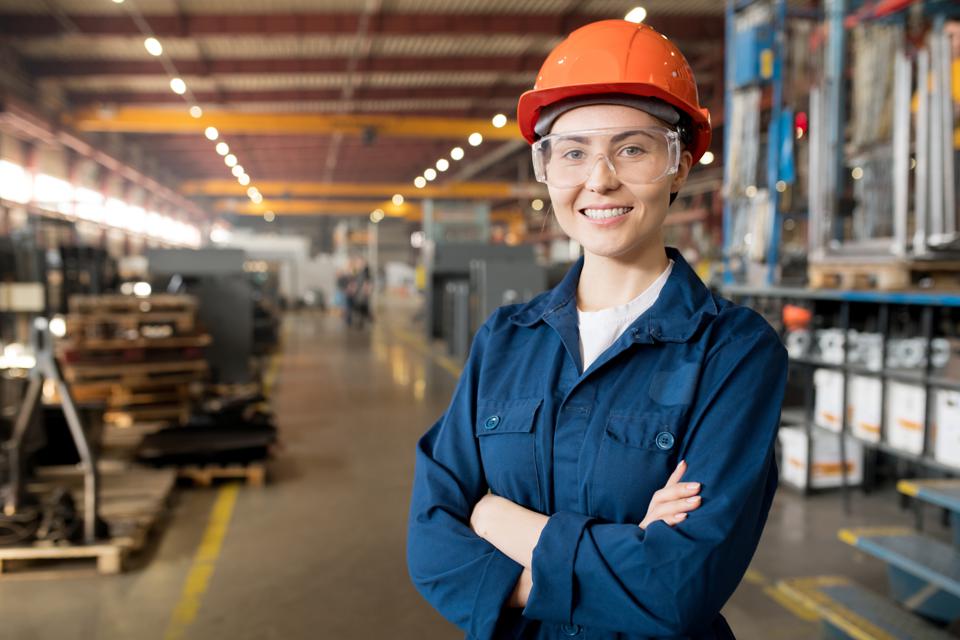
Industrial management is an engineering field where different engineering processes are integrated in order to create a management system. A industrial manager is responsible for integrating these engineering processes into one integrated management system. Here are some facts about this job. Below are some benefits and requirements that you must meet to be an industrial manager. If you have the required qualifications and are looking for a challenging and rewarding job, this is the career for you. Continue reading to learn about the career.
Job description
An industrial manager oversees all aspects of the production process. Although this job covers all aspects of the production process it will also cover how to source raw material and implement equipment. Computer literacy is essential for industrial production managers, who must be able to use computers to coordinate the work of different departments, suppliers, clients, and other parties. Additionally, industrial production managers need to be proficient in current production technologies and management methods. Managers are often involved in professional organizations and attend trade shows and industry conferences. They also take courses to become certified in their fields.
Industrial managers coordinate all activities within a company, in addition to supervising production processes. They ensure that production lines are productive and meet customer expectations in terms both quality and speed. They oversee staffing levels and alter production levels when necessary to reduce inventory. They may coordinate communication with suppliers or other departments, and supervise quality control programs. The majority of this job involves managing people.
Education Required
For industrial managers, a bachelor's level in business administration, management, engineering or other related fields is not enough. Some employers prefer candidates with a background or education in these areas. Industrial managers also need to be computer literate. Computers have become an integral part in manufacturing. They can help coordinate production between departments as well as suppliers and clients. To excel in this field, interested individuals need to have the right education and experience.
Many industrial production supervisors start out as production workers. They then progress to first-line supervisory jobs. A college degree in business administration is required to advance to an industrial management position. However, entry-level workers may still be able obtain this education through their jobs or by taking classes sponsored in part by their companies. However, managers must have two to five year of relevant experience before becoming a manager.
Potential earning
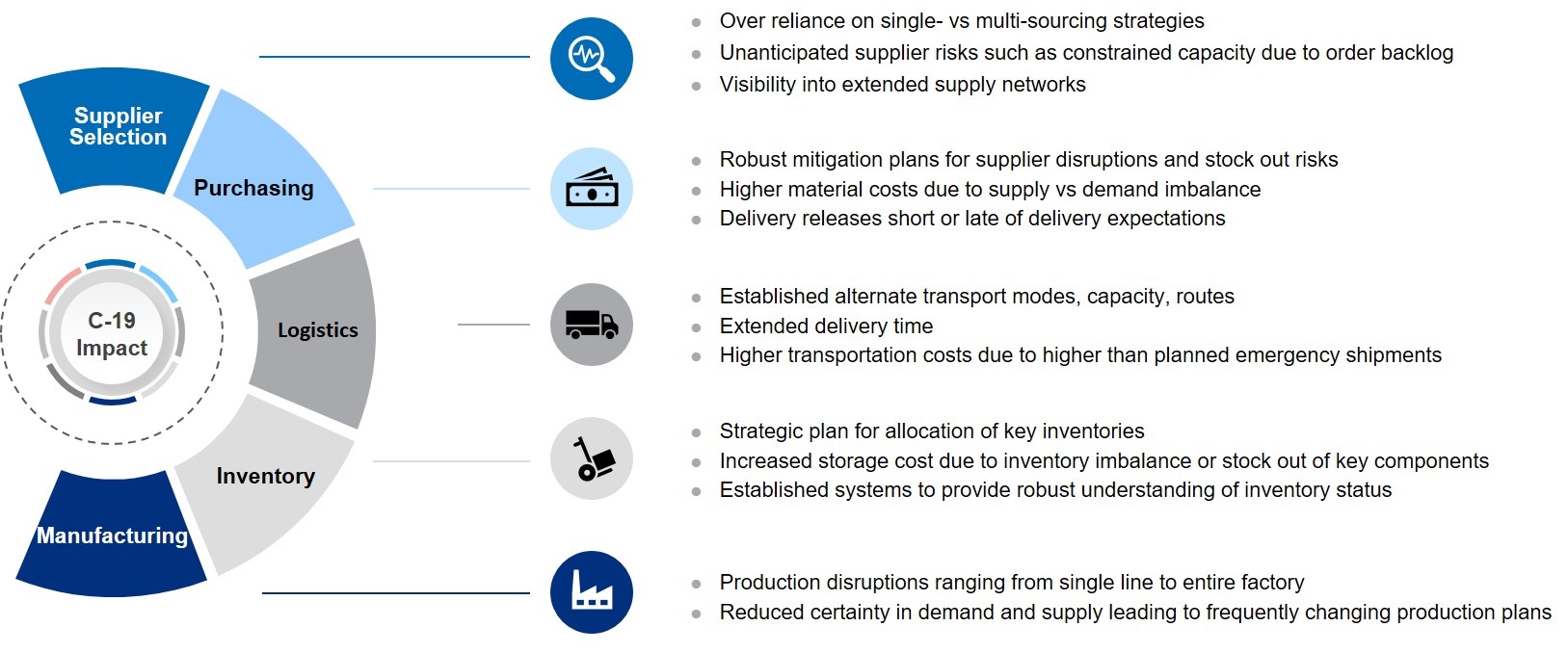
The industrial managers are responsible for overseeing the smooth running of manufacturing plants. They are responsible for determining how best to utilize equipment and employees, as well as making strategic decisions. These people are responsible for evaluating and hiring workers. They also set production schedules and ensure safety. They are responsible for overseeing the day-to-day operations of a team and constantly analyzing the production process to ensure it is running efficiently and at peak performance.
An industrial production manager's earnings potential is dependent on both the employer and their experience. Although it's impossible to predict the future earnings of industrial producers, the average salary was $103,380 in May 2016, with the highest-paid earning industrial production managers earning $172,000. High-skilled industrial production managers may earn more if they have been certified and received additional training. According to the U.S. Bureau of Labor Statistics industrial production managers who have earned a bachelor’s degree or higher could earn more.
Work environment
An industrial production manager divides his or her time between the production floor and an office, often in the same building. Industrial production managers must observe established health and safety practices and wear appropriate protective equipment when working in a production area. They often spend significant time in meetings and analysis of production data. They may also be responsible for writing reports. Industrial production managers often work in dynamic environments.
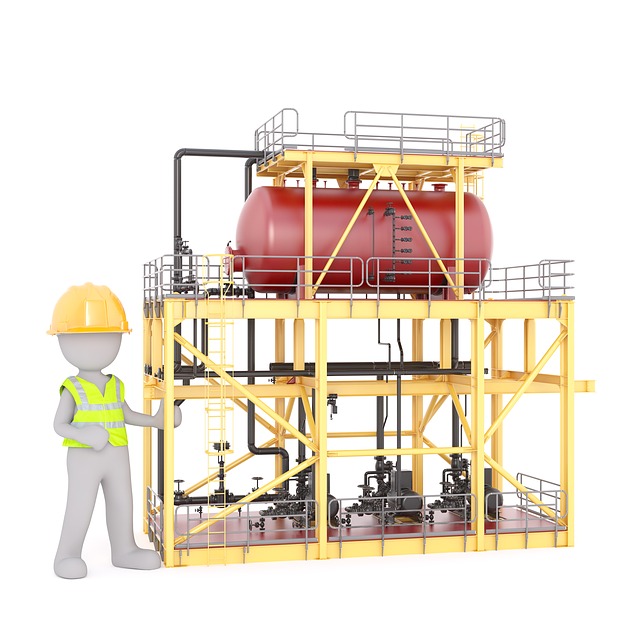
As part of a business's management structure, industrial production managers have many responsibilities. They have to coordinate the work of many workers and increase productivity. Increasing productivity and ensuring safety are some of the primary responsibilities of an industrial production manager. Because of corporate restructuring, many levels of management have been eliminated and support staff have been reduced, leaving more of the workload to production managers. This is a serious challenge for any manager and can make the job of a production manager difficult.
FAQ
What does manufacturing mean?
Manufacturing Industries are businesses that produce products for sale. Consumers are people who purchase these goods. This is accomplished by using a variety of processes, including production, distribution and retailing. They produce goods from raw materials by using machines and other machinery. This covers all types of manufactured goods including clothing, food, building supplies and furniture, as well as electronics, tools, machinery, vehicles and pharmaceuticals.
What are the goods of logistics?
Logistics refers to the movement of goods from one place to another.
They encompass all aspects transport, including packaging and loading, transporting, storage, unloading.
Logisticians ensure that products reach the right destination at the right moment and under safe conditions. They assist companies with their supply chain efficiency through information on demand forecasts. Stock levels, production times, and availability.
They also keep track of shipments in transit, monitor quality standards, perform inventories and order replenishment, coordinate with suppliers and vendors, and provide support services for sales and marketing.
How does a Production Planner differ from a Project Manager?
The main difference between a production planner and a project manager is that a project manager is usually the person who plans and organizes the entire project, whereas a production planner is mainly involved in the planning stage of the project.
Statistics
- (2:04) MTO is a production technique wherein products are customized according to customer specifications, and production only starts after an order is received. (oracle.com)
- In 2021, an estimated 12.1 million Americans work in the manufacturing sector.6 (investopedia.com)
- In the United States, for example, manufacturing makes up 15% of the economic output. (twi-global.com)
- Job #1 is delivering the ordered product according to specifications: color, size, brand, and quantity. (netsuite.com)
- [54][55] These are the top 50 countries by the total value of manufacturing output in US dollars for its noted year according to World Bank.[56] (en.wikipedia.org)
External Links
How To
Six Sigma: How to Use it in Manufacturing
Six Sigma refers to "the application and control of statistical processes (SPC) techniques in order to achieve continuous improvement." Motorola's Quality Improvement Department, Tokyo, Japan, developed it in 1986. Six Sigma is a method to improve quality through standardization and elimination of defects. Many companies have adopted Six Sigma in recent years because they believe that there are no perfect products and services. Six Sigma's primary goal is to reduce variation from the average value of production. This means that if you take a sample of your product, then measure its performance against the average, you can find out what percentage of the time the process deviates from the norm. If this deviation is too big, you know something needs fixing.
Understanding how your business' variability is a key step towards Six Sigma implementation is the first. Once you have a good understanding of the basics, you can identify potential sources of variation. This will allow you to decide if these variations are random and systematic. Random variations happen when people make errors; systematic variations are caused externally. For example, if you're making widgets, and some of them fall off the assembly line, those would be considered random variations. However, if you notice that every time you assemble a widget, it always falls apart at exactly the same place, then that would be a systematic problem.
Once you've identified where the problems lie, you'll want to design solutions to eliminate those problems. It might mean changing the way you do business or redesigning it entirely. Test them again once you've implemented the changes. If they fail, you can go back to the drawing board to come up with a different plan.