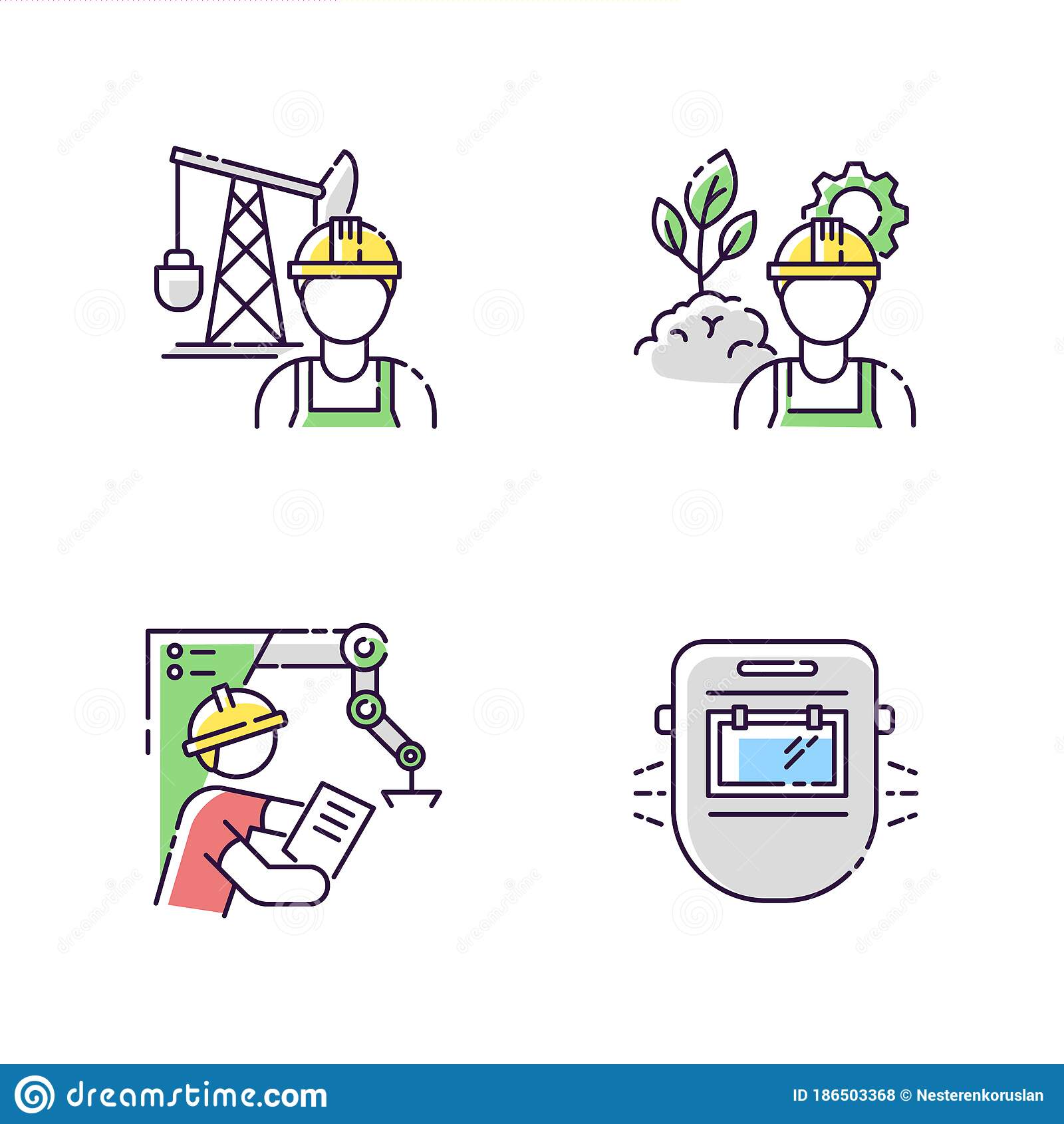
Rail logistics jobs require a variety of skills. Some positions are easy to learn, while others take years of classroom training and experience to master. These jobs require advanced product knowledge and computer proficiency. Other jobs might involve extensive travel overseas.
A transport logistics specialist works to organize the transportation of people and goods. A transport logistics specialist can also evaluate the efficiency of the process, or provide solutions to specific problems. This could include a mechanical check or determining which route is best for a particular cargo.
The role of the rail logistic manager is to ensure trains and other transport means run on time and are properly maintained. They are responsible for ensuring that trains adhere to safety regulations and rules. This job often involves moving freight from one place to another. But this is only one part of the job.
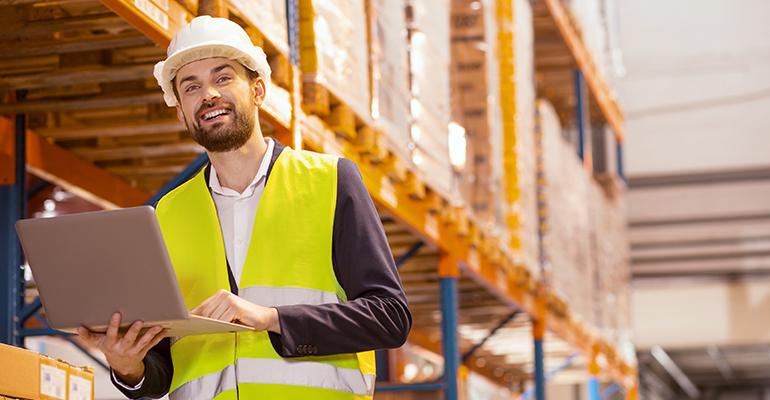
Intermodal dispatcher is another entry level job in the industry. This person coordinates a schedule for drivers and shipping companies. The person coordinates the schedule of a group of drivers and a shipping company. This position may also include administrative duties.
A railway logistics manager may also choose to work in a private firm or a government agency. These positions are generally well-paid and provide excellent career opportunities. You can expect to make approximately $45,000 annually. A bachelor's degree is not required for most of these jobs. Despite the high pay, the average train salary is not very high.
You might find logistics managers, logistics analysts and logistics coordinators. These are all key positions in the industry. Each role has its merits. However, there's a good chance you will find your talents more useful in one than the other.
Logistics managers must know how to negotiate the best rates for their company's transport needs. This requires analyzing the availability and quality of equipment and services, as well as negotiating with other party and analyzing service levels. A basic understanding of transportation management principles is required to help improve the efficiency of a company's logistics process.
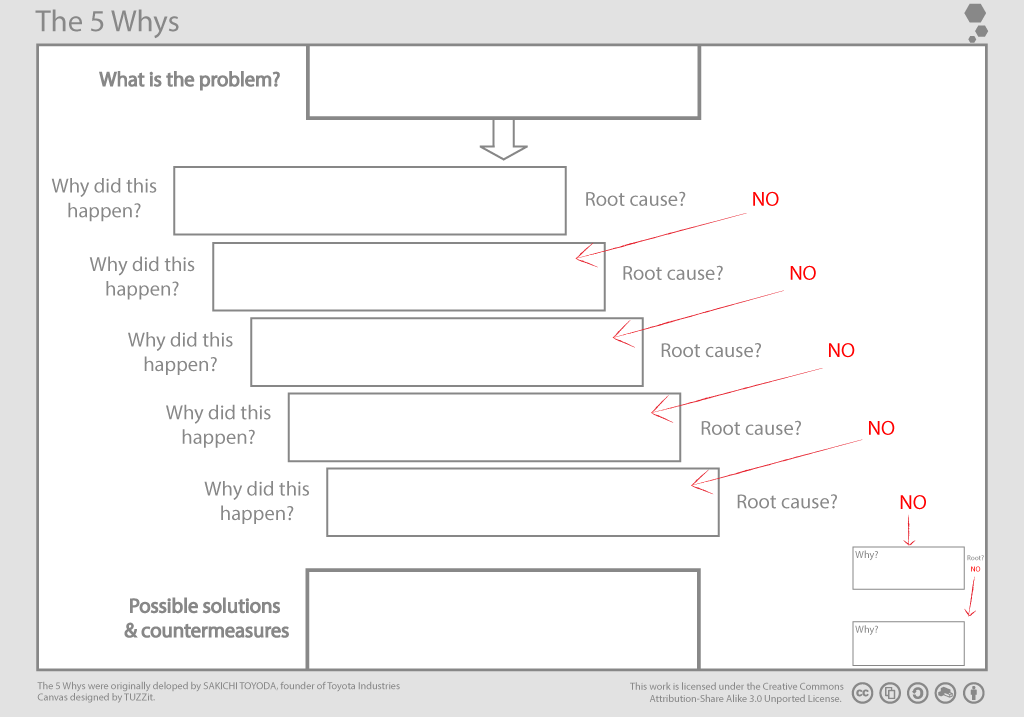
A rail logistics manager might also oversee the implementation of a state-of-the-art tracking system to track shipments and ensure the timely delivery of goods. A tracking system can often notify customers of the shipment's location.
Rail logistics managers may be asked to advise how to maximize efficiency in the transportation process. This will enable them to achieve faster results for their clients.
Many of these roles can be learned through on the job training and experience. Rail logistics coordinators, on the other side, require a bachelor's and years of relevant experience.
FAQ
What are the jobs in logistics?
There are different kinds of jobs available in logistics. Some of them are:
-
Warehouse workers - They load trucks and pallets.
-
Transportation drivers - They drive trucks and trailers to deliver goods and carry out pick-ups.
-
Freight handlers: They sort and package freight in warehouses.
-
Inventory managers – They manage the inventory in warehouses.
-
Sales representatives - They sell products to customers.
-
Logistics coordinators are responsible for organizing and planning logistics operations.
-
Purchasing agents - They purchase goods and services needed for company operations.
-
Customer service representatives - They answer calls and emails from customers.
-
Ship clerks - They issue bills and process shipping orders.
-
Order fillers - They fill orders based on what is ordered and shipped.
-
Quality control inspectors (QCI) - They inspect all incoming and departing products for potential defects.
-
Others - There is a variety of other jobs in logistics. These include transportation supervisors and cargo specialists.
Can certain manufacturing steps be automated?
Yes! Since ancient times, automation has been in existence. The wheel was invented by the Egyptians thousands of years ago. Today, robots assist in the assembly of lines.
Robotics is used in many manufacturing processes today. These include:
-
Automated assembly line robots
-
Robot welding
-
Robot painting
-
Robotics inspection
-
Robots that make products
Manufacturing could also benefit from automation in other ways. 3D printing makes it possible to produce custom products in a matter of days or weeks.
How can manufacturing efficiency be improved?
The first step is to determine the key factors that impact production time. We then need to figure out how to improve these variables. If you don’t know how to start, look at which factors have the greatest impact upon production time. Once you have identified the factors, then try to find solutions.
How can manufacturing avoid production bottlenecks
To avoid production bottlenecks, ensure that all processes run smoothly from the moment you receive your order to the time the product ships.
This includes planning for both capacity requirements and quality control measures.
This can be done by using continuous improvement techniques, such as Six Sigma.
Six Sigma is a management method that helps to improve quality and reduce waste.
It's all about eliminating variation and creating consistency in work.
What is the difference between manufacturing and logistics
Manufacturing is the act of producing goods from raw materials using machines and processes. Logistics manages all aspects of the supply chain, including procurement, production planning and distribution, inventory control, transportation, customer service, and transport. As a broad term, manufacturing and logistics often refer to both the creation and delivery of products.
Is automation important in manufacturing?
Automation is essential for both manufacturers and service providers. It allows them to offer services faster and more efficiently. It helps them to lower costs by reducing human errors, and improving productivity.
Statistics
- In the United States, for example, manufacturing makes up 15% of the economic output. (twi-global.com)
- According to the United Nations Industrial Development Organization (UNIDO), China is the top manufacturer worldwide by 2019 output, producing 28.7% of the total global manufacturing output, followed by the United States, Japan, Germany, and India.[52][53] (en.wikipedia.org)
- Many factories witnessed a 30% increase in output due to the shift to electric motors. (en.wikipedia.org)
- It's estimated that 10.8% of the U.S. GDP in 2020 was contributed to manufacturing. (investopedia.com)
- [54][55] These are the top 50 countries by the total value of manufacturing output in US dollars for its noted year according to World Bank.[56] (en.wikipedia.org)
External Links
How To
How to Use the Just In Time Method in Production
Just-intime (JIT), which is a method to minimize costs and maximize efficiency in business process, is one way. It is a process where you get the right amount of resources at the right moment when they are needed. This means that you only pay for what you actually use. Frederick Taylor, a 1900s foreman, first coined the term. He noticed that workers were often paid overtime when they had to work late. He decided to ensure workers have enough time to do their jobs before starting work to improve productivity.
JIT teaches you to plan ahead and prepare everything so you don’t waste time. Look at your entire project, from start to end. Make sure you have enough resources in place to deal with any unexpected problems. If you expect problems to arise, you will be able to provide the necessary equipment and personnel to address them. This will ensure that you don't spend more money on things that aren't necessary.
There are many JIT methods.
-
Demand-driven: This JIT is where you place regular orders for the parts/materials that are needed for your project. This will enable you to keep track of how much material is left after you use it. This will allow to you estimate the time it will take for more to be produced.
-
Inventory-based: This is a type where you stock the materials required for your projects in advance. This allows for you to anticipate how much you can sell.
-
Project-driven: This approach involves setting aside sufficient funds to cover your project's costs. If you know the amount you require, you can buy the materials you need.
-
Resource-based JIT: This is the most popular form of JIT. You assign certain resources based off demand. If you have many orders, you will assign more people to manage them. If you don't receive many orders, then you'll assign fewer employees to handle the load.
-
Cost-based: This approach is very similar to resource-based. However, you don't just care about the number of people you have; you also need to consider how much each person will cost.
-
Price-based: This is a variant of cost-based. However, instead of focusing on the individual workers' costs, this looks at the total price of the company.
-
Material-based: This is very similar to cost-based but instead of looking at total costs of the company you are concerned with how many raw materials you use on an average.
-
Time-based JIT: A variation on resource-based JIT. Instead of focusing solely on the amount each employee costs, focus on how long it takes for the project to be completed.
-
Quality-based: This is yet another variation of resource-based JIT. Instead of focusing on the cost of each worker or how long it takes, think about how high quality your product is.
-
Value-based JIT is the newest form of JIT. In this case, you're not concerned with how well the products perform or whether they meet customer expectations. Instead, your goal is to add value to the market.
-
Stock-based: This inventory-based approach focuses on how many items are being produced at any one time. It's useful when you want maximum production and minimal inventory.
-
Just-intime planning (JIT), is a combination JIT/sales chain management. It's the process of scheduling delivery of components immediately after they are ordered. This is important as it reduces lead time and increases throughput.