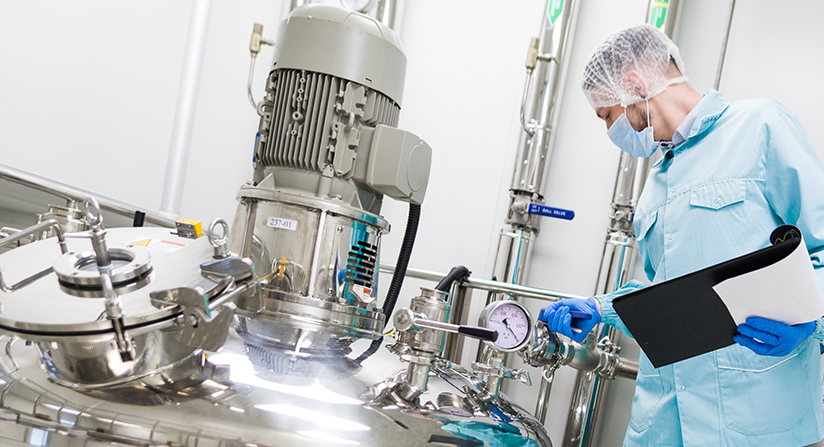
The state-by-state list shows a surprising trend. The top states are the ones you would expect to be there, like the southeastern. This trend is changing. There are many states that show you can compromise on cost and quality to get the best deals. This trend shows there are many factors that influence a state’s ability to attract manufacturing jobs. So how do you choose the best place for your business?
Group Five
The following list contains a listing of all Group Five manufacturers, organized by state. Group Five's portfolio includes steel pipes, structural components, and industrial engineering products. The company provides pipe design services and offers the best price/quality ratio for steel thickness and grades. It also stiffens thin-walled pipelines. The company makes use of the most recent CAD systems to design your pipes.
Group Three
According to the United States Census Bureau approximately 50,000 manufacturing companies are in Group Three. This group has low unemployment rates, high economic growth and has a low rate of GDP growth. This is due to the fact that most of these manufacturers are small. These limitations aside, the data can still serve as a guide. Below are the top-rated manufacturers in each state. Continue reading for more information.
Audi, Mercedes-Benz, and BMW are the biggest three manufacturers in Europe. Honda and Toyota fall to fifth and fifth, respectively. However, the Detroit Three have reclaimed the Big Three title. This table shows the sales figures for each of these carmakers. The link below will take you to the list of top-selling cars in each state. There are many models that these manufacturers offer, including SUVs, midsize sedans and minivans.
FAQ
What is the importance of logistics in manufacturing?
Logistics are an essential part of any business. They enable you to achieve outstanding results by helping manage product flow from raw materials through to finished goods.
Logistics also play a major role in reducing costs and increasing efficiency.
What is manufacturing and logistics?
Manufacturing is the process of creating goods from raw materials by using machines and processes. Logistics covers all aspects involved in managing supply chains, including procurement and production planning. As a broad term, manufacturing and logistics often refer to both the creation and delivery of products.
How can manufacturing excess production be decreased?
It is essential to find better ways to manage inventory to reduce overproduction. This would reduce time spent on activities such as purchasing, stocking, and maintaining excess stock. We could use these resources to do other productive tasks.
You can do this by adopting a Kanban method. A Kanban Board is a visual display that tracks work progress. In a Kanban system, work items move through a sequence of states until they reach their final destination. Each state represents a different priority.
To illustrate, work can move from one stage or another when it is complete enough for it to be moved to a new stage. But if a task remains in the beginning stages it will stay that way until it reaches its end.
This keeps work moving and ensures no work is lost. Managers can monitor the work being done by Kanban boards to see what is happening at any given time. This information allows managers to adjust their workflow based off real-time data.
Lean manufacturing is another way to manage inventory levels. Lean manufacturing emphasizes eliminating waste in all phases of production. Waste includes anything that does not add value to the product. Here are some examples of common types.
-
Overproduction
-
Inventory
-
Unnecessary packaging
-
Excess materials
These ideas will help manufacturers increase efficiency and lower costs.
What does manufacturing industry mean?
Manufacturing Industries is a group of businesses that produce goods for sale. The people who buy these products are called consumers. These companies use various processes such as production, distribution, retailing, management, etc., to fulfill this purpose. They manufacture goods from raw materials using machines and other equipment. This covers all types of manufactured goods including clothing, food, building supplies and furniture, as well as electronics, tools, machinery, vehicles and pharmaceuticals.
Statistics
- It's estimated that 10.8% of the U.S. GDP in 2020 was contributed to manufacturing. (investopedia.com)
- Many factories witnessed a 30% increase in output due to the shift to electric motors. (en.wikipedia.org)
- [54][55] These are the top 50 countries by the total value of manufacturing output in US dollars for its noted year according to World Bank.[56] (en.wikipedia.org)
- In 2021, an estimated 12.1 million Americans work in the manufacturing sector.6 (investopedia.com)
- (2:04) MTO is a production technique wherein products are customized according to customer specifications, and production only starts after an order is received. (oracle.com)
External Links
How To
How to use lean manufacturing in the production of goods
Lean manufacturing refers to a method of managing that seeks to improve efficiency and decrease waste. It was developed by Taiichi Okono in Japan, during the 1970s & 1980s. TPS founder Kanji Takoda awarded him the Toyota Production System Award (TPS). Michael L. Watkins published the original book on lean manufacturing, "The Machine That Changed the World," in 1990.
Lean manufacturing can be described as a set or principles that are used to improve quality, speed and cost of products or services. It emphasizes reducing defects and eliminating waste throughout the value chain. Lean manufacturing is called just-in-time (JIT), zero defect, total productive maintenance (TPM), or 5S. Lean manufacturing focuses on eliminating non-value-added activities such as rework, inspection, and waiting.
Lean manufacturing can help companies improve their product quality and reduce costs. Additionally, it helps them achieve their goals more quickly and reduces employee turnover. Lean manufacturing has been deemed one of the best ways to manage the entire value-chain, including customers, distributors as well retailers and employees. Lean manufacturing practices are widespread in many industries. For example, Toyota's philosophy underpins its success in automobiles, electronics, appliances, healthcare, chemical engineering, aerospace, paper, food, etc.
Five principles are the basis of lean manufacturing:
-
Define Value- Identify the added value your company brings to society. What makes you stand out from your competitors?
-
Reduce waste - Get rid of any activity that does not add value to the supply chain.
-
Create Flow. Ensure that your work is uninterrupted and flows seamlessly.
-
Standardize & simplify - Make processes consistent and repeatable.
-
Develop Relationships: Establish personal relationships both with internal and external stakeholders.
Although lean manufacturing isn't a new concept in business, it has gained popularity due to renewed interest in the economy after the 2008 global financial crisis. Many businesses have adopted lean manufacturing techniques to help them become more competitive. Many economists believe lean manufacturing will play a major role in economic recovery.
Lean manufacturing, which has many benefits, is now a standard practice in the automotive industry. These include higher customer satisfaction levels, reduced inventory levels as well as lower operating costs.
You can apply Lean Manufacturing to virtually any aspect of your organization. This is because it ensures efficiency and effectiveness in all stages of the value chain.
There are three main types:
-
Just-in-Time Manufacturing: Also known as "pull systems", this type of lean manufacturing uses just-in-time manufacturing (JIT). JIT means that components are assembled at the time of use and not manufactured in advance. This approach aims to reduce lead times, increase the availability of parts, and reduce inventory.
-
Zero Defects Manufacturing: ZDM ensures that no defective units leave the manufacturing plant. It is better to repair a part than have it removed from the production line if it needs to be fixed. This is true even for finished products that only require minor repairs prior to shipping.
-
Continuous Improvement (CI), also known as Continuous Improvement, aims at improving the efficiency of operations through continuous identification and improvement to minimize or eliminate waste. Continuous improvement refers to continuous improvement of processes as well people and tools.