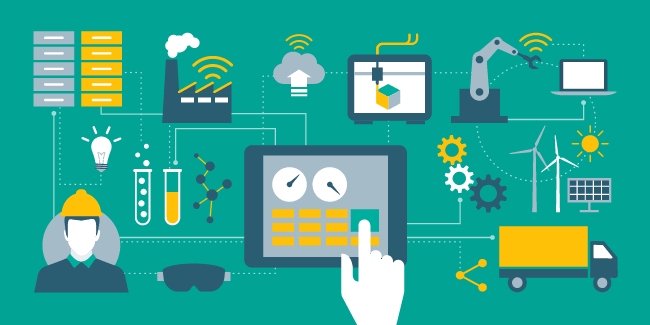
Tennessee has a diverse economy with a variety of career options. Tennessee has a wide range of career opportunities, whether you want to work in manufacturing or another industry.
Manufacturing Jobs In Tennessee
MNI has collected data showing that over 6109 companies in the state employ 408 131 workers. These companies produce many different products including automotive parts and industrial machinery.
Transportation Equipment Manufacturing: The largest industrial sector in the state, transportation equipment manufactures trucks and other vehicles and is also a major producer of commercial and military aircraft parts. These firms have hired many new workers in recent years, as Nissan expands production at its plant in Smyrna and Volkswagen ramps up production at its Chattanooga facility.
Industrial Machinery: Industrial machines are second only to transportation in terms of size. They produce parts for various industries, such as agriculture and defense. Manufacturers that employ this sector include DENSO Manufacturing Tennessee in Maryville and Maremont Exhaust Products in Loudon.
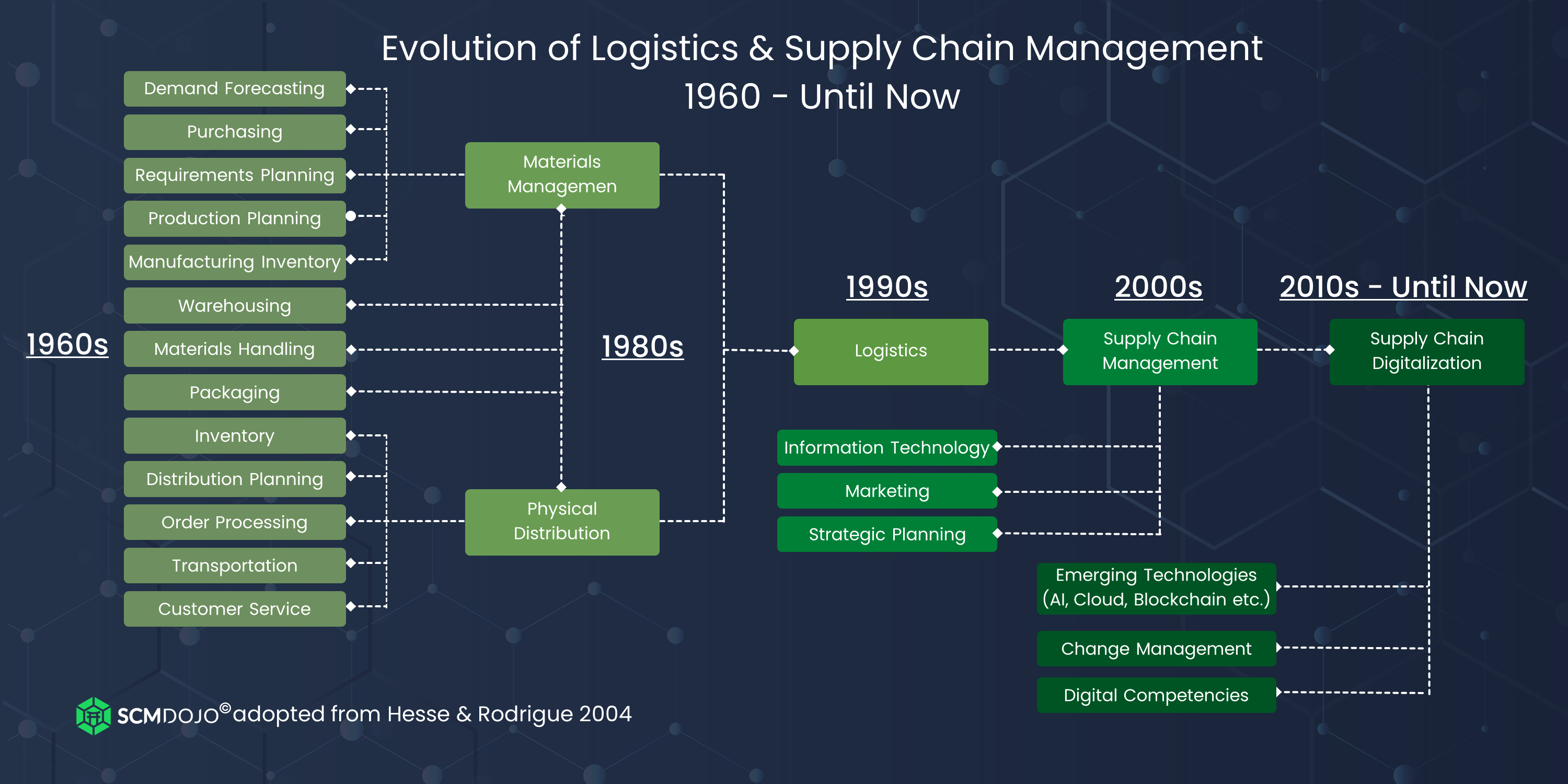
Food Processing is the third largest industry. It includes food producers such as Little Debbie snacks and Drake's Devil Dogs. These companies hire many different people including production workers as well as packaging specialists and warehouse assistants.
Advanced Manufacturing: As the fourth-largest industry in New York, advanced manufacturing has created more than 32,000 new jobs in recent years. Eastman Chemicals, Consolidated Nuclear Security, and McKee foods are the top employers in this industry.
You can find factory jobs in Tennessee.
The best way to start a manufacturing career in the state is through an apprenticeship or training program. These programs are designed for you to get practical experience in one area of the manufacturing process. These courses focus on a certain skill, like welding or electrical work. They can be customized according to your qualifications and interests.
Some programs cover a broader area such as manufacturing or quality management. These programs can be taught in community colleges and other training providers.
Those interested in a career in the manufacturing industry can also search for manufacturing jobs on online job boards or classified ads. These sites offer a wealth of information about a range of companies and allow you to submit applications without having to speak to hiring managers.
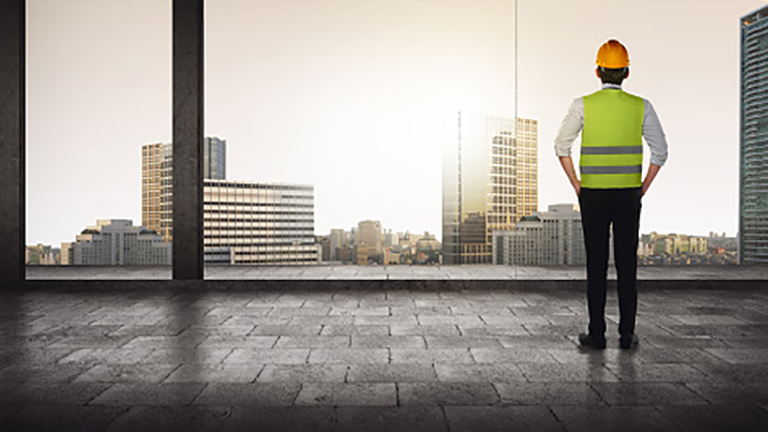
To find a position in the manufacturing industry, you should start by checking out the careers page on a website for a local or a national employer. You can find a description of the company as well as a list with open positions on this site.
You can also find jobs in manufacturing by attending job fairs. These often give you the opportunity to interview for several different companies. These events are difficult to locate and may not include all of the manufacturing jobs available in your locality.
FAQ
How can excess manufacturing production be reduced?
In order to reduce excess production, you need to develop better inventory management methods. This would reduce the time spent on unproductive activities like purchasing, storing and maintaining excess stock. We could use these resources to do other productive tasks.
One way to do this is to adopt a Kanban system. A Kanban Board is a visual display that tracks work progress. Work items are moved through various states to reach their destination in a Kanban system. Each state represents an individual priority level.
When work is completed, it can be transferred to the next stage. If a task is still in its beginning stages, it will continue to be so until it reaches the end.
This allows for work to continue moving forward, while also ensuring that there is no work left behind. Managers can see how much work has been done and the status of each task at any time with a Kanban Board. This information allows them to adjust their workflow based on real-time data.
Lean manufacturing can also be used to reduce inventory levels. Lean manufacturing emphasizes eliminating waste in all phases of production. Anything that does nothing to add value to a product is waste. There are several types of waste that you might encounter:
-
Overproduction
-
Inventory
-
Unnecessary packaging
-
Exceed materials
By implementing these ideas, manufacturers can improve efficiency and cut costs.
How is a production manager different from a producer planner?
The major difference between a Production Planner and a Project Manager is that a Project Manager is often the person responsible for organizing and planning the entire project. While a Production Planner is involved mainly in the planning stage,
How can manufacturing avoid production bottlenecks
Avoiding production bottlenecks is as simple as keeping all processes running smoothly, from the time an order is received until the product ships.
This includes planning for capacity requirements as well as quality control measures.
Continuous improvement techniques such Six Sigma are the best method to accomplish this.
Six Sigma Management System is a method to increase quality and reduce waste throughout your organization.
It emphasizes consistency and eliminating variance in your work.
What is the distinction between Production Planning or Scheduling?
Production Planning (PP) is the process of determining what needs to be produced at any given point in time. This is accomplished by forecasting the demand and identifying production resources.
Scheduling involves the assignment of dates and times to tasks in order to complete them within the timeframe.
What are the main products of logistics?
Logistics refers to the movement of goods from one place to another.
They include all aspects associated with transport including packaging, loading transporting, unloading storage, warehousing inventory management customer service, distribution returns and recycling.
Logisticians ensure that the right product reaches the right place at the right time and under safe conditions. Logisticians assist companies in managing their supply chains by providing information such as demand forecasts, stock levels and production schedules.
They can also track shipments in transit and monitor quality standards.
Why automate your warehouse?
Modern warehouses have become more dependent on automation. E-commerce has increased the demand for quicker delivery times and more efficient processes.
Warehouses must be able to quickly adapt to changing demands. Technology investment is necessary to enable warehouses to respond quickly to changing demands. Automating warehouses is a great way to save money. These are some of the benefits that automation can bring to warehouses:
-
Increases throughput/productivity
-
Reduces errors
-
Increases accuracy
-
Boosts safety
-
Eliminates bottlenecks
-
Companies can scale more easily
-
Increases efficiency of workers
-
It gives visibility to everything that happens inside the warehouse
-
Enhances customer experience
-
Improves employee satisfaction
-
It reduces downtime, and increases uptime
-
Ensures quality products are delivered on time
-
Human error can be eliminated
-
It ensures compliance with regulations
Statistics
- (2:04) MTO is a production technique wherein products are customized according to customer specifications, and production only starts after an order is received. (oracle.com)
- [54][55] These are the top 50 countries by the total value of manufacturing output in US dollars for its noted year according to World Bank.[56] (en.wikipedia.org)
- It's estimated that 10.8% of the U.S. GDP in 2020 was contributed to manufacturing. (investopedia.com)
- In the United States, for example, manufacturing makes up 15% of the economic output. (twi-global.com)
- Job #1 is delivering the ordered product according to specifications: color, size, brand, and quantity. (netsuite.com)
External Links
How To
How to Use 5S for Increasing Productivity in Manufacturing
5S stands for "Sort", 'Set In Order", 'Standardize', & Separate>. Toyota Motor Corporation developed the 5S method in 1954. It improves the work environment and helps companies to achieve greater efficiency.
The basic idea behind this method is to standardize production processes, so they become repeatable, measurable, and predictable. This means that tasks such as cleaning, sorting, storing, packing, and labeling are performed daily. Workers can be more productive by knowing what to expect.
Five steps are required to implement 5S: Sort, Set In Order, Standardize. Separate. Each step requires a different action to increase efficiency. If you sort items, it makes them easier to find later. When items are ordered, they are put together. You then organize your inventory in groups. Finally, label all containers correctly.
Employees must be able to critically examine their work practices. Employees must be able to see why they do what they do and find a way to achieve them without having to rely on their old methods. To be successful in the 5S system, employees will need to acquire new skills and techniques.
In addition to increasing efficiency, the 5S method also improves morale and teamwork among employees. As they begin to see improvements, they feel motivated to continue working towards the goal of achieving higher levels of efficiency.