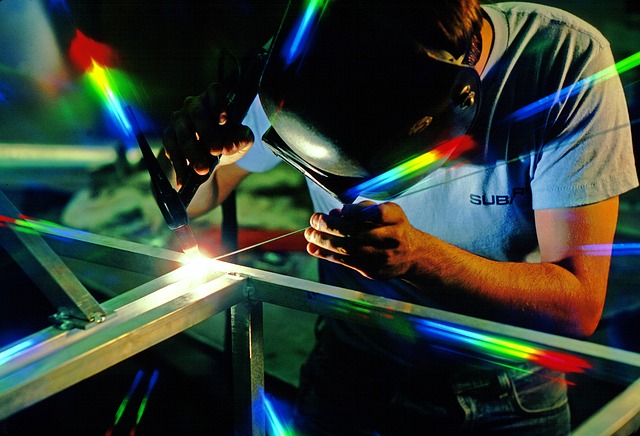
The success of your business depends on how well you manage your supply chain. The goal is to improve the efficiency of your processes, reduce costs, and improve customer satisfaction. Management of your supply chain will not only increase revenues but also create a competitive advantage on the market. Eight out of ten companies with a strong supply-chain management program see revenue growth that is higher than the industry average.
You need to track your inventory and monitor it's status in order to manage your supply chain. You also need to know the availability of your products, the prices of your products, and the lead time of your products.
The supply chain is an interdependent network that includes people, technology, resources, and organizations working together to produce, transport and deliver goods and/or services. This network allows organizations to produce and deliver goods more quickly, better, and with greater efficiency. It also reduces production and purchasing costs. It is essential to the production and delivery of health care products, electronics, and other goods that are used for daily living.
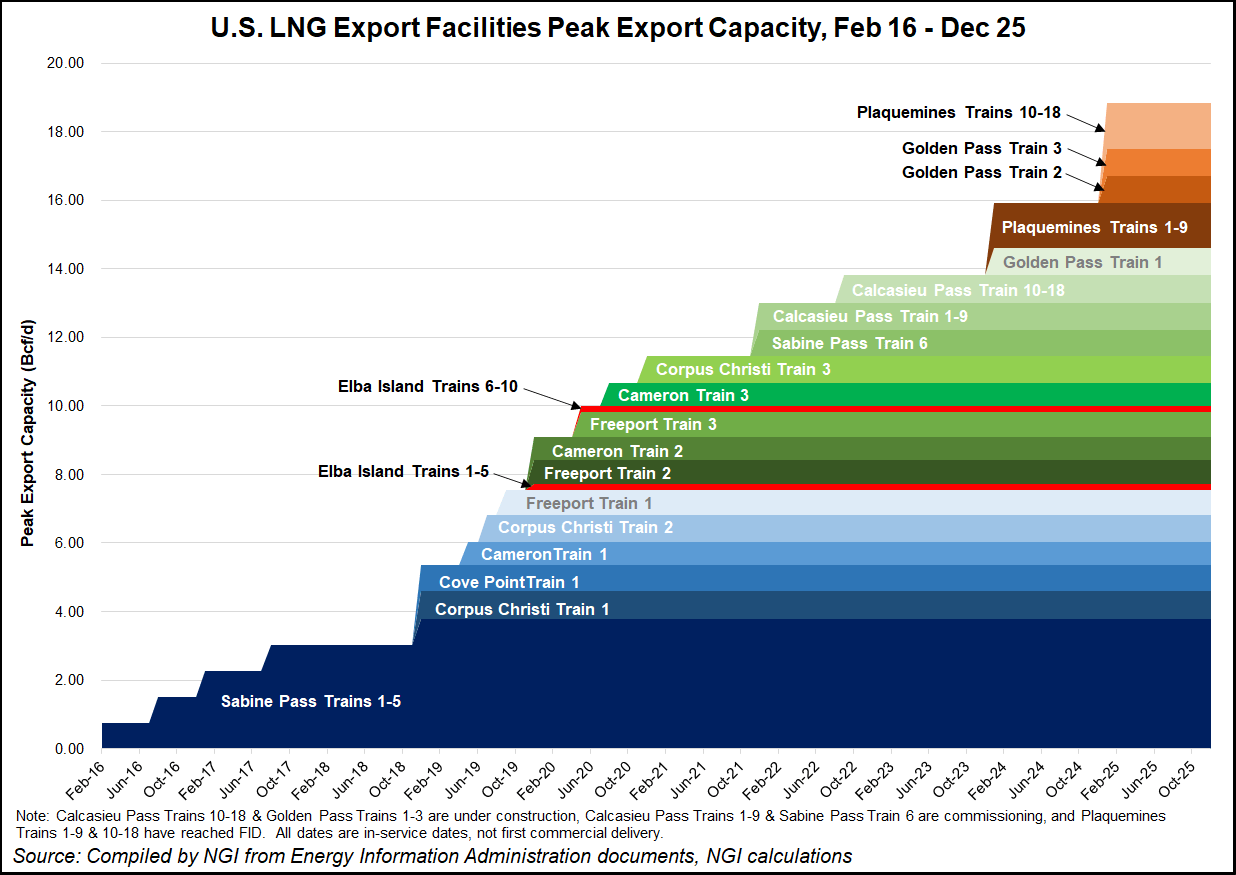
Supply chain management refers to the creation and execution of processes that move goods from the raw material to the consumer. It involves coordination among many activities including sales, marketing, and distribution. It also involves a system for managing returns of defective products.
Supply chain complexity increases as global competition rises. Part price fluctuations, offshoring and talent attrition all contribute to this increase in complexity. You may also have multiple suppliers to your organization, which can increase redundancy in your supply chains.
Supply chain management is a complex process that involves many departments in your organization. These include finance, sales and operations.
It is essential to have knowledge in all five aspects of supply chain management in order to successfully manage your supply chains. These include the design of a supply chain plan, the selection and management suppliers, the management supplier relationships, inventory management and coordination.
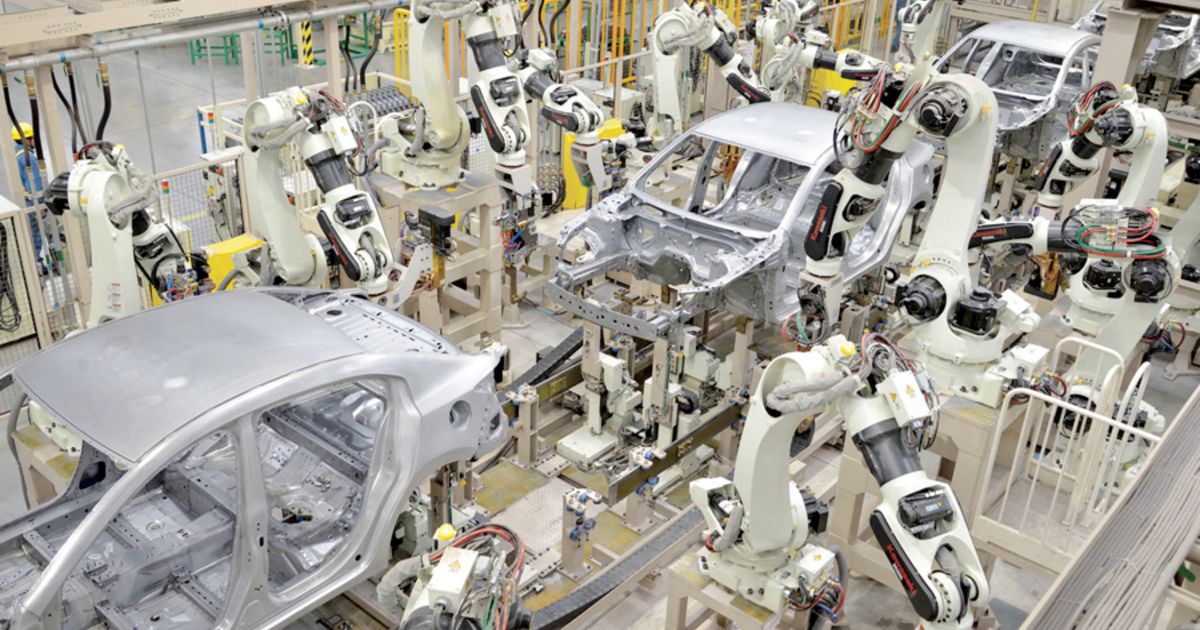
A supply chain planning plan is a plan that describes how your organization will implement the strategy. It also gives a breakdown for each step in the process. You may decide to outsource manufacturing. That includes packaging, distribution, and shipping. You might also have to inspect finished products and collect payments from your customers.
Designing your supply chain plan should include considerations for managing your supplier relationships. One example is a vendor that has a history of delivering goods on-time. You might also prefer a vendor that is flexible to allow you to obtain emergency materials when necessary.
Supply chain management can also help to reduce the wear and tear on equipment. It can also be a way for your company to stay close to customers and minimize quality issues.
FAQ
What are the responsibilities of a production planner
A production planner makes sure all project elements are delivered on schedule, within budget, as well as within the agreed scope. They ensure that the product or service is of high quality and meets client requirements.
What can I do to learn more about manufacturing?
You can learn the most about manufacturing by getting involved in it. You can also read educational videos or take classes if this isn't possible.
What are the four types of manufacturing?
Manufacturing is the process that transforms raw materials into useful products. It includes many different activities like designing, building and testing, packaging, shipping and selling, as well as servicing.
How can we increase manufacturing efficiency?
First, we need to identify which factors are most critical in affecting production times. We then need to figure out how to improve these variables. You can start by identifying the most important factors that impact production time. Once you have identified them, it is time to identify solutions.
Do we need to know about Manufacturing Processes before learning about Logistics?
No. You don't have to know about manufacturing processes before learning about logistics. Understanding the manufacturing process will allow you to better understand logistics.
What is it like to manage a logistics company?
A successful logistics business requires a lot more than just knowledge. You must have good communication skills to interact effectively with your clients and suppliers. You should be able analyse data and draw inferences. You need to be able work under pressure and manage stressful situations. You need to be innovative and creative to come up with new ways to increase efficiency. You must be a strong leader to motivate others and direct them to achieve organizational goals.
You should also be organized and efficient to meet tight deadlines.
Statistics
- In 2021, an estimated 12.1 million Americans work in the manufacturing sector.6 (investopedia.com)
- (2:04) MTO is a production technique wherein products are customized according to customer specifications, and production only starts after an order is received. (oracle.com)
- You can multiply the result by 100 to get the total percent of monthly overhead. (investopedia.com)
- In the United States, for example, manufacturing makes up 15% of the economic output. (twi-global.com)
- Many factories witnessed a 30% increase in output due to the shift to electric motors. (en.wikipedia.org)
External Links
How To
Six Sigma: How to Use it in Manufacturing
Six Sigma is defined as "the application of statistical process control (SPC) techniques to achieve continuous improvement." Motorola's Quality Improvement Department, Tokyo, Japan, developed it in 1986. Six Sigma's main goal is to improve process quality by standardizing processes and eliminating defects. Many companies have adopted Six Sigma in recent years because they believe that there are no perfect products and services. Six Sigma seeks to reduce variation between the mean production value. You can calculate the percentage of deviation from the norm by taking a sample of your product and comparing it to the average. If this deviation is too big, you know something needs fixing.
Understanding how variability works in your company is the first step to Six Sigma. Once you have a good understanding of the basics, you can identify potential sources of variation. These variations can also be classified as random or systematic. Random variations are caused by human errors. Systematic variations can be caused by outside factors. These are, for instance, random variations that occur when widgets are made and some fall off the production line. If however, you notice that each time you assemble a widget it falls apart in exactly the same spot, that is a problem.
Once you've identified where the problems lie, you'll want to design solutions to eliminate those problems. You might need to change the way you work or completely redesign the process. To verify that the changes have worked, you need to test them again. If they fail, you can go back to the drawing board to come up with a different plan.