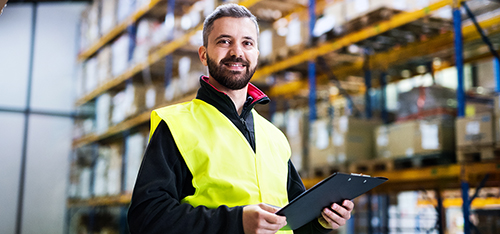
Kaizen isn't always easy to integrate into manufacturing processes. It is slow and takes time to get inventory and make sure everyone is on the same page. The length of this improvement project depends on the type of company and participation level. Follow the correct implementation methods and obtain the resources you need to ensure your manufacturing process improvement project is a success. To make this strategy work, create a culture within your company that promotes continuous improvement.
Creating a culture in the company that is focused on improving
According to a Gallup poll, only 32% of employees in the United States are engaged in their job. 17.2% were actively disengaged. Kaizen culture encourages employee engagement which in turn will improve processes, reduce turnover and promote innovation. In addition, engaged employees are more likely to contribute ideas and innovate, leading to higher productivity and customer satisfaction. Kaizen culture provides many other benefits than reducing waste and improving productivity.
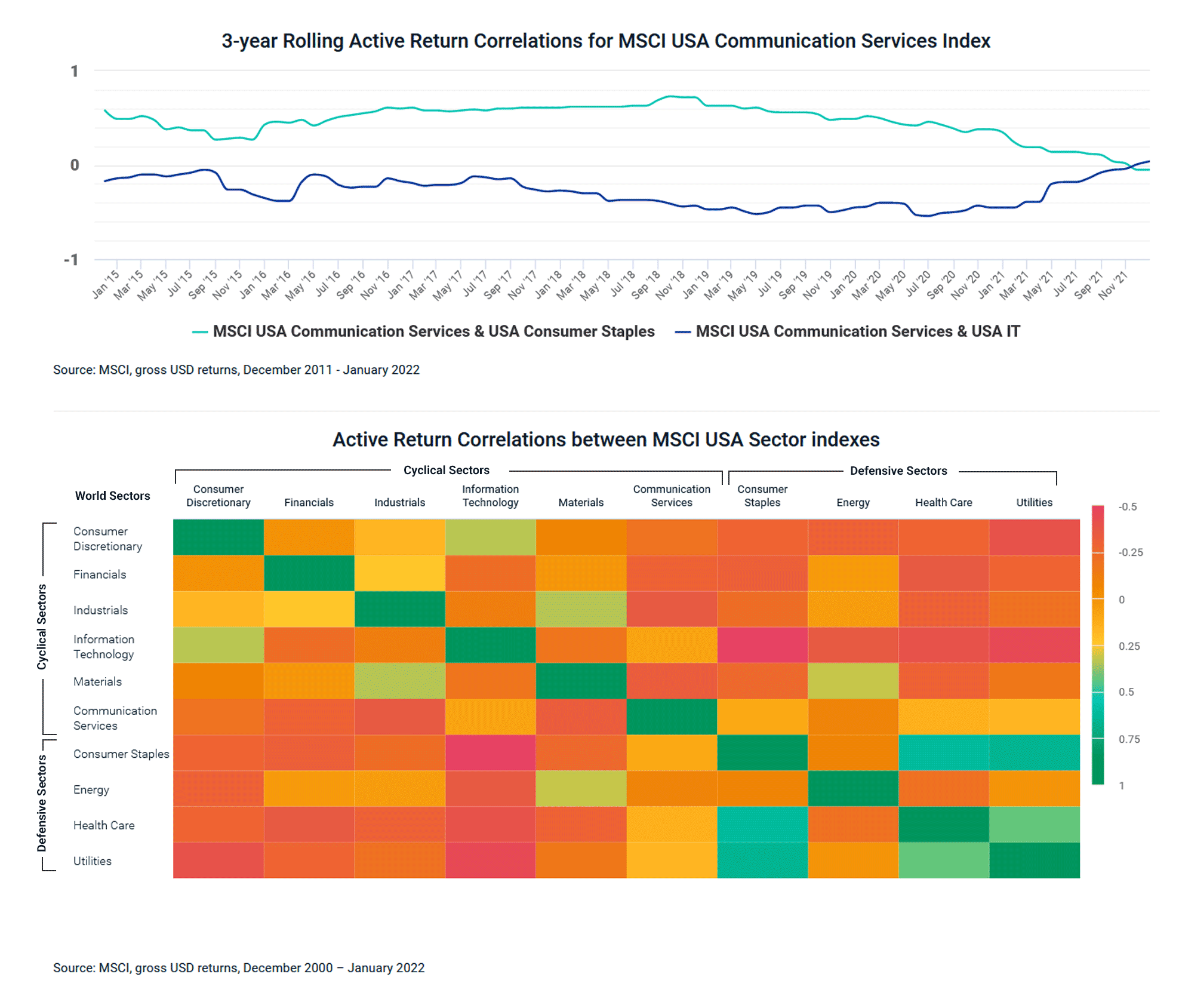
Kaizen stands for continuous improvement in all aspects of a company's business. Kaizen isn't about making huge, unproductive changes. It's about incremental improvement. Kaizen can help reduce costs, increase productivity, improve quality, and improve customer satisfaction when implemented properly. It is also a great way to increase employee morale.
Manufacturing obstacles that prevent kaizen implementation
There are some downsides to kaizen implementation. First, implementing Kaizen requires substantial changes to a company's management systems. It can be hard to reverse these changes after the changes have been made. Second, many businesses find it difficult or impossible to modify their existing work practices. This could hinder the implementation of kaizen.
Another common obstacle is that many manufacturers operate on a "feast or famine" cycle. When demand drops for their products and they don't have enough people to hire them, the machine shop will be in trouble. In such a situation, they'll have to lay off employees and close their doors. Implementing kaizen, which is continuous improvement, can help these machine shops steer clear of the "feast/famine" cycle. Kaizen will improve the efficiency of a shop and enable it to produce more product.
Kaizen implementation success rate in manufacturing
Statistics show that Kaizen implementation in the manufacturing industry is very low. Only 10% of manufacturing firms reported positive results after implementing Kaizen. This does not mean that Kaizen implementation is useless. Implementing Kaizen is an integral part of lean manufacturing. These are some ways to improve your manufacturing company's success rate.
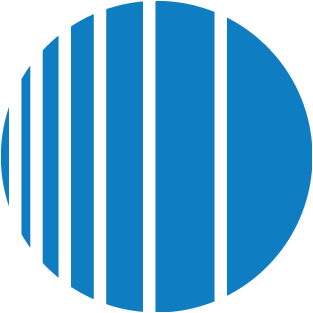
To start kaizen, one must first understand the current state processes. During the first step, data is collected and analyzed to identify the highest priorities. Then, improvements are tested and verified by doing a before-and-after comparison. An analysis of the benefit-to-cost ratio can be used to analyze the overall impact of an improvement or the entire Kaizen process. To gauge the effectiveness of the program, it is important to keep track of the results of kaizen cycle for between 60 and 90 days.
FAQ
What does it mean to be a manufacturer?
Manufacturing Industries is a group of businesses that produce goods for sale. The people who buy these products are called consumers. This is accomplished by using a variety of processes, including production, distribution and retailing. They produce goods from raw materials by using machines and other machinery. This includes all types of manufactured goods, including food items, clothing, building supplies, furniture, toys, electronics, tools, machinery, vehicles, pharmaceuticals, medical devices, chemicals, and many others.
What are the four types of manufacturing?
Manufacturing refers the process of turning raw materials into useful products with machines and processes. It can involve many activities like designing, manufacturing, testing packaging, shipping, selling and servicing.
What are the main products of logistics?
Logistics is the process of moving goods from one point to another.
These include all aspects related to transport such as packaging, loading and transporting, storing, transporting, unloading and warehousing inventory management, customer service. Distribution, returns, recycling are some of the options.
Logisticians ensure that products reach the right destination at the right moment and under safe conditions. Logisticians assist companies in managing their supply chains by providing information such as demand forecasts, stock levels and production schedules.
They can also track shipments in transit and monitor quality standards.
Statistics
- Many factories witnessed a 30% increase in output due to the shift to electric motors. (en.wikipedia.org)
- You can multiply the result by 100 to get the total percent of monthly overhead. (investopedia.com)
- According to a Statista study, U.S. businesses spent $1.63 trillion on logistics in 2019, moving goods from origin to end user through various supply chain network segments. (netsuite.com)
- In the United States, for example, manufacturing makes up 15% of the economic output. (twi-global.com)
- [54][55] These are the top 50 countries by the total value of manufacturing output in US dollars for its noted year according to World Bank.[56] (en.wikipedia.org)
External Links
How To
How to use Lean Manufacturing in the production of goods
Lean manufacturing is an approach to management that aims for efficiency and waste reduction. It was developed by Taiichi Okono in Japan, during the 1970s & 1980s. TPS founder Kanji Takoda awarded him the Toyota Production System Award (TPS). Michael L. Watkins published the first book on lean manufacturing in 1990.
Lean manufacturing is often defined as a set of principles used to improve the quality, speed, and cost of products and services. It is about eliminating defects and waste from all stages of the value stream. Lean manufacturing is called just-in-time (JIT), zero defect, total productive maintenance (TPM), or 5S. Lean manufacturing is about eliminating activities that do not add value, such as inspection, rework, and waiting.
Lean manufacturing improves product quality and costs. It also helps companies reach their goals quicker and decreases employee turnover. Lean manufacturing is considered one of the most effective ways to manage the entire value chain, including suppliers, customers, distributors, retailers, and employees. Many industries worldwide use lean manufacturing. Toyota's philosophy is a great example of this. It has helped to create success in automobiles as well electronics, appliances and healthcare.
Five principles are the basis of lean manufacturing:
-
Define value - Find out what your business contributes to society, and what makes it different from other competitors.
-
Reduce waste - Get rid of any activity that does not add value to the supply chain.
-
Create Flow - Make sure work runs smoothly without interruptions.
-
Standardize and simplify - Make your processes as consistent as possible.
-
Build relationships - Develop and maintain personal relationships with both your internal and external stakeholders.
Although lean manufacturing isn't a new concept in business, it has gained popularity due to renewed interest in the economy after the 2008 global financial crisis. To increase their competitiveness, many businesses have turned to lean manufacturing. Some economists even believe that lean manufacturing can be a key factor in economic recovery.
Lean manufacturing, which has many benefits, is now a standard practice in the automotive industry. These include improved customer satisfaction, reduced inventory levels, lower operating costs, increased productivity, and better overall safety.
Any aspect of an enterprise can benefit from Lean manufacturing. Lean manufacturing is most useful in the production sector of an organisation because it ensures that each step in the value-chain is efficient and productive.
There are three main types:
-
Just-in-Time Manufacturing: Also known as "pull systems", this type of lean manufacturing uses just-in-time manufacturing (JIT). JIT stands for a system where components are assembled on the spot rather than being made in advance. This approach reduces lead time, increases availability and reduces inventory.
-
Zero Defects Manufacturing: ZDM ensures that no defective units leave the manufacturing plant. If a part needs to be fixed during the assembly line, it should be repaired rather than scrapped. This also applies to finished products that need minor repairs before being shipped.
-
Continuous Improvement (CI: Continuous improvement aims to increase the efficiency of operations by constantly identifying and making improvements to reduce or eliminate waste. Continuous Improvement involves continuous improvement of processes.