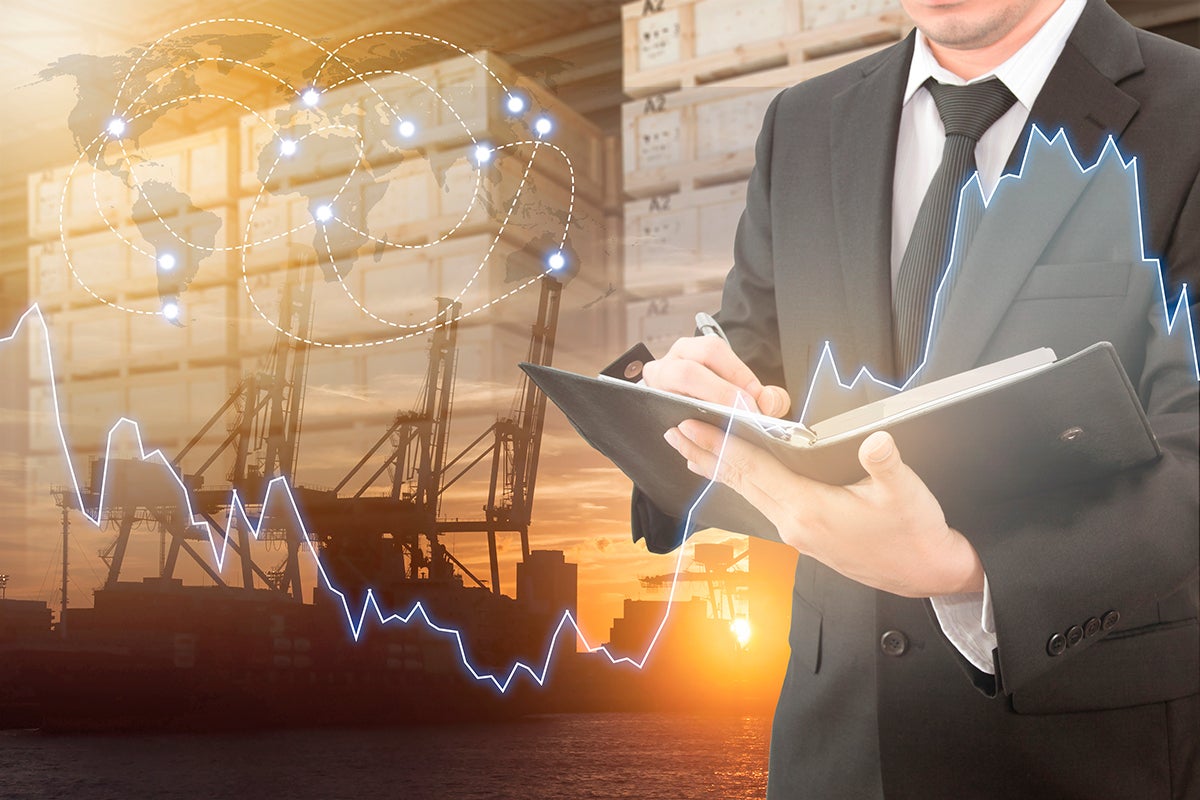
Flow is when the production process flows without interruption. Every step adds worth to the product. Goods flow smoothly through the production cycle without being hampered. In many companies, the production of a specific quantity of stock is planned out so that production orders can be fulfilled as efficiently as possible. This is known as "push production" in Lean Manufacturing. Here are the key elements of flow:
Manufacturing just-in-time
The dominant paradigm of "just in time" manufacturing was prevalent when lean manufacturing was introduced to the U.S. late 1970s. This concept is not practical, and it does not have the greatest benefits. It takes many skills and new mindsets to reduce costs and increase efficiency. However, it is well worth pursuing if you want to reap the full benefits.
Among the most important aspects of just-in-time manufacturing is standardizing procedures and working with smaller lots. To promote just-in–time thinking, a well-planned layout of the facility is essential. Cellular manufacturing is one example of a way to improve production flow. Cellular organization can make it easier to move materials around. Long changeover times should be avoided by just-in time manufacturers.
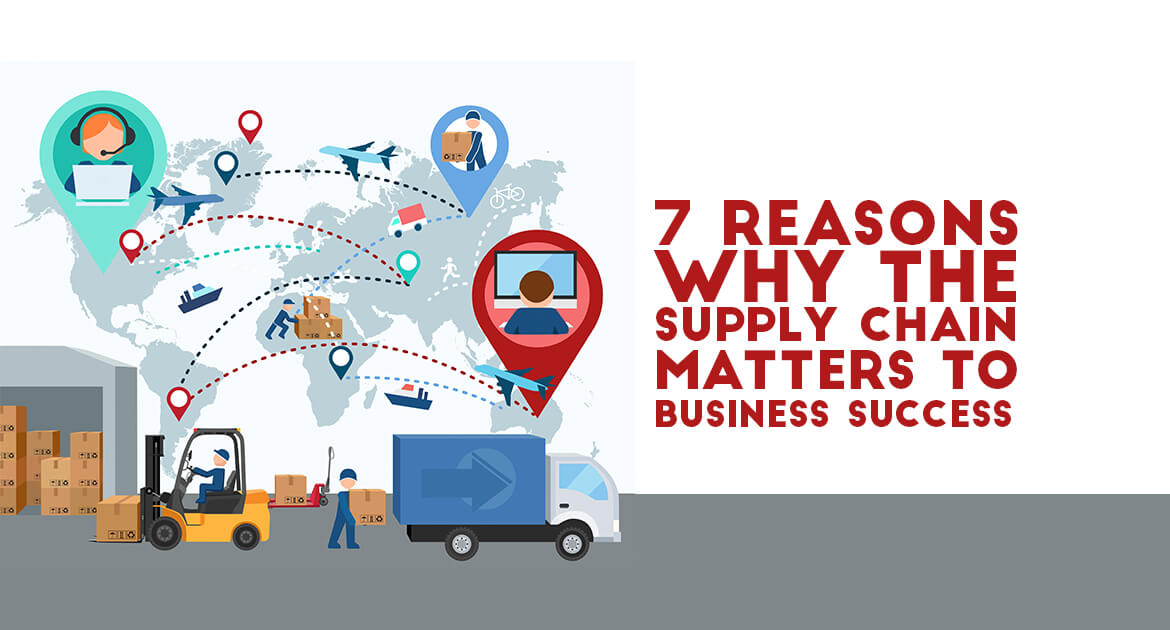
Standardized work
Before you can apply lean manufacturing to manufacturing, you need to first create standard work. This system of work is about the workers and the steps that they must complete to make a product. This also refers the process of continually improving the system via kaizen. The cell leader is responsible for standardizing work documents and they are automatically updated as takt times change. Standardized work documents provide a basis for improvement activities including kaizen or improvement activities.
Standardized work processes help improve service quality and productivity. They help to reduce product development and human error. The organization can also fix problems faster because employees are better equipped to understand the process. This enables the organization to implement continuous improvement and increase its customer satisfaction. It is easy to implement these processes within a company when they are standardized. Ultimately, it is a good idea to have a mission statement.
Continuous improvement
Lean principles promote continual improvement, resulting in a range of benefits. These benefits are usually additive, but one thread links them all: increased productivity, lower costs, and shorter lead times. Continuous improvement in lean is all about increasing value creation. But how is continuous improvement possible? This article will provide an overview of the common benefits of continuous improvements. It's easy: it saves companies money.
Continuous improvement is a process that focuses on incremental rather than large-scale improvements. Although small improvements seem insignificant at first glance, the whole is important. The slow process of improvement is not about making big leaps. Continuous improvement in lean manufacturing environments focuses on aligning goals. This helps the business achieve maximum productivity and profitability. Continuous improvement can streamline the production process and allow all processes to work together towards a common goal.
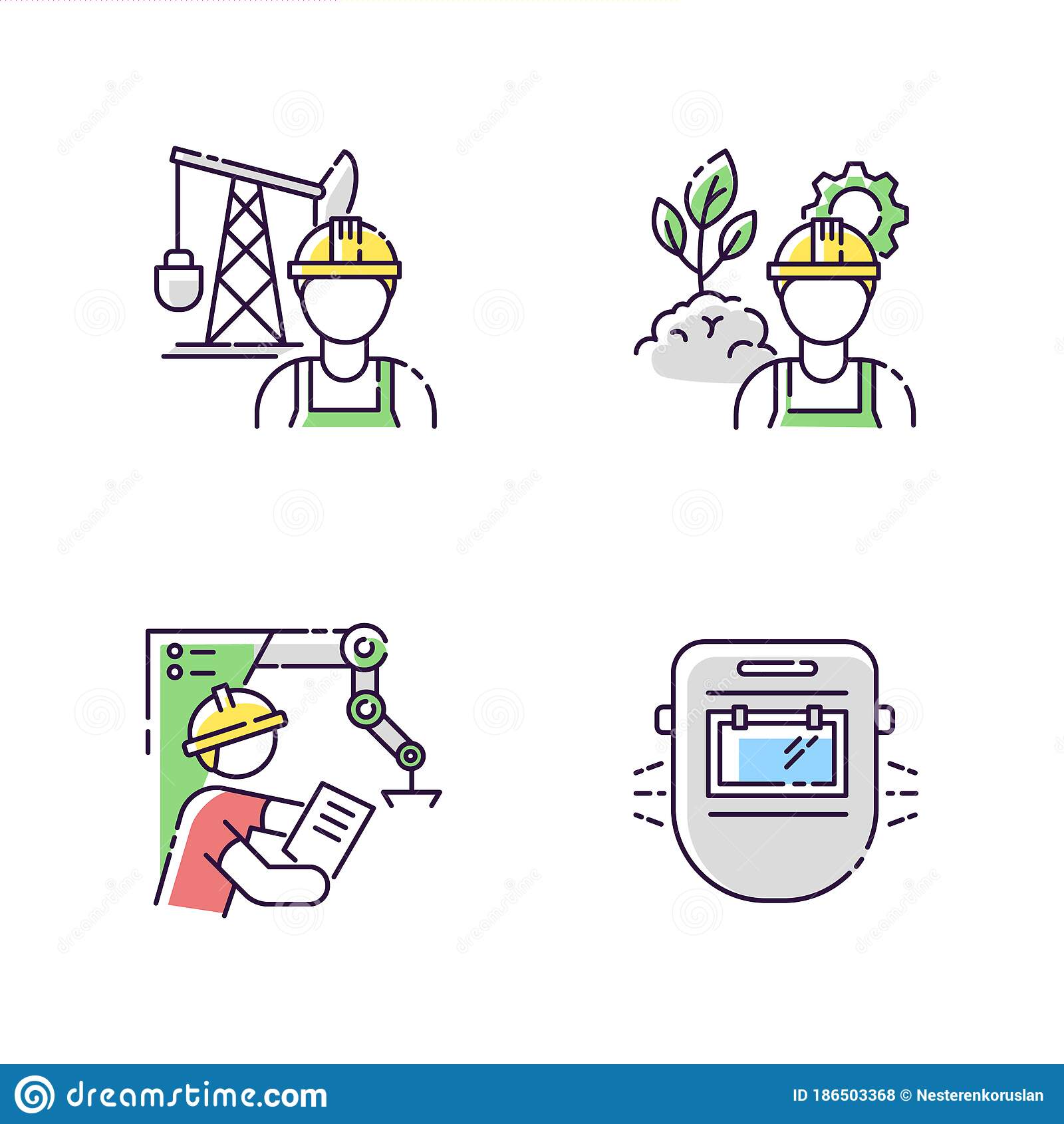
Kaizen
Kaizen in lean manufacturing focuses on waste elimination. It is sometimes used to improve production yield or reduce lead times. Employees are given specific roles that allow them to investigate the problem and find possible solutions. A kaizen event typically begins with the creation of a value stream map of the process. The team then conducts an analysis of time and other relevant operations. This continues until each step can be improved and the overall process has become more efficient.
One example: A manufacturing plant may choose to buy a new forklift after identifying inefficiencies. The operator might move inventory around to speed up loading and unloading. The value stream, which is a map that shows the processes involved in creating products and services, can be used similarly. Five S's will be used during the mapping to increase employee productivity as well as workplace practices. There are seven types. Each of these types focuses on a different aspect of a manufacturing process.
FAQ
What's the difference between Production Planning & Scheduling?
Production Planning (PP) refers to the process of determining how much production is needed at any given moment. This is accomplished by forecasting the demand and identifying production resources.
Scheduling involves the assignment of dates and times to tasks in order to complete them within the timeframe.
Why is logistics so important in manufacturing?
Logistics are an integral part any business. They can help you achieve great success by helping you manage product flow from raw material to finished goods.
Logistics play a key role in reducing expenses and increasing efficiency.
What does it take to run a logistics business?
A successful logistics business requires a lot more than just knowledge. To communicate effectively with clients and suppliers, you must be able to communicate well. You should be able analyse data and draw inferences. You must be able manage stress and pressure under pressure. You must be creative and innovative to develop new ideas to improve efficiency. You must be a strong leader to motivate others and direct them to achieve organizational goals.
It is important to be organized and efficient in order to meet tight deadlines.
Statistics
- In the United States, for example, manufacturing makes up 15% of the economic output. (twi-global.com)
- Job #1 is delivering the ordered product according to specifications: color, size, brand, and quantity. (netsuite.com)
- According to a Statista study, U.S. businesses spent $1.63 trillion on logistics in 2019, moving goods from origin to end user through various supply chain network segments. (netsuite.com)
- (2:04) MTO is a production technique wherein products are customized according to customer specifications, and production only starts after an order is received. (oracle.com)
- [54][55] These are the top 50 countries by the total value of manufacturing output in US dollars for its noted year according to World Bank.[56] (en.wikipedia.org)
External Links
How To
How to Use 5S for Increasing Productivity in Manufacturing
5S stands for "Sort", "Set In Order", "Standardize", "Separate" and "Store". Toyota Motor Corporation was the first to develop the 5S approach in 1954. It improves the work environment and helps companies to achieve greater efficiency.
This method has the basic goal of standardizing production processes to make them repeatable. This means that every day tasks such cleaning, sorting/storing, packing, and labeling can be performed. Because workers know what they can expect, this helps them perform their jobs more efficiently.
There are five steps to implementing 5S, including Sort, Set In Order, Standardize, Separate and Store. Each step involves a different action which leads to increased efficiency. If you sort items, it makes them easier to find later. When you arrange items, you place them together. You then organize your inventory in groups. Finally, when you label your containers, you ensure everything is labeled correctly.
Employees must be able to critically examine their work practices. Employees should understand why they do the tasks they do, and then decide if there are better ways to accomplish them. They will need to develop new skills and techniques in order for the 5S system to be implemented.
The 5S Method not only improves efficiency, but it also helps employees to be more productive and happier. They are more motivated to achieve higher efficiency levels as they start to see improvement.