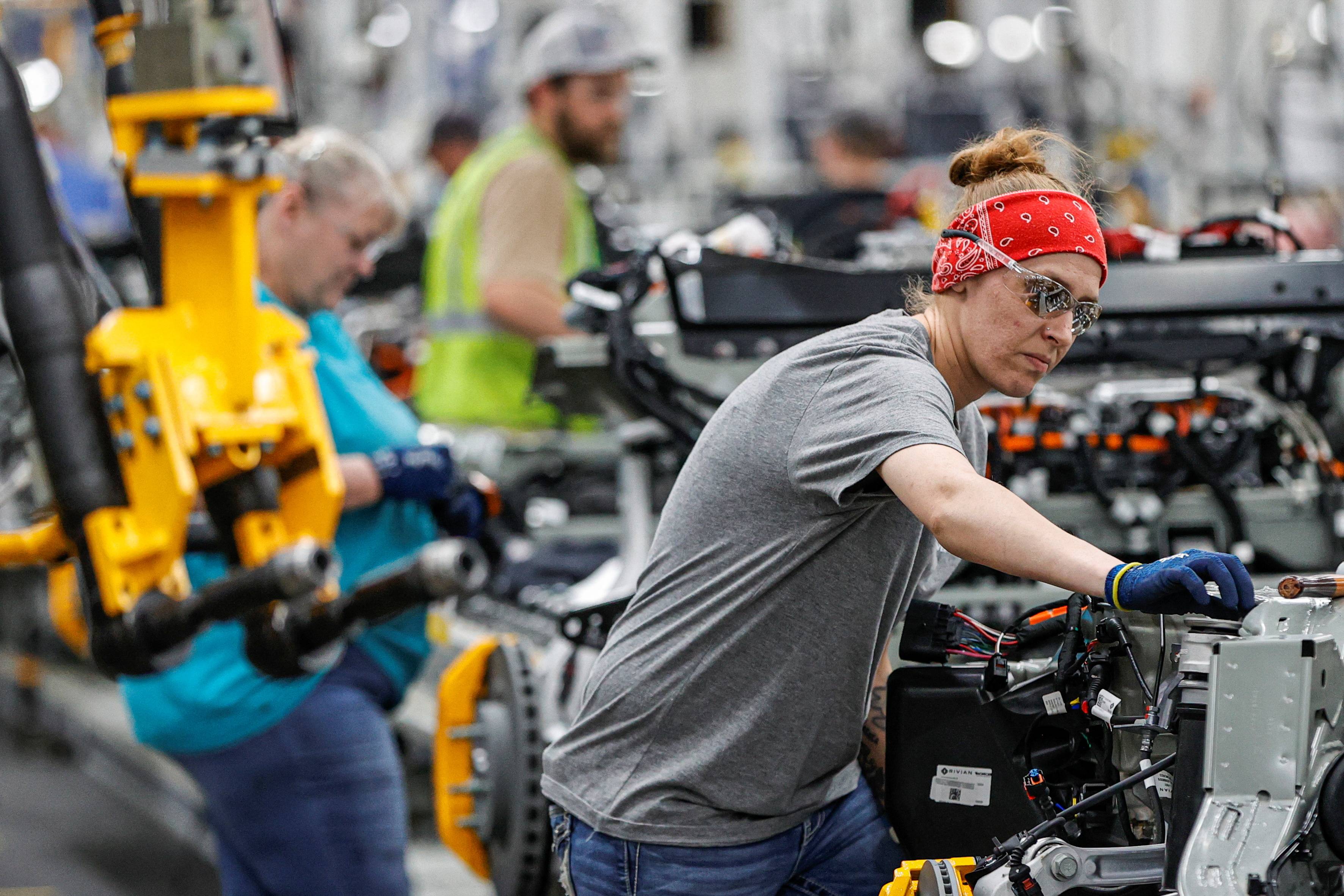
A supply manager should have experience leading manufacturing jobs. A supply chain manager should have a minimum of a bachelor's and at least 10+ years experience. They must also be able and willing to collaborate with other departments in the company. They should be motivated and able to take decisions that will affect the company's supply-chain. They must also be well-versed in safety procedures, as well as industry-related terms and terminology.
The entire logistics process is overseen by supply chain managers. They work closely with customers, suppliers, and other stakeholders to ensure the smooth running of the supply chain. They find solutions for any problem that may arise and help create an environment that is productive and functional. They are also responsible for coordinating the company's supply and distribution strategy.
Responsible for the coordination of phases such as raw material procurement and production, as well distribution, are supply chain managers. They must be capable of negotiating prices for equipment and materials, as well as being able to monitor and control the effectiveness of their supply-chain. They are responsible to coordinate and plan transport and storage methods.
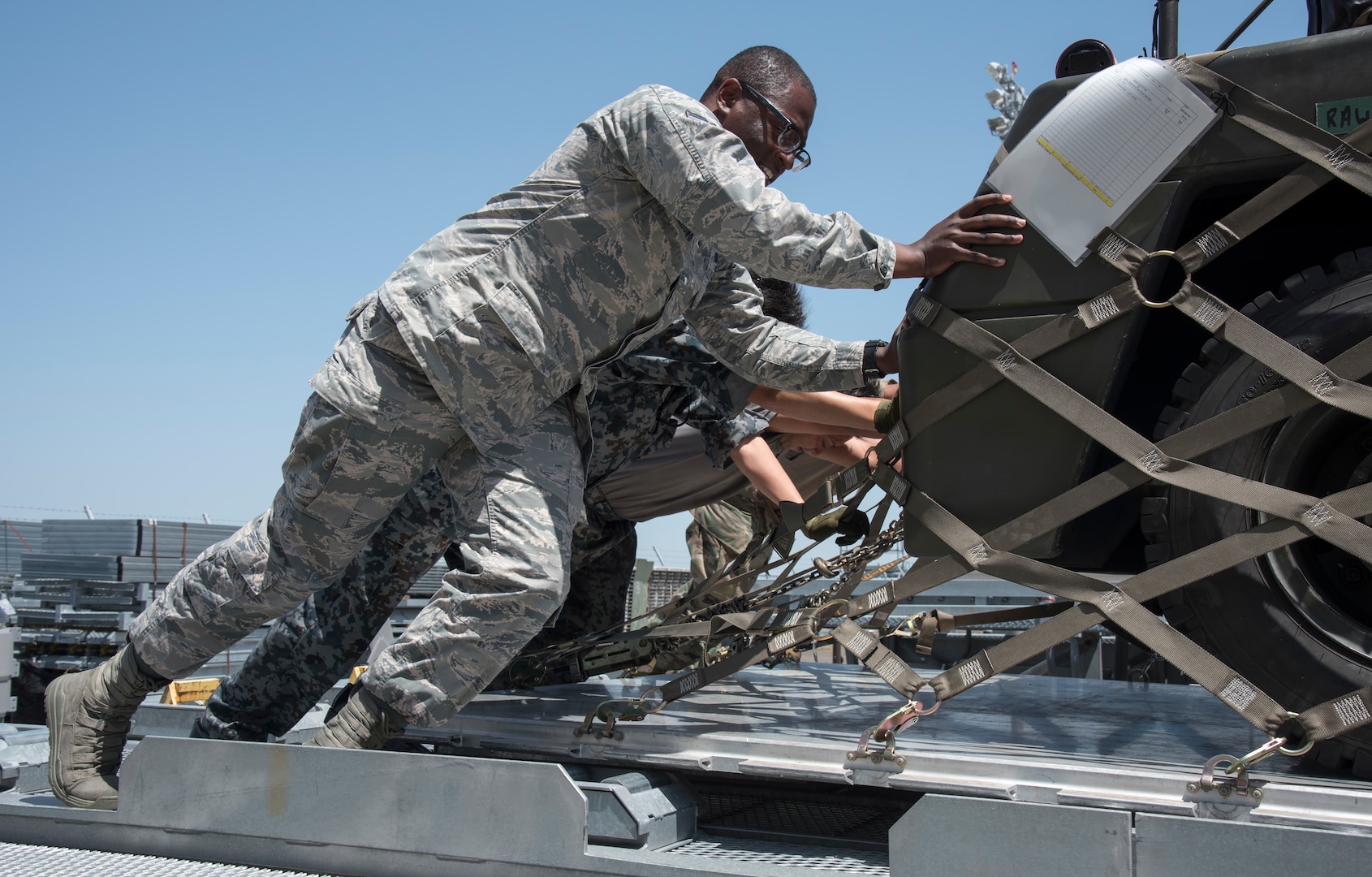
They are responsible for ensuring the quality of products. They are also responsible for optimizing the firm's human and financial capital. They are also responsible for identifying opportunities to recycle, reuse, and repurpose materials and products. They need to be able predict future needs throughout production.
You may find supply chain managers in many different industries such as fashion, retail, food, and automotive. They must be able to liaise with various departments within their company, and they must be able to provide training to all personnel. They must have a good understanding of management principles and strategies, supply chain management, and supply chain management. They will need to have a background and ability to manage large-scale operations.
The training required of supply chain managers is in inventory control and supplier management. They should be familiar with industry policies and procedures and have the ability manage budgets. They must be adept at organizing systems and be able lead groups. They must also have a thorough understanding of the company's operations and be able to lead their team. They must have a deep understanding of the company's goals and be able to communicate effectively with suppliers and customers.
Supply chain managers are also responsible for monitoring the environmental performance of their distribution partners. They may be required to look into the carbon footprints for their transport and storage providers. They will need to be aware of key performance indicators (KPIs) in the supply chain, and be able develop solutions to any issues. They will need to look for ways to cut costs, including shipping and delivery.
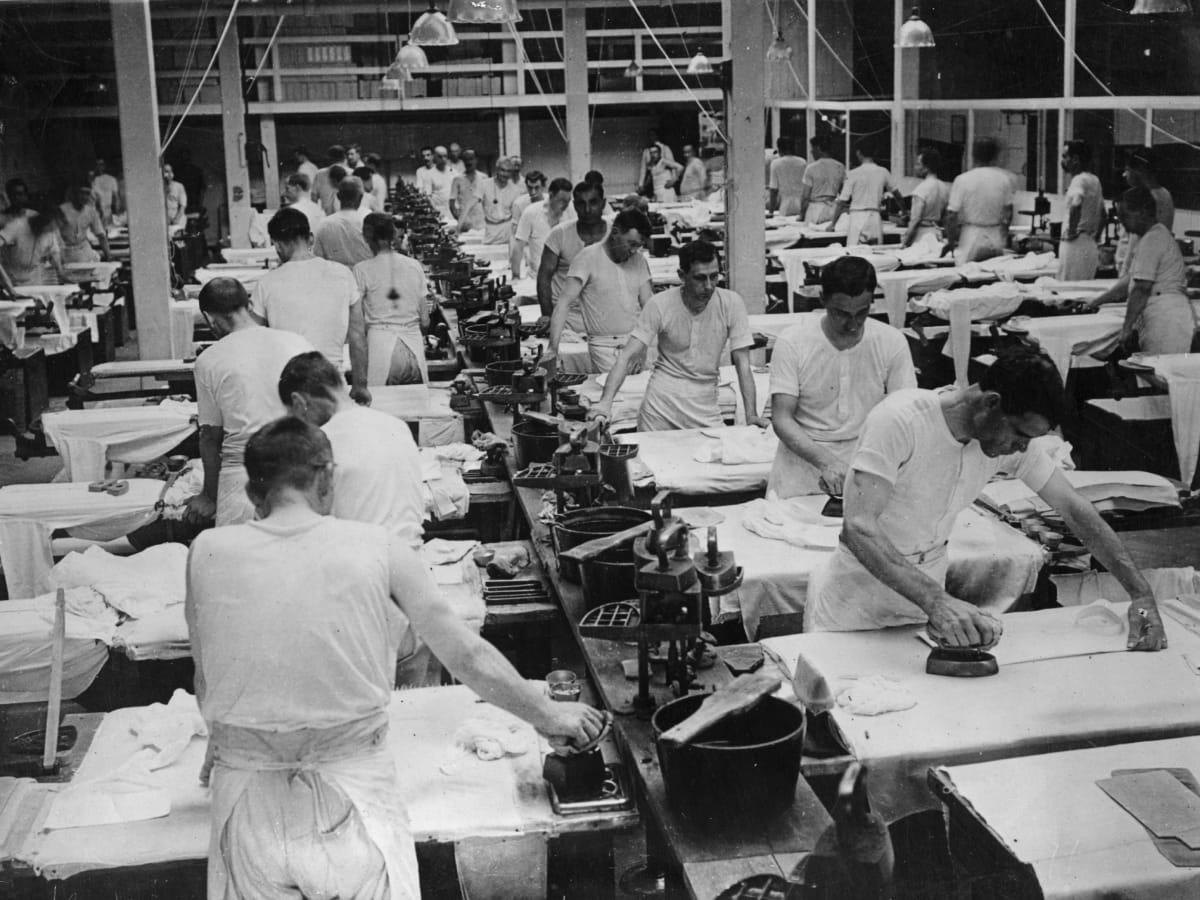
The supply chain managers are part of teams that coordinate the work. They also have to train new employees. They need to be skilled in transport, purchasing, manufacturing, and must also have an understanding of management principles and supply chain management.
FAQ
What does the term manufacturing industries mean?
Manufacturing Industries are companies that manufacture products. Consumers are people who purchase these goods. To accomplish this goal, these companies employ a range of processes including distribution, sales, management, and production. They produce goods from raw materials by using machines and other machinery. This includes all types if manufactured goods.
What is the responsibility of a manufacturing manager?
A manufacturing manager must make sure that all manufacturing processes run smoothly and effectively. They should be aware of any issues within the company and respond accordingly.
They should also be able communicate with other departments, such as sales or marketing.
They should be up to date on the latest trends and be able apply this knowledge to increase productivity and efficiency.
How can manufacturing overproduction be reduced?
It is essential to find better ways to manage inventory to reduce overproduction. This would reduce the time spent on unproductive activities like purchasing, storing and maintaining excess stock. We could use these resources to do other productive tasks.
One way to do this is to adopt a Kanban system. A Kanban board, a visual display to show the progress of work, is called a Kanban board. A Kanban system allows work items to move through several states before reaching their final destination. Each state represents a different priority.
As an example, if work is progressing from one stage of the process to another, then the current task is complete and can be transferred to the next. It is possible to keep a task in the beginning stages until it gets to the end.
This helps to keep work moving forward while ensuring that no work is left behind. With a Kanban board, managers can see exactly how much work is being done at any given moment. This allows them the ability to adjust their workflow using real-time data.
Lean manufacturing, another method to control inventory levels, is also an option. Lean manufacturing works to eliminate waste throughout every stage of the production chain. Any product that isn't adding value can be considered waste. Here are some examples of common types.
-
Overproduction
-
Inventory
-
Packaging that is not necessary
-
Exceed materials
By implementing these ideas, manufacturers can improve efficiency and cut costs.
What are the four types in manufacturing?
Manufacturing is the process that transforms raw materials into useful products. Manufacturing can include many activities such as designing and building, testing, packaging shipping, selling, servicing, and other related activities.
Statistics
- According to the United Nations Industrial Development Organization (UNIDO), China is the top manufacturer worldwide by 2019 output, producing 28.7% of the total global manufacturing output, followed by the United States, Japan, Germany, and India.[52][53] (en.wikipedia.org)
- (2:04) MTO is a production technique wherein products are customized according to customer specifications, and production only starts after an order is received. (oracle.com)
- You can multiply the result by 100 to get the total percent of monthly overhead. (investopedia.com)
- In the United States, for example, manufacturing makes up 15% of the economic output. (twi-global.com)
- It's estimated that 10.8% of the U.S. GDP in 2020 was contributed to manufacturing. (investopedia.com)
External Links
How To
Six Sigma in Manufacturing
Six Sigma is defined by "the application SPC (statistical process control) techniques to achieve continuous improvements." Motorola's Quality Improvement Department developed it at their Tokyo plant in Japan in 1986. Six Sigma is a method to improve quality through standardization and elimination of defects. Many companies have adopted Six Sigma in recent years because they believe that there are no perfect products and services. Six Sigma's primary goal is to reduce variation from the average value of production. If you take a sample and compare it with the average, you will be able to determine how much of the production process is different from the norm. If there is a significant deviation from the norm, you will know that something needs to change.
The first step toward implementing Six Sigma is understanding how variability works in your business. Once you've understood that, you'll want to identify sources of variation. This will allow you to decide if these variations are random and systematic. Random variations occur when people make mistakes; systematic ones are caused by factors outside the process itself. These are, for instance, random variations that occur when widgets are made and some fall off the production line. If however, you notice that each time you assemble a widget it falls apart in exactly the same spot, that is a problem.
Once you have identified the problem, you can design solutions. That solution might involve changing the way you do things or redesigning the process altogether. Once you have implemented the changes, it is important to test them again to ensure they work. If they fail, you can go back to the drawing board to come up with a different plan.