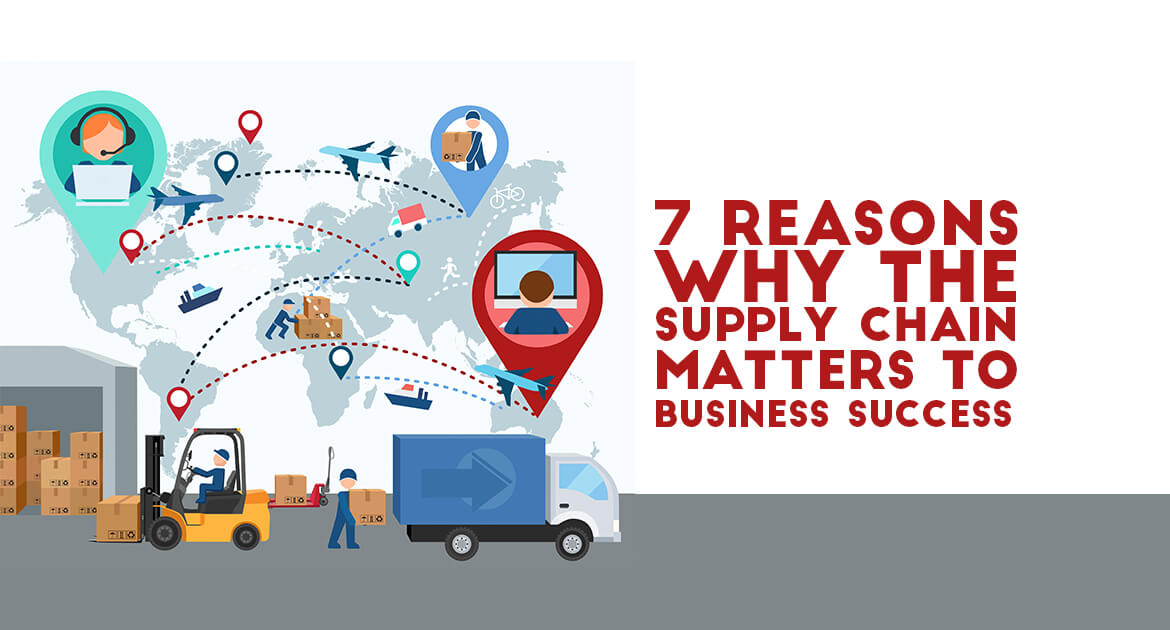
A planning engineer (also known as a building planner) is responsible for the planning and scheduling of the construction process. They plan for the entire project, which includes finding the right materials and estimating how long it will last. They will also decide the best order for each stage in a project.
Career Plans for a Planning Engineer
If you want to pursue a career in planning engineering, it is important that you learn about the position and what skills are required. Generally, you need a bachelor's degree in engineering or a related field and several years of experience. Some certifications are required by industry organizations.
How to Become A Planning Engineer
This occupation typically requires a bachelor's in engineering or another relevant field. A strong knowledge of computer programs and the construction industry is also required. You will need to manage a team and perform quality checks on your projects.
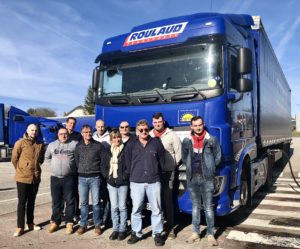
What to Look For in a Planning Engineering
When reviewing your resume, it is important to know what the hiring manager wants. Include skills such as good communication and organizational skills, ability to meet deadlines and experience working on construction sites.
What To Expect From A Planning Engineer Role
Planned engineers usually work from a computer-intensive office environment. They may also need to travel around to construction sites to ensure all work is completed properly and on schedule. They may be required to work on site during construction, which means they will need to be able to tolerate noisy and dirty conditions.
What to Expect in a Career as a Planning Engineer
As you gain more experience, your career as a planner engineer will progress to progressively higher positions. You can move up to a position of operations manager, project manger, or independent consultant. Some planning engineers decide to pursue careers as salespeople or marketers with an engineering company.
What to expect from a career as a planner engineer
The average annual salary for a planner engineer is about $150,000, but it can vary depending on the experience you have and the size and sector of the business where you work. Many planning engineer earn bonuses for completing and meeting projects.
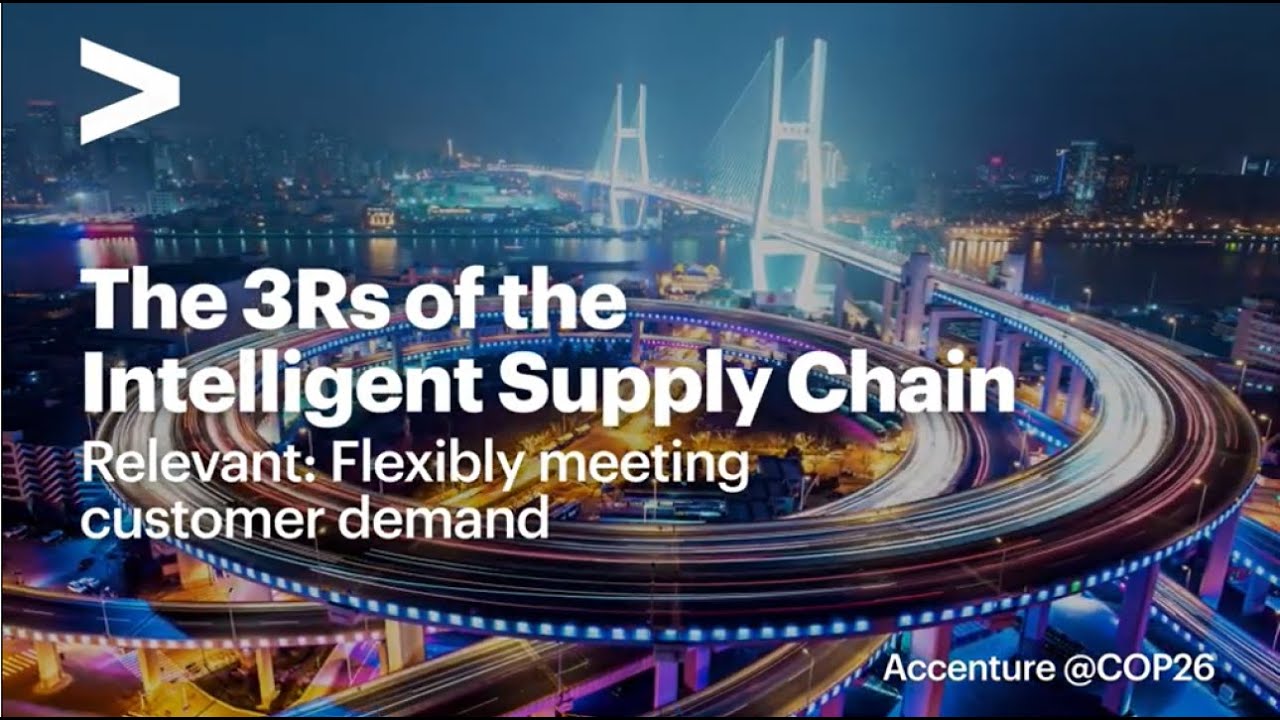
How to Get a Job as a Planning Engineer
A planning engineer's job is to design and plan all aspects of the project, starting from the beginning. They work with a team made up of architects, engineers and designers to produce plans that assist businesses in achieving their goals. They develop long-term strategy for their organization, including identifying new business opportunities and deciding on which technologies to invest next.
FAQ
Can certain manufacturing steps be automated?
Yes! Automation has been around since ancient times. The Egyptians invent the wheel thousands of year ago. Nowadays, we use robots for assembly lines.
There are many uses of robotics today in manufacturing. These include:
-
Line robots
-
Robot welding
-
Robot painting
-
Robotics inspection
-
Robots that produce products
There are many other examples of how manufacturing could benefit from automation. For example, 3D printing allows us to make custom products without having to wait for weeks or months to get them manufactured.
What does warehouse refer to?
A warehouse is an area where goods are stored before being sold. It can be an indoor space or an outdoor area. In some cases, it may be a combination of both.
What are the logistics products?
Logistics is the process of moving goods from one point to another.
They include all aspects associated with transport including packaging, loading transporting, unloading storage, warehousing inventory management customer service, distribution returns and recycling.
Logisticians ensure that the right product reaches the right place at the right time and under safe conditions. They assist companies with their supply chain efficiency through information on demand forecasts. Stock levels, production times, and availability.
They can also track shipments in transit and monitor quality standards.
What does it take for a logistics enterprise to succeed?
To run a successful logistics company, you need a lot knowledge and skills. To communicate effectively with clients and suppliers, you must be able to communicate well. You should be able analyse data and draw inferences. You will need to be able handle pressure well and work in stressful situations. To improve efficiency, you must be innovative and creative. You need to have strong leadership qualities to motivate team members and direct them towards achieving organizational goals.
It is also important to be efficient and well organized in order meet deadlines.
What is the role of a production manager?
A production planner ensures all aspects of the project are delivered on time, within budget, and within scope. They ensure that the product or service is of high quality and meets client requirements.
What are the 7 R's of logistics?
The acronym 7R's for Logistics stands to represent the seven basic principles in logistics management. It was developed by International Association of Business Logisticians (IABL), and published as part of their "Seven Principles of Logistics Management Series" in 2004.
The following letters form the acronym:
-
Responsive - ensure all actions are legal and not harmful to others.
-
Reliable - Have confidence in your ability to fulfill all of your commitments.
-
Be responsible - Use resources efficiently and avoid wasting them.
-
Realistic - consider all aspects of operations, including cost-effectiveness and environmental impact.
-
Respectful – Treat others fairly and equitably.
-
Be resourceful: Look for opportunities to save money or increase productivity.
-
Recognizable - provide customers with value-added services.
Statistics
- You can multiply the result by 100 to get the total percent of monthly overhead. (investopedia.com)
- In the United States, for example, manufacturing makes up 15% of the economic output. (twi-global.com)
- According to a Statista study, U.S. businesses spent $1.63 trillion on logistics in 2019, moving goods from origin to end user through various supply chain network segments. (netsuite.com)
- It's estimated that 10.8% of the U.S. GDP in 2020 was contributed to manufacturing. (investopedia.com)
- [54][55] These are the top 50 countries by the total value of manufacturing output in US dollars for its noted year according to World Bank.[56] (en.wikipedia.org)
External Links
How To
How to use 5S to increase Productivity in Manufacturing
5S stands for "Sort", "Set In Order", "Standardize", "Separate" and "Store". Toyota Motor Corporation created the 5S methodology in 1954. It improves the work environment and helps companies to achieve greater efficiency.
This approach aims to standardize production procedures, making them predictable, repeatable, and easily measurable. It means tasks like cleaning, sorting or packing, labeling, and storing are done every day. These actions allow workers to perform their job more efficiently, knowing what to expect.
There are five steps to implementing 5S, including Sort, Set In Order, Standardize, Separate and Store. Each step is a different action that leads to greater efficiency. For example, when you sort things, you make them easy to find later. You arrange items by placing them in an order. After you have divided your inventory into groups you can store them in easy-to-reach containers. Finally, label all containers correctly.
This requires employees to critically evaluate how they work. Employees need to understand the reasons they do certain jobs and determine if there is a better way. They will need to develop new skills and techniques in order for the 5S system to be implemented.
The 5S Method not only improves efficiency, but it also helps employees to be more productive and happier. As they begin to see improvements, they feel motivated to continue working towards the goal of achieving higher levels of efficiency.