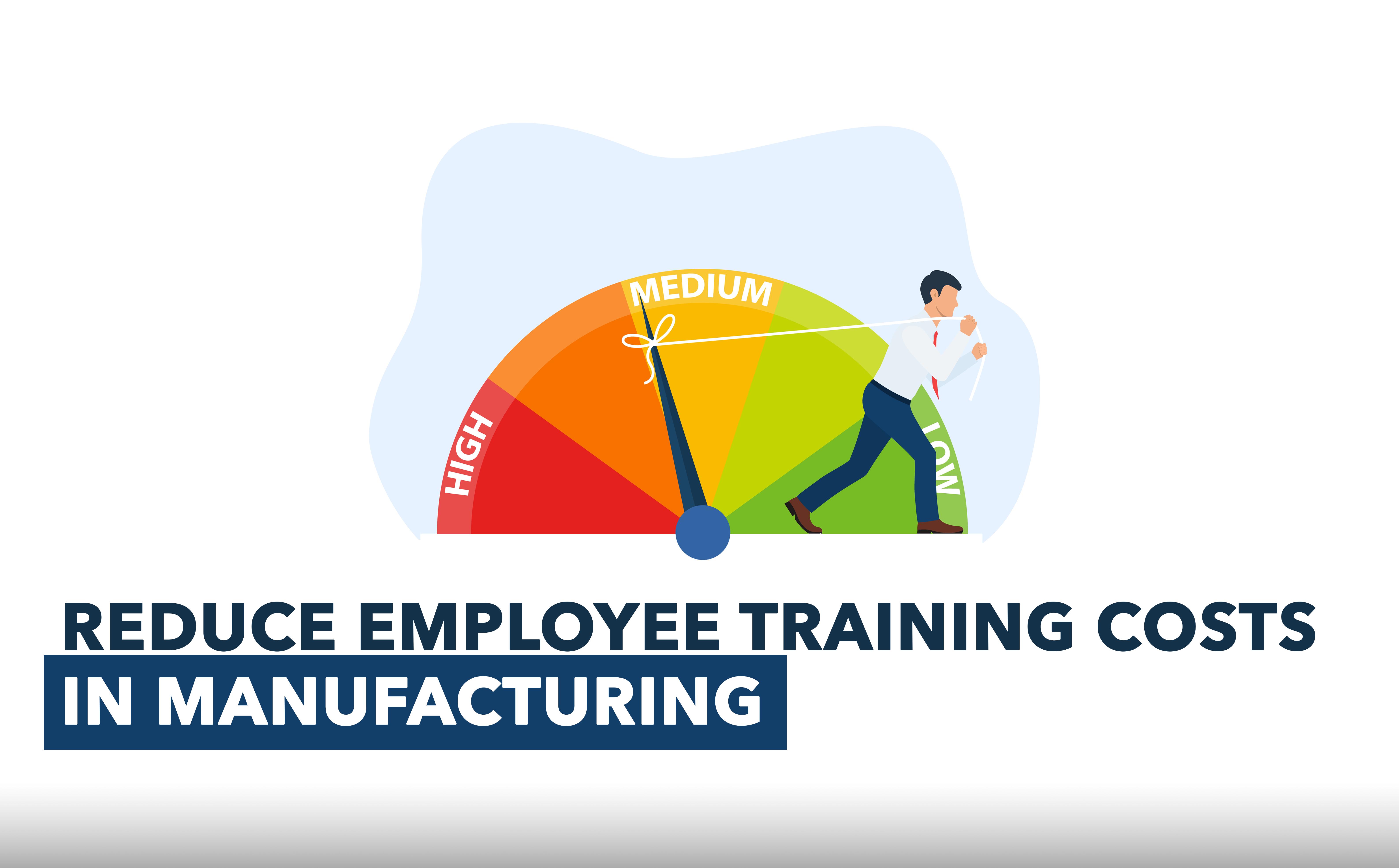
Just-in-time production is a set of principles and practices used by businesses to create goods that meet customer demand. The approach relies on efficient quality controls and effective workflows throughout the manufacturing process. It allows manufacturers lower inventory levels and less warehouse space. These benefits are also beneficial for lower costs.
Although JIT has been proven to reduce overall costs for many companies, implementation can be complicated. JIT is not only dependent on operations coordination, but also the efficiency of the supply chains. It is therefore susceptible to economic or logistical disruptions on the global marketplace. JIT is not difficult to manage, but there are many tools.
When implemented properly, JIT can significantly reduce costs. It also increases the quality of final products. This method will increase both the efficiency and productivity of machine and human labor. Additionally, it helps to increase the speed and smoothness of the production cycle. It reduces the amount of time that is spent on unneeded output. This will also help to lower the environmental impact of the operation.
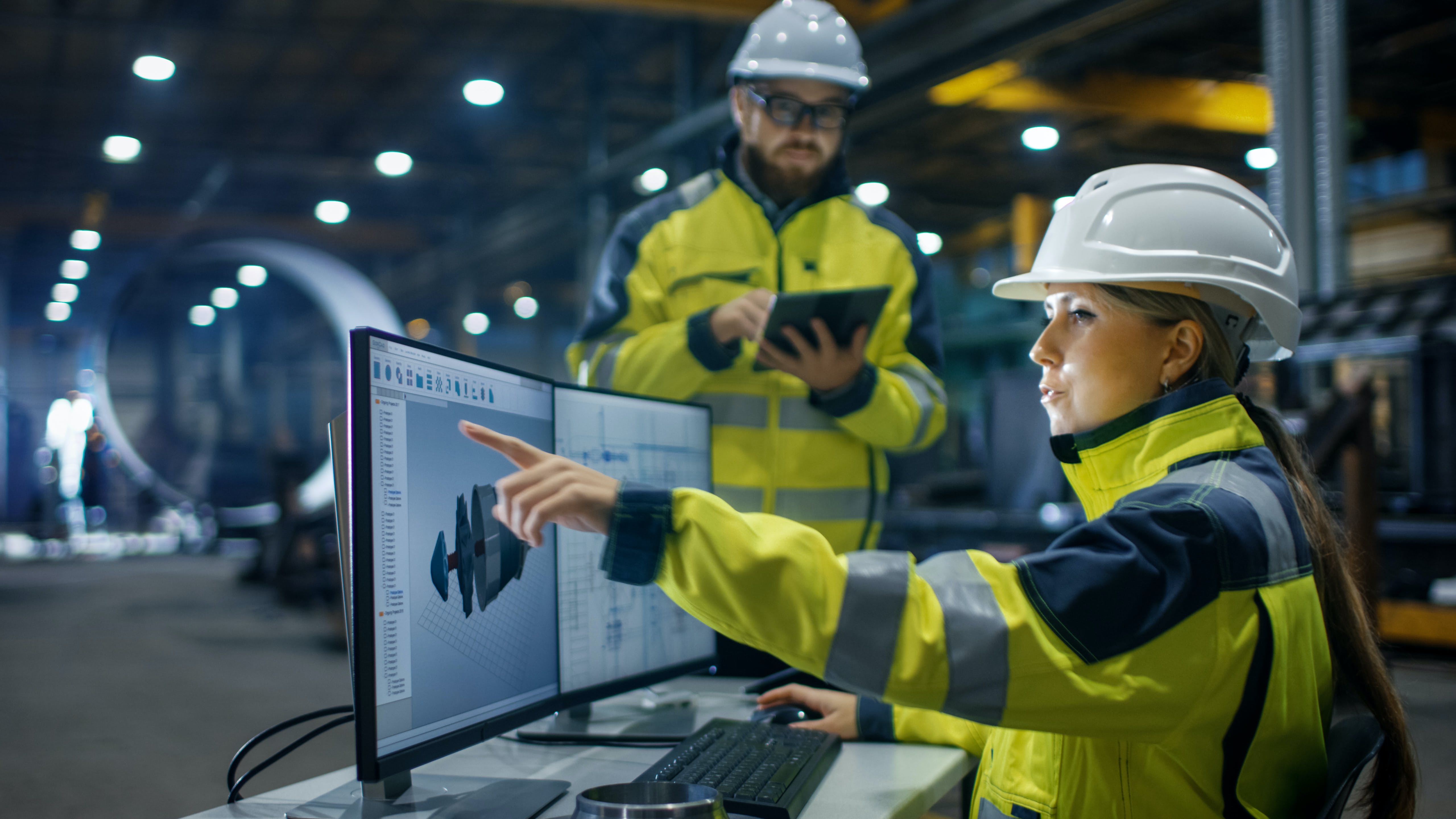
Initially, the concept of just-in-time production was introduced in Japan during the birth of lean manufacturing. After World War II ended, Japanese organisations were forced to depend on limited resources. In order to survive, they had to streamline their manufacturing processes. They used JIT to maximize their output.
Toyota's management team took the method and made it a success. They transformed their production from an inexplicable experiment to an exceptional case in just three years. These methods were so successful, other Japanese organizations started to notice them.
As a result of its effectiveness, JIT has become a popular technique in the Japanese industry. But before implementing this system, manufacturers should understand the risks and benefits that come along with the implementation. The ability to build strong partnerships with suppliers is key to a successful JIT project. Suppliers can minimize stock-keeping needs and increase delivery speed.
There are two basic types of JIT methods: pull and push. Push is the standard Make to Stock approach to manufacturing. Push puts pressure on other business areas. Retooling can also be costly. Similar to the pull method, it is based on actual demand.
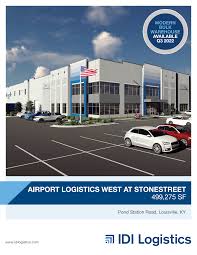
Many companies have used both of these techniques around the globe. The key to a successful implementation of JIT is to empower the workers to solve quality problems. JIT also has to be successful due to the complexity of manufacturing and the delay between manufacturer and supplier deliveries.
Ideally, a firm shouldn't have any stocks of raw materials or finished products. If it does, then it should have a small number of reusable containers called kanban.
JIT aims to minimize waste and maximize both human labor and machine labor. It is crucial to recognize and fix any quality issues before they become serious.
FAQ
How can manufacturing efficiency be improved?
First, determine which factors have the greatest impact on production time. We must then find ways that we can improve these factors. You can start by identifying the most important factors that impact production time. Once you have identified the factors, then try to find solutions.
Is automation important for manufacturing?
Automation is essential for both manufacturers and service providers. It allows them provide faster and more efficient services. It also helps to reduce costs and improve productivity.
What are the requirements to start a logistics business?
You need to have a lot of knowledge and skills to manage a successful logistic business. For clients and suppliers to be successful, you need to have excellent communication skills. You must be able analyze data and draw out conclusions. You need to be able work under pressure and manage stressful situations. To improve efficiency, you must be innovative and creative. Strong leadership qualities are essential to motivate your team and help them achieve their organizational goals.
You should also be organized and efficient to meet tight deadlines.
Can certain manufacturing steps be automated?
Yes! Since ancient times, automation has been in existence. The wheel was invented by the Egyptians thousands of years ago. Nowadays, we use robots for assembly lines.
There are many applications for robotics in manufacturing today. They include:
-
Automated assembly line robots
-
Robot welding
-
Robot painting
-
Robotics inspection
-
Robots that produce products
Automation can be applied to manufacturing in many other ways. 3D printing makes it possible to produce custom products in a matter of days or weeks.
What are the responsibilities of a manufacturing manager
The manufacturing manager should ensure that every manufacturing process is efficient and effective. They should be aware of any issues within the company and respond accordingly.
They should also be able communicate with other departments, such as sales or marketing.
They should be up to date on the latest trends and be able apply this knowledge to increase productivity and efficiency.
What are manufacturing and logistic?
Manufacturing is the process of creating goods from raw materials by using machines and processes. Logistics covers all aspects involved in managing supply chains, including procurement and production planning. As a broad term, manufacturing and logistics often refer to both the creation and delivery of products.
Statistics
- You can multiply the result by 100 to get the total percent of monthly overhead. (investopedia.com)
- [54][55] These are the top 50 countries by the total value of manufacturing output in US dollars for its noted year according to World Bank.[56] (en.wikipedia.org)
- Many factories witnessed a 30% increase in output due to the shift to electric motors. (en.wikipedia.org)
- Job #1 is delivering the ordered product according to specifications: color, size, brand, and quantity. (netsuite.com)
- According to the United Nations Industrial Development Organization (UNIDO), China is the top manufacturer worldwide by 2019 output, producing 28.7% of the total global manufacturing output, followed by the United States, Japan, Germany, and India.[52][53] (en.wikipedia.org)
External Links
How To
How to Use the 5S to Increase Productivity In Manufacturing
5S stands for "Sort", "Set In Order", "Standardize", "Separate" and "Store". Toyota Motor Corporation created the 5S methodology in 1954. This methodology helps companies improve their work environment to increase efficiency.
This method has the basic goal of standardizing production processes to make them repeatable. Cleaning, sorting and packing are all done daily. Through these actions, workers can perform their jobs more efficiently because they know what to expect from them.
There are five steps to implementing 5S, including Sort, Set In Order, Standardize, Separate and Store. Each step involves a different action which leads to increased efficiency. By sorting, for example, you make it easy to find the items later. When you arrange items, you place them together. Next, organize your inventory into categories and store them in containers that are easily accessible. Finally, label all containers correctly.
This requires employees to critically evaluate how they work. Employees need to be able understand their motivations and discover alternative ways to do them. In order to use the 5S system effectively, they must be able to learn new skills.
The 5S Method not only improves efficiency, but it also helps employees to be more productive and happier. As they begin to see improvements, they feel motivated to continue working towards the goal of achieving higher levels of efficiency.