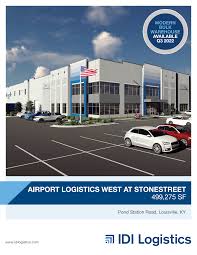
Michigan's unemployment rate is among the highest in the Midwest. The Unemployment insurance system was created to aid families in economic downturns. Unfortunately, the system does not reflect current trends in workforce. Many of the policies adopted by the state are outdated, especially those that protect Black and Latinx workers and women.
Michigan's maximum weekly benefit has only been raised once since 1995. It is also the only state that offers less than 26 weeks of unemployment benefit. In reality, only 10 weeks are provided. If a person loses their job, they may fall into poverty. Michigan is not doing enough to ensure all unemployed workers have unemployment insurance.
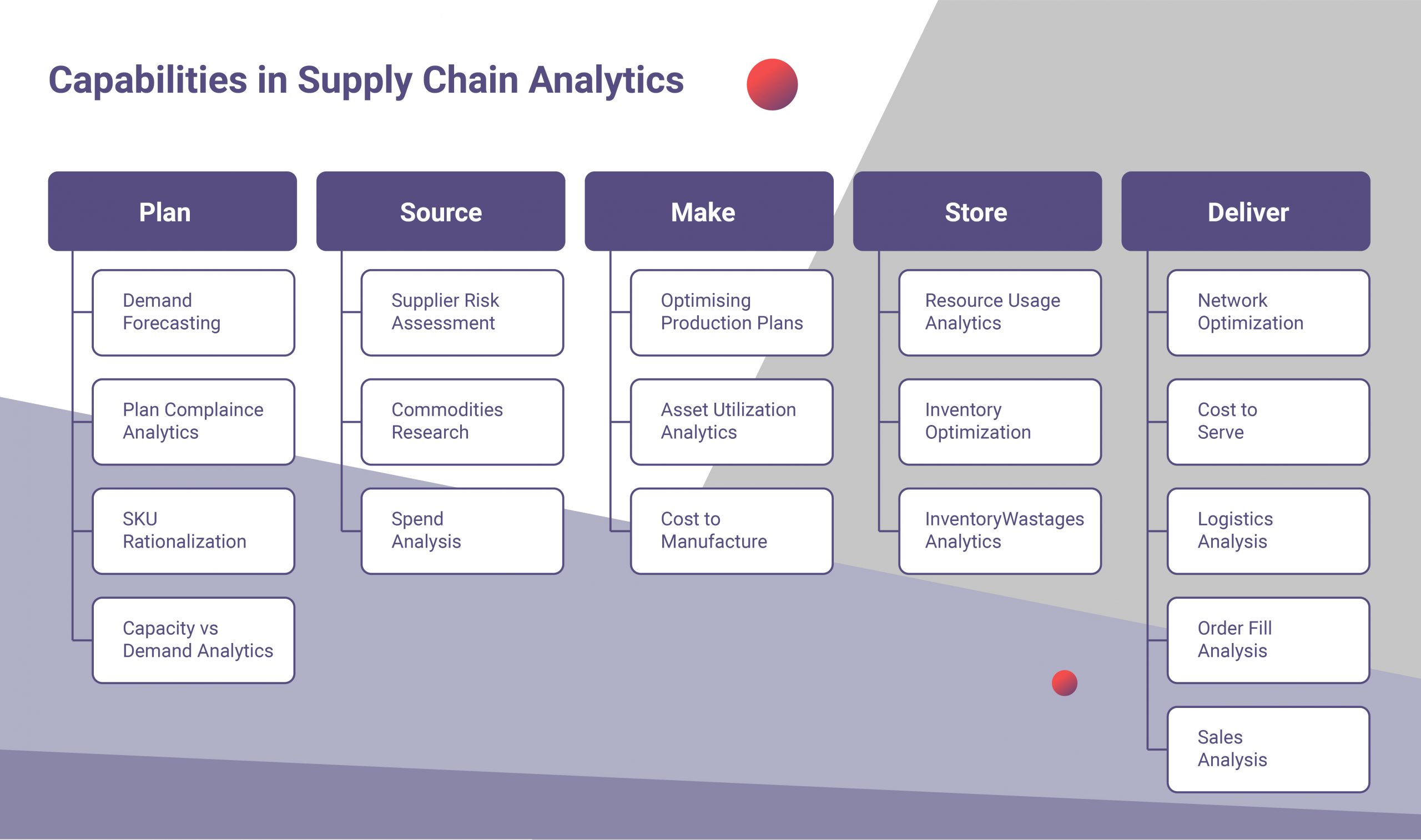
Michigan has a minimum wage requirement. Workers must earn a minimum wage at least $5667 per week in order to be eligible for UI. This is more than the average wage in other Midwestern states. While this isn't a bad thing by itself, the State of Michigan demands a minimum wage of at least a few hundred dollars per workweek.
The Advisory Council’s "two-thirds" rule says that Michigan's unemployment payments should not exceed 50 percent of weekly average wages. Instead, the state has a maximum benefit of 34%. This means that Michigan is far behind other states and should be raising its Unemployment Insurance game. Wisconsin, Iowa, Pennsylvania and other states offer maximum benefits that are at or below 50% of the average wage.
Michigan's Unemployment Compensation program should be enhanced by the Michigan Legislature. This is a great way to reduce racial disparities and increase the safety net for all workers. Also, the state should consider expanding the time period for which workers can apply to benefits. An extended base period can be a great tool to increase federal funding for skill training and employment search expenses. It would increase the chances that more people are able to access the assistance they require.
Although Michigan's unemployment rates are higher than those in other states, they have been decreasing since 2009. New figures from the state show that the unemployment rate is now at 6.1 percent as of January 2021. Since then, the rate has remained relatively stable. Michigan had one of the worst unemployment rates in America during the recession. However, with strong investments made in the Unemployment Insurance system, more workers are likely to be able find employment before the 26-week threshold is reached.
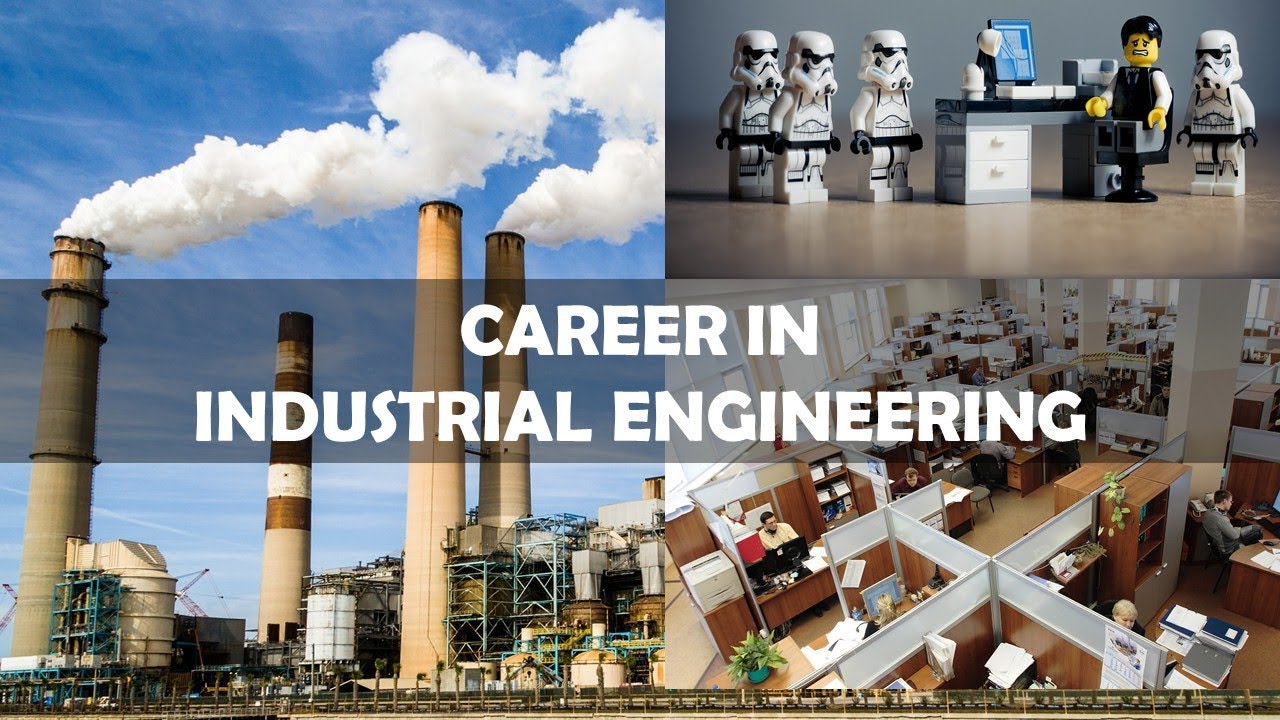
The minimum wage that is required to qualify in the United States for unemployment benefits, which is available only in the Midwest, is the highest. Michigan's maximum UI benefits are the lowest in the country.
FAQ
What is production planning?
Production Planning refers to the development of a plan for every aspect of production. This document will ensure everything is in order and ready to go when you need it. This document should also include information on how to get the best result on set. This includes information on shooting times, locations, cast lists and crew details.
First, you need to plan what you want to film. You may already know where you want the film to be shot, or perhaps you have specific locations and sets you wish to use. Once you have identified your locations and scenes, you can start working out which elements you require for each scene. You might decide you need a car, but not sure what make or model. To narrow your options, you can search online for available models.
Once you have found the right vehicle, you can think about adding accessories. Do you need people sitting in the front seats? Or perhaps you need someone walking around the back of the car? Maybe you'd like to change the interior from black to a white color. These questions will help to determine the style and feel of your car. It is also worth considering the types of shots that you wish to take. Do you want to film close-ups, or wider angles? Perhaps you want to show the engine or the steering wheel? All of these things will help you identify the exact style of car you want to film.
Once you have all the information, you are ready to create a plan. A schedule will tell you when you need to start shooting and when you need to finish. The schedule will show you when to get there, what time to leave, and when to return home. Everyone will know what they need and when. It is possible to make arrangements in advance for additional staff if you are looking to hire. There is no point in hiring someone who won't turn up because you didn't let him know.
It is important to calculate the amount of filming days when you are creating your schedule. Some projects may only take a couple of days, while others could last for weeks. When creating your schedule, be aware of whether you need more shots per day. Shooting multiple takes over the same location will increase costs and take longer to complete. If you are unsure if you need multiple takes, it is better to err on the side of caution and shoot fewer takes rather than risk wasting money.
Budgeting is another crucial aspect of production plan. As it will allow you and your team to work within your financial means, setting a realistic budget is crucial. Keep in mind that you can always reduce your budget if you face unexpected difficulties. It is important to not overestimate how much you will spend. You will end up spending less money if you underestimate the cost of something.
Planning production is a tedious process. Once you have a good understanding of how everything works together, planning future projects becomes easy.
What makes a production planner different from a project manger?
The major difference between a Production Planner and a Project Manager is that a Project Manager is often the person responsible for organizing and planning the entire project. While a Production Planner is involved mainly in the planning stage,
What are the 4 types manufacturing?
Manufacturing refers the process of turning raw materials into useful products with machines and processes. It involves many different activities such as designing, building, testing, packaging, shipping, selling, servicing, etc.
Is automation important in manufacturing?
Not only are service providers and manufacturers important, but so is automation. They can provide services more quickly and efficiently thanks to automation. In addition, it helps them reduce costs by reducing human errors and improving productivity.
What are the 7 Rs of logistics?
The acronym 7R's for Logistics stands to represent the seven basic principles in logistics management. It was developed and published by the International Association of Business Logisticians in 2004 as part of the "Seven Principles of Logistics Management".
The acronym is made up of the following letters:
-
Responsible - to ensure that all actions are within the legal requirements and are not detrimental to others.
-
Reliable – have faith in your ability and capability to keep promises.
-
It is reasonable to use resources efficiently and not waste them.
-
Realistic - Take into consideration all aspects of operations including cost-effectiveness, environmental impact, and other factors.
-
Respectful – Treat others fairly and equitably.
-
Responsive - Look for ways to save time and increase productivity.
-
Recognizable is a company that provides customers with value-added solutions.
What are the responsibilities of a manufacturing manager
Manufacturing managers must ensure that manufacturing processes are efficient, effective, and cost-effective. They should be aware of any issues within the company and respond accordingly.
They should also know how to communicate with other departments such as sales and marketing.
They should be up to date on the latest trends and be able apply this knowledge to increase productivity and efficiency.
What skills do production planners need?
To become a successful production planner, you need to be organized, flexible, and able to multitask. You must also be able to communicate effectively with clients and colleagues.
Statistics
- According to a Statista study, U.S. businesses spent $1.63 trillion on logistics in 2019, moving goods from origin to end user through various supply chain network segments. (netsuite.com)
- You can multiply the result by 100 to get the total percent of monthly overhead. (investopedia.com)
- It's estimated that 10.8% of the U.S. GDP in 2020 was contributed to manufacturing. (investopedia.com)
- Many factories witnessed a 30% increase in output due to the shift to electric motors. (en.wikipedia.org)
- [54][55] These are the top 50 countries by the total value of manufacturing output in US dollars for its noted year according to World Bank.[56] (en.wikipedia.org)
External Links
How To
Six Sigma in Manufacturing:
Six Sigma refers to "the application and control of statistical processes (SPC) techniques in order to achieve continuous improvement." Motorola's Quality Improvement Department developed it at their Tokyo plant in Japan in 1986. Six Sigma's core idea is to improve the quality of processes by standardizing and eliminating defects. Many companies have adopted Six Sigma in recent years because they believe that there are no perfect products and services. Six Sigma's main objective is to reduce variations from the production average. It is possible to measure the performance of your product against an average and find the percentage of time that it differs from the norm. If there is a significant deviation from the norm, you will know that something needs to change.
Understanding the nature of variability in your business is the first step to Six Sigma. Once you've understood that, you'll want to identify sources of variation. These variations can also be classified as random or systematic. Random variations occur when people do mistakes. Symmetrical variations are caused due to factors beyond the process. Random variations would include, for example, the failure of some widgets to fall from the assembly line. You might notice that your widgets always fall apart at the same place every time you put them together.
Once you have identified the problem, you can design solutions. This could mean changing your approach or redesigning the entire process. Once you have implemented the changes, it is important to test them again to ensure they work. If they didn't work, then you'll need to go back to the drawing board and come up with another plan.