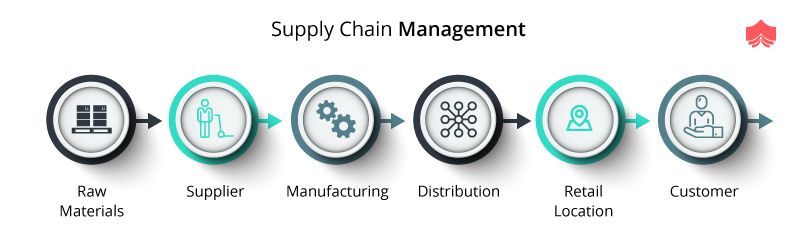
Lean thinking can help improve an organization's performance. This is the process of eliminating wasteful activities and undervalued activities from your business processes. It's also a way to build a lean culture inside your organization. A lean culture consists of a set values, principles, practices, and procedures that improve employee morale, productivity, quality, and quality. It also creates a more sustainable working environment.
Lean thinking starts with identifying value for your customers. This means understanding your customers' needs and the whole value chain. This will allow you to identify the steps involved in your current process. Identifying the steps in different processes will help you to determine if your current processes are inefficient. To visualize the current state of your business, you can use value stream mapping. The value stream map shows the flow of your business, how it works, and the value created by each process.
Lean thinking is all about flow. It involves the ability to quickly switch from one known activity to another. This is particularly important for responding to customer demands. It also reduces inventory backlogs. It allows workers the ability to quickly switch between tasks.
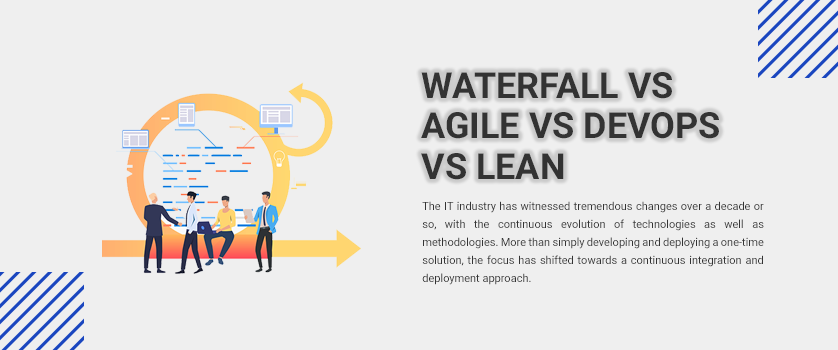
Lean organizations take an equal approach to managing output. They encourage collaboration and clear communication. They encourage quality control and celebrate successes. They reduce unnecessary costs to customers and suppliers.
Lean thinking is a continuous process. Lean thinking can be applied to all types of work. It can help to reduce environmental damage, reduce the waste, and improve employee motivation. Although lean thinking is often used in manufacturing, it can be used in all areas of business.
A culture that encourages lean thinking and collaboration is key to implementing lean production techniques. Culture should have a clear definition and encourage employee motivation. It must also be willing and able to take small steps in the right direction on a daily basis. This is called Kaizen.
Lean thinking is continuous improvement. It requires a kaizen spirit. You must be willing to make small changes every day if you want to improve your product's quality. This can be accomplished either by implementing changes to the organization or using standardized works. Standardized work is a visual representation of the flow of work. It clearly identifies where everything is located. It also allows people to see how obstacles can be overcome to make their work smoother.
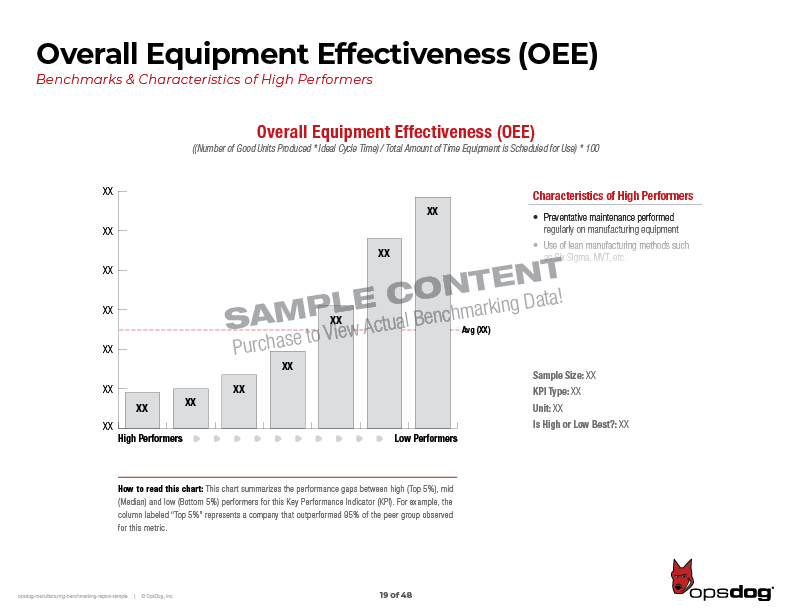
Also, lean production practices should be evaluated in light of other production metrics. The ratio of running time to downtime shows how frequently an asset is available for production. It also shows how frequently planned maintenance is needed. The quality ratio is an indication of the quality of a supplier's products.
It is also important to be aware of the risks involved in the "Just-In-Time" principle. This principle ensures that supplies are delivered at the last minute. This principle also helps you concentrate and focus on the task in hand. But it can cause problems in the industry.
FAQ
Can certain manufacturing steps be automated?
Yes! Yes. Automation has been around since ancient time. The Egyptians invented the wheel thousands of years ago. Today, robots assist in the assembly of lines.
There are many uses of robotics today in manufacturing. These include:
-
Line robots
-
Robot welding
-
Robot painting
-
Robotics inspection
-
Robots create products
Manufacturing can also be automated in many other ways. For instance, 3D printing allows us make custom products and not have to wait for months or even weeks to get them made.
Why is logistics important for manufacturing?
Logistics are an essential component of any business. They enable you to achieve outstanding results by helping manage product flow from raw materials through to finished goods.
Logistics play an important role in reducing costs as well as increasing efficiency.
How can we increase manufacturing efficiency?
First, identify the factors that affect production time. The next step is to identify the most important factors that affect production time. If you don't know where to start, then think about which factor(s) have the biggest impact on production time. Once you've identified them, try to find solutions for each of those factors.
What does it mean to be a manufacturer?
Manufacturing Industries are companies that manufacture products. Consumers are those who purchase these products. These companies employ many processes to achieve this purpose, such as production and distribution, retailing, management and so on. They make goods from raw materials with machines and other equipment. This includes all types manufactured goods such as clothing, building materials, furniture, electronics, tools and machinery.
What is the role of a manager in manufacturing?
The manufacturing manager should ensure that every manufacturing process is efficient and effective. They should be alert for any potential problems in the company and react accordingly.
They should also be able and comfortable communicating with other departments like sales and marketing.
They must also keep up-to-date with the latest trends in their field and be able use this information to improve productivity and efficiency.
What is the responsibility of a logistics manager?
Logistics managers make sure all goods are delivered on schedule and without damage. This is done using his/her knowledge of the company's products. He/she must also ensure sufficient stock to meet the demand.
How can we reduce manufacturing overproduction?
The key to reducing overproduction lies in developing better ways to manage inventory. This would reduce the time spent on unproductive activities like purchasing, storing and maintaining excess stock. By doing this, we could free up resources for other productive tasks.
This can be done by using a Kanban system. A Kanban board, a visual display to show the progress of work, is called a Kanban board. A Kanban system allows work items to move through several states before reaching their final destination. Each state has a different priority level.
If work is moving from one stage to the other, then the current task can be completed and moved on to the next. It is possible to keep a task in the beginning stages until it gets to the end.
This allows work to move forward and ensures that no work is missed. A Kanban board allows managers to monitor how much work is being completed at any given moment. This information allows them to adjust their workflow based on real-time data.
Lean manufacturing is another way to manage inventory levels. Lean manufacturing works to eliminate waste throughout every stage of the production chain. Anything that does nothing to add value to a product is waste. Here are some examples of common types.
-
Overproduction
-
Inventory
-
Packaging that is not necessary
-
Exceed materials
By implementing these ideas, manufacturers can improve efficiency and cut costs.
Statistics
- Job #1 is delivering the ordered product according to specifications: color, size, brand, and quantity. (netsuite.com)
- It's estimated that 10.8% of the U.S. GDP in 2020 was contributed to manufacturing. (investopedia.com)
- [54][55] These are the top 50 countries by the total value of manufacturing output in US dollars for its noted year according to World Bank.[56] (en.wikipedia.org)
- According to the United Nations Industrial Development Organization (UNIDO), China is the top manufacturer worldwide by 2019 output, producing 28.7% of the total global manufacturing output, followed by the United States, Japan, Germany, and India.[52][53] (en.wikipedia.org)
- According to a Statista study, U.S. businesses spent $1.63 trillion on logistics in 2019, moving goods from origin to end user through various supply chain network segments. (netsuite.com)
External Links
How To
How to use 5S in Manufacturing to Increase Productivity
5S stands for "Sort", "Set In Order", "Standardize", "Separate" and "Store". Toyota Motor Corporation created the 5S methodology in 1954. It assists companies in improving their work environments and achieving higher efficiency.
The basic idea behind this method is to standardize production processes, so they become repeatable, measurable, and predictable. Cleaning, sorting and packing are all done daily. Because workers know what they can expect, this helps them perform their jobs more efficiently.
There are five steps that you need to follow in order to implement 5S. Each step involves a different action which leads to increased efficiency. Sorting things makes it easier to find them later. When you arrange items, you place them together. Once you have separated your inventory into groups and organized them, you will store these groups in easily accessible containers. Labeling your containers will ensure that everything is correctly labeled.
Employees need to reflect on how they do their jobs. Employees need to understand the reasons they do certain jobs and determine if there is a better way. In order to use the 5S system effectively, they must be able to learn new skills.
In addition to increasing efficiency, the 5S method also improves morale and teamwork among employees. As they begin to see improvements, they feel motivated to continue working towards the goal of achieving higher levels of efficiency.