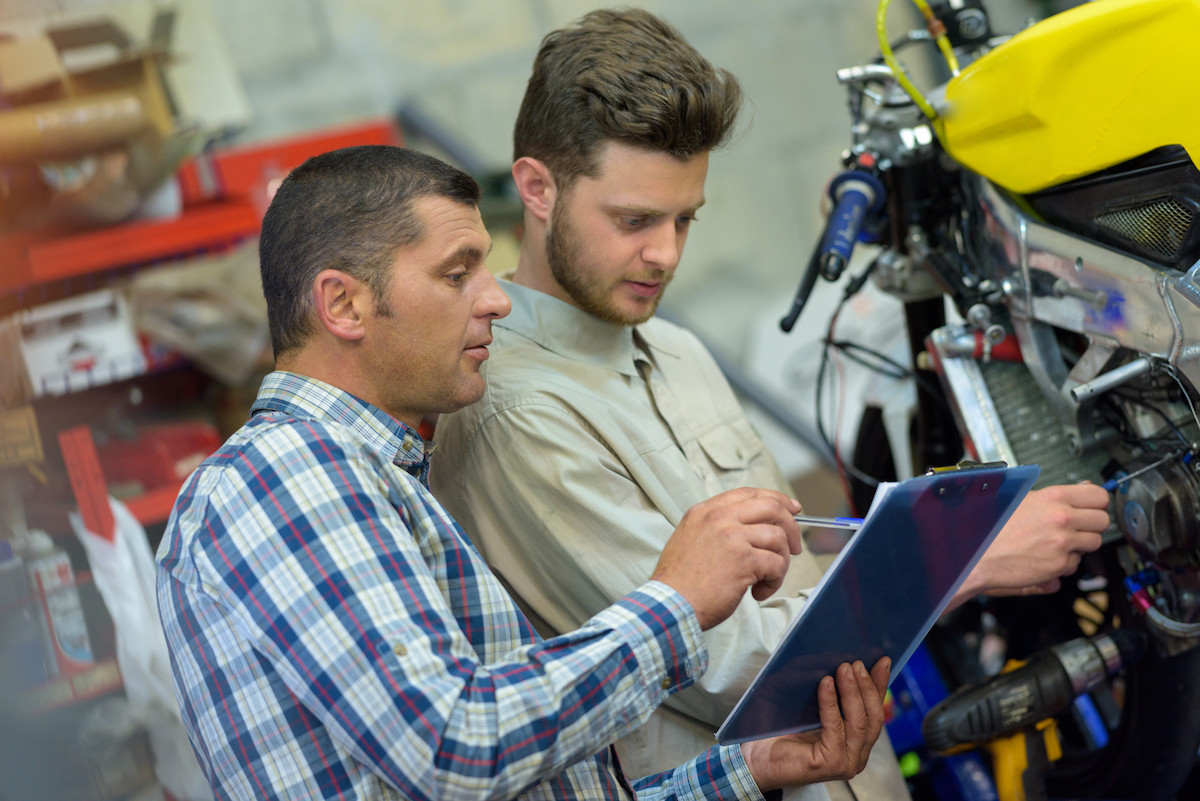
Mechatronics is a multidisciplinary engineering field that combines mechanical engineering with electrical engineering. This combination is key to the development of advanced machines that are efficient. A typical mechatronic system consists of sensors, actuators, and electronics. It collects signals from the environment, processes them, and generates an output signal. It can be found in many types of products. Mechatronic systems are installed in household items like computers and televisions to make them function. Mechatronic systems that are simpler and smarter will be the future of electromechanical technology.
The first electromechanical devices were used in early telegraphy. The first electromechanical device to transmit electrical signals was the Strowger Switch. These devices were widely used in automated telephone exchanges in the United States in the middle 20th century. Today, more equipment is designed with automated features and the use of solid-state electronics has replaced electromechanical devices in many applications.
An electro-mechanical technician combines mechanical technology with electrical or electronic circuits in order operate and maintain automated equipment. They may be involved with energy projects, or they could maintain equipment that is used in deep-ocean research. They might also repair machines. The Electro-Mechanical Technie must be able to troubleshoot and solve problems as well as have logical thinking skills. They must be able to work in pressure situations. They must be able and competent to safely use tools. Employers can gain a lot from their knowledge about electrical and mechanical system.
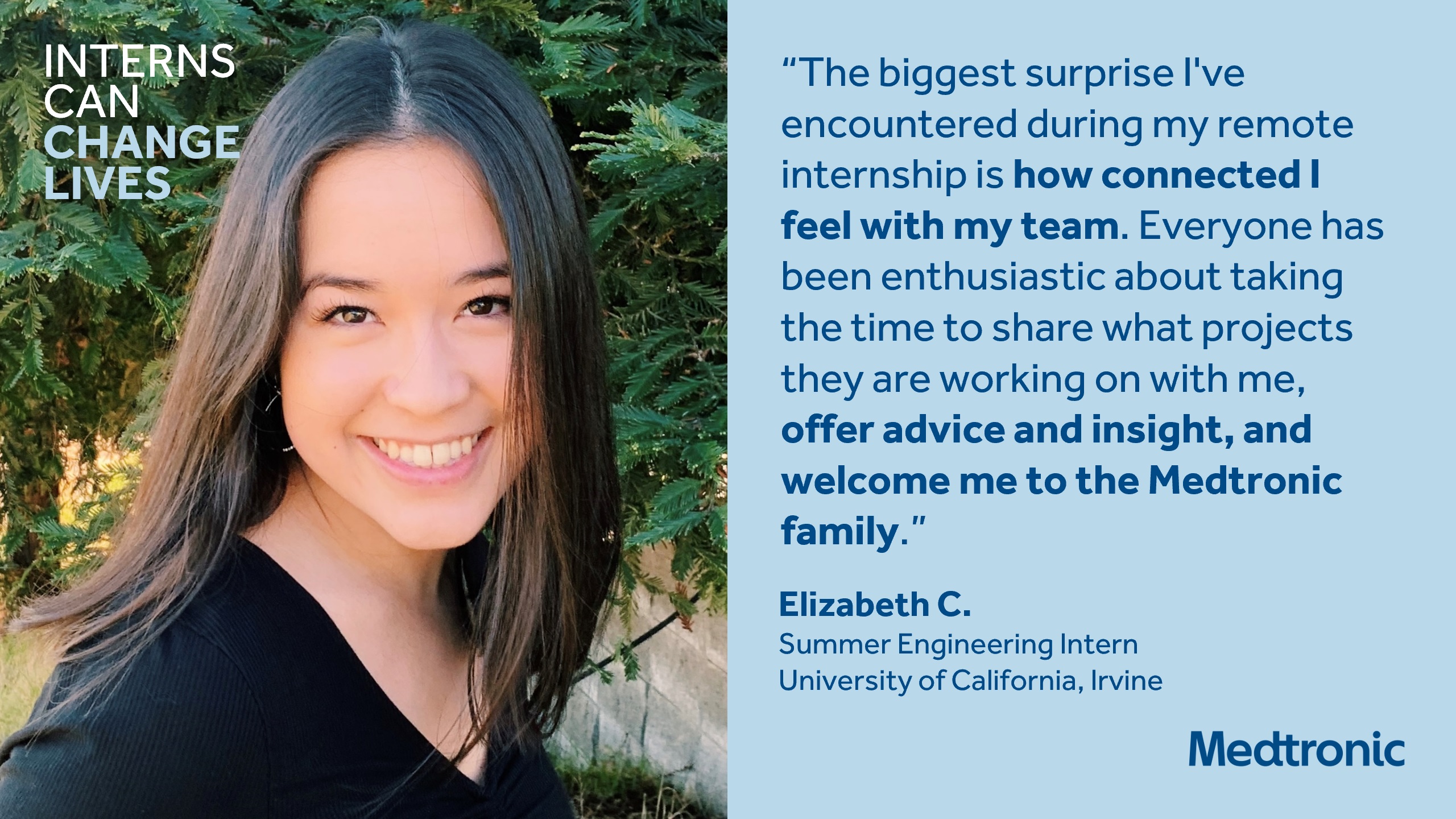
Electro-mechanical Technicians may earn a diploma or certificate from a vocational or technical school. They could also get an associate's/bachelor's in Electrical Engineering or Mechatronics. Certified Control Systems Certification is another certification that Electro-mechanical Technicians can use to prove their professional competence.
Sometimes, Electro-Mechanical Technicians are also known as assemblers. They follow assembly drawings and oral instructions to assemble mechanical and electronic equipment. They may also work with production drawings. These types of assemblers are also more likely to require transistors.
Mechatronics is expected to increase in popularity in the coming years. The society's need for high-functioning products and more efficient machines is the reason it has grown in popularity. The field of Mechatronics is still vastly underexplored. These include the development new technology like particle electromechanics or the relationships between magnetic and fluid energy. Mechatronics combines engineering with computer science to help solve problems in new ways. In addition, many large manufacturing companies are looking to develop new electronic-mechanical engineering technologies.
Mechatronics has a lot of potential and is always evolving. An Electro-mechanical Technician can specialize in the field of Mechatronics, which requires specialized knowledge in electrical circuits, sensing engineering, and computer software. These technicians will apply their specialized knowledge and design value-add products.
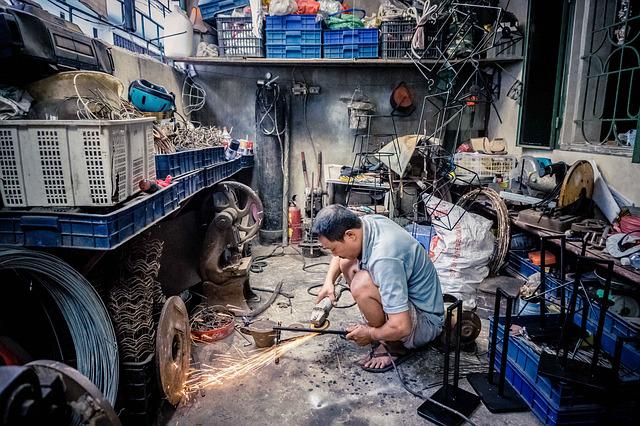
You can choose to specialize in electro-mechanical technicians, such as industrial maintenance, mechanics or maintenance and repair. This type of technician is expected to remain in demand because of the growth of computer-control systems. Compensation is dependent on experience, geographic location and industry.
FAQ
What jobs are available in logistics?
There are many types of jobs in logistics. Here are some examples:
-
Warehouse workers - They load trucks and pallets.
-
Transport drivers - These are people who drive trucks and trailers to transport goods or perform pick-ups.
-
Freight handlers - They sort and pack freight in warehouses.
-
Inventory managers – These people oversee inventory at warehouses.
-
Sales reps - They sell products and services to customers.
-
Logistics coordinators - They plan and organize logistics operations.
-
Purchasing agents - They purchase goods and services needed for company operations.
-
Customer service representatives are available to answer customer calls and emails.
-
Shipping clerks – They process shipping orders, and issue bills.
-
Order fillers - These people fill orders based on what has been ordered.
-
Quality control inspectors – They inspect incoming and outgoing products to ensure that there are no defects.
-
Others - There is a variety of other jobs in logistics. These include transportation supervisors and cargo specialists.
What does "warehouse" mean?
Warehouses and storage facilities are where goods are kept before being sold. You can have it indoors or outdoors. It may also be an indoor space or an outdoor area.
Can certain manufacturing steps be automated?
Yes! Automation has been around since ancient times. The Egyptians created the wheel thousands years ago. Nowadays, we use robots for assembly lines.
In fact, there are several applications of robotics in manufacturing today. They include:
-
Assembly line robots
-
Robot welding
-
Robot painting
-
Robotics inspection
-
Robots that create products
Manufacturing could also benefit from automation in other ways. 3D printing is a way to make custom products quickly and without waiting weeks or months for them to be manufactured.
What makes a production planner different from a project manger?
The major difference between a Production Planner and a Project Manager is that a Project Manager is often the person responsible for organizing and planning the entire project. While a Production Planner is involved mainly in the planning stage,
How can we reduce manufacturing overproduction?
Improved inventory management is the key to reducing overproduction. This would reduce the time spent on unproductive activities like purchasing, storing and maintaining excess stock. We could use these resources to do other productive tasks.
Kanban systems are one way to achieve this. A Kanban board, a visual display to show the progress of work, is called a Kanban board. Kanban systems are where work items travel through a series of states until reaching their final destination. Each state represents an individual priority level.
When work is completed, it can be transferred to the next stage. But if a task remains in the beginning stages it will stay that way until it reaches its end.
This allows for work to continue moving forward, while also ensuring that there is no work left behind. A Kanban board allows managers to monitor how much work is being completed at any given moment. This data allows them adjust their workflow based upon real-time data.
Lean manufacturing is another option to control inventory levels. Lean manufacturing works to eliminate waste throughout every stage of the production chain. Anything that does not contribute to the product's value is considered waste. The following are examples of common waste types:
-
Overproduction
-
Inventory
-
Packaging not required
-
Materials in excess
These ideas can help manufacturers improve efficiency and reduce costs.
Statistics
- In 2021, an estimated 12.1 million Americans work in the manufacturing sector.6 (investopedia.com)
- [54][55] These are the top 50 countries by the total value of manufacturing output in US dollars for its noted year according to World Bank.[56] (en.wikipedia.org)
- Job #1 is delivering the ordered product according to specifications: color, size, brand, and quantity. (netsuite.com)
- It's estimated that 10.8% of the U.S. GDP in 2020 was contributed to manufacturing. (investopedia.com)
- Many factories witnessed a 30% increase in output due to the shift to electric motors. (en.wikipedia.org)
External Links
How To
How to use lean manufacturing in the production of goods
Lean manufacturing refers to a method of managing that seeks to improve efficiency and decrease waste. It was created in Japan by Taiichi Ohno during the 1970s and 80s. He received the Toyota Production System award (TPS), from Kanji Toyoda, founder of TPS. Michael L. Watkins published the first book on lean manufacturing in 1990.
Lean manufacturing refers to a set of principles that improve the quality, speed and costs of products and services. It emphasizes the elimination and minimization of waste in the value stream. Just-in-time (JIT), zero defect (TPM), and 5S are all examples of lean manufacturing. Lean manufacturing emphasizes reducing non-value-added activities like inspection, rework and waiting.
Lean manufacturing not only improves product quality but also reduces costs. Companies can also achieve their goals faster by reducing employee turnover. Lean manufacturing has been deemed one of the best ways to manage the entire value-chain, including customers, distributors as well retailers and employees. Lean manufacturing is widely used in many industries. Toyota's philosophy is the foundation of its success in automotives, electronics and appliances, healthcare, chemical engineers, aerospace, paper and food, among other industries.
Five basic principles of Lean Manufacturing are included in lean manufacturing
-
Define Value- Identify the added value your company brings to society. What makes you stand out from your competitors?
-
Reduce Waste - Eliminate any activity that doesn't add value along the supply chain.
-
Create Flow: Ensure that the work process flows without interruptions.
-
Standardize & simplify - Make processes consistent and repeatable.
-
Building Relationships – Establish personal relationships with both external and internal stakeholders.
Lean manufacturing is not a new concept, but it has been gaining popularity over the last few years due to a renewed interest in the economy following the global financial crisis of 2008. Many businesses have adopted lean production techniques to make them more competitive. In fact, some economists believe that lean manufacturing will be an important factor in economic recovery.
Lean manufacturing is becoming a popular practice in automotive. It has many advantages. These include higher customer satisfaction, lower inventory levels, lower operating expenses, greater productivity, and improved overall safety.
The principles of lean manufacturing can be applied in almost any area of an organization. However, it is particularly useful when applied to the production side of an organization because it ensures that all steps in the value chain are efficient and effective.
There are three main types:
-
Just-in-Time Manufacturing: Also known as "pull systems", this type of lean manufacturing uses just-in-time manufacturing (JIT). JIT is a method in which components are assembled right at the moment of use, rather than being manufactured ahead of time. This strategy aims to decrease lead times, increase availability of parts and reduce inventory.
-
Zero Defects Manufacturing - ZDM: ZDM focuses its efforts on making sure that no defective units leave a manufacturing facility. It is better to repair a part than have it removed from the production line if it needs to be fixed. This is also true for finished products that require minor repairs before shipping.
-
Continuous Improvement (CI: Continuous improvement aims to increase the efficiency of operations by constantly identifying and making improvements to reduce or eliminate waste. Continuous Improvement (CI) involves continuous improvement in processes, people, tools, and infrastructure.