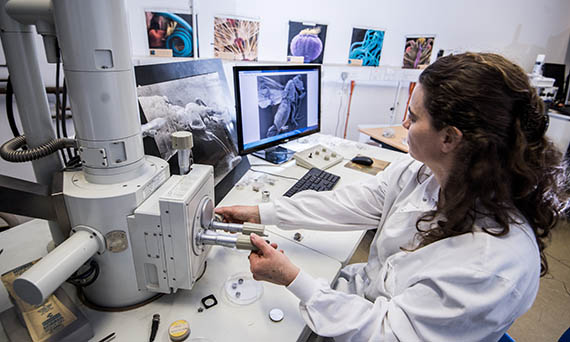
Industrial Engineers make a great salary and have many career options. You can choose to work for a different employer, pursue an advanced degree, gain managerial experience, or move on to another job that pays better. These options can increase your income and make you eligible for promotions. An Industrial Engineer may also be considered for a job in a research lab, or a design company where you can gain more knowledge about new technology.
Job description
Industrial engineers can use their creativity and ingenuity to develop new production methods. They seek to improve processes by reducing waste and inefficiency. They must communicate complex ideas clearly to all members of production. In addition to their communication skills, industrial engineering must be able understand and respond to the needs and concerns all stakeholders.
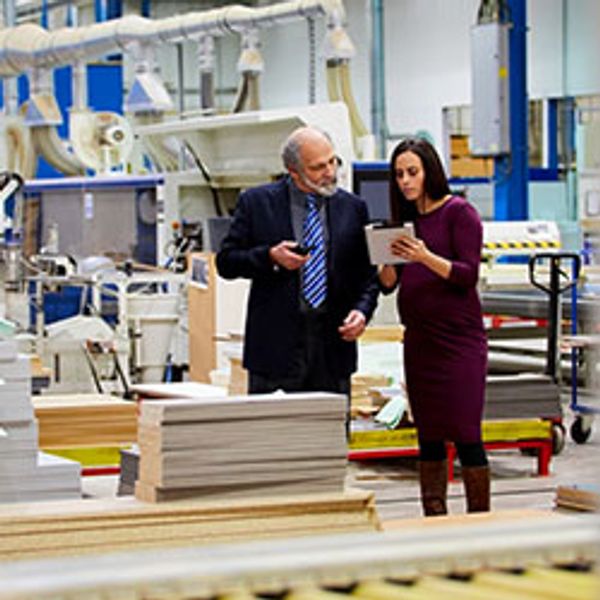
For industrial engineers, a Bachelor's Degree in Industrial Engineering or a related field is required. Employers may prefer candidates who have previous experience. Students who are interested can benefit from co-education programs. Industrial engineers may also have other degrees, such as mathematics or computer science.
Salary
Industrial engineers in NYC make an average of $598,820 per year. You have many options to increase your income. These include moving to a higher-paying job, earning advanced degrees, or gaining more experience. Management experience is a great way to increase your earning power. However, it can be difficult to find industrial engineering jobs in NYC that offer a competitive salary.
The salary for industrial engineering jobs in NYC is dependent on experience and where you live. For entry level industrial engineers, the average salary is $82,657. Senior industrial engineers make an average of $145.936. An average industrial engineer bonus is $3.939.
Education necessary
Industrial engineers are multi-disciplinary professionals who design and implement new production processes to increase efficiency. They apply logic and creativity to solve complex problems, such as reducing waste in materials, time, and labor. They work in many industries including healthcare, finance and risk management. A bachelor's degree in a STEM area is required. Industrial engineers must have work experience in addition to their education requirements.
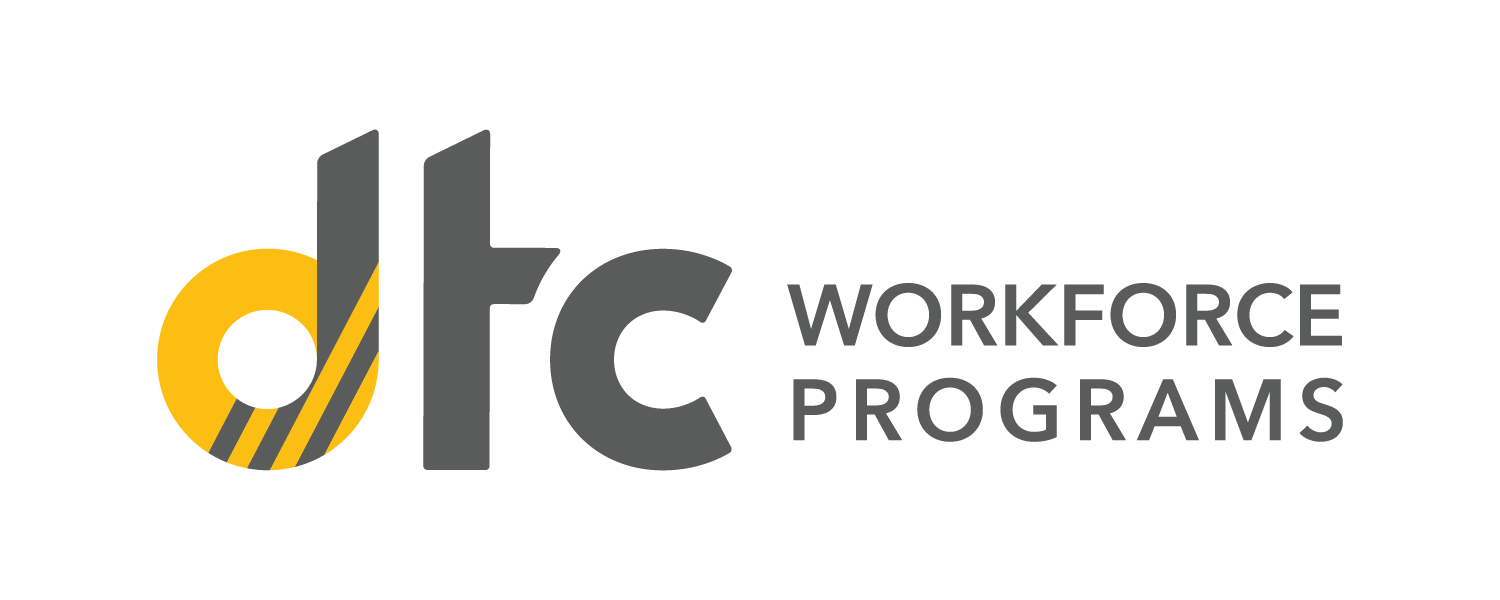
Industrial engineers are highly in demand across all industries. There is 14% job growth over the next decade. They may have an advantage over other applicants due to their education and experience. They will need to have a wide variety of skills and knowledge to ensure smooth production and analyze supply chains.
FAQ
What does the term manufacturing industries mean?
Manufacturing Industries are businesses that produce products for sale. Consumers are the people who purchase these products. These companies use a variety processes such as distribution, retailing and management to accomplish their purpose. They make goods from raw materials with machines and other equipment. This includes all types and varieties of manufactured goods, such as food items, clothings, building supplies, furnitures, toys, electronics tools, machinery vehicles, pharmaceuticals medical devices, chemicals, among others.
How can manufacturing avoid production bottlenecks
The key to avoiding bottlenecks in production is to keep all processes running smoothly throughout the entire production cycle, from the time you receive an order until the time when the product ships.
This includes planning for both capacity requirements and quality control measures.
Continuous improvement techniques like Six Sigma are the best way to achieve this.
Six Sigma management is a system that improves quality and reduces waste within your organization.
It's all about eliminating variation and creating consistency in work.
What can I do to learn more about manufacturing?
You can learn the most about manufacturing by getting involved in it. You can read books, or watch instructional videos if you don't have the opportunity to do so.
What does warehouse mean?
A warehouse, or storage facility, is where goods are stored prior to being sold. It can be an indoor space or an outdoor area. In some cases it could be both indoors and outdoors.
Do we need to know about Manufacturing Processes before learning about Logistics?
No. It doesn't matter if you don't know anything about manufacturing before you learn about logistics. However, knowing about manufacturing processes will definitely give you a better understanding of how logistics works.
What is the responsibility of a logistics manager?
Logistics managers are responsible for ensuring that all goods arrive in perfect condition and on time. This is done by using his/her experience and knowledge of the company's products. He/she should also ensure enough stock is available to meet demand.
Statistics
- Job #1 is delivering the ordered product according to specifications: color, size, brand, and quantity. (netsuite.com)
- It's estimated that 10.8% of the U.S. GDP in 2020 was contributed to manufacturing. (investopedia.com)
- You can multiply the result by 100 to get the total percent of monthly overhead. (investopedia.com)
- In the United States, for example, manufacturing makes up 15% of the economic output. (twi-global.com)
- Many factories witnessed a 30% increase in output due to the shift to electric motors. (en.wikipedia.org)
External Links
How To
How to Use Lean Manufacturing in the Production of Goods
Lean manufacturing is an approach to management that aims for efficiency and waste reduction. It was developed in Japan during the 1970s and 1980s by Taiichi Ohno, who received the Toyota Production System (TPS) award from TPS founder Kanji Toyoda. Michael L. Watkins published the book "The Machine That Changed the World", which was the first to be published about lean manufacturing.
Lean manufacturing is often described as a set if principles that help improve the quality and speed of products and services. It emphasizes the elimination of defects and waste throughout the value stream. Lean manufacturing is called just-in-time (JIT), zero defect, total productive maintenance (TPM), or 5S. Lean manufacturing emphasizes reducing non-value-added activities like inspection, rework and waiting.
Lean manufacturing is a way for companies to achieve their goals faster, improve product quality, and lower costs. Lean manufacturing is considered one of the most effective ways to manage the entire value chain, including suppliers, customers, distributors, retailers, and employees. Lean manufacturing practices are widespread in many industries. Toyota's philosophy has been a key driver of success in many industries, including automobiles and electronics.
Five basic principles of Lean Manufacturing are included in lean manufacturing
-
Define Value - Identify the value your business adds to society and what makes you different from competitors.
-
Reduce waste - Stop any activity that isn't adding value to the supply chains.
-
Create Flow. Ensure that your work is uninterrupted and flows seamlessly.
-
Standardize & Simplify - Make processes as consistent and repeatable as possible.
-
Build Relationships- Develop personal relationships with both internal as well as external stakeholders.
Although lean manufacturing isn't a new concept in business, it has gained popularity due to renewed interest in the economy after the 2008 global financial crisis. To increase their competitiveness, many businesses have turned to lean manufacturing. Some economists even believe that lean manufacturing can be a key factor in economic recovery.
Lean manufacturing is now becoming a common practice in the automotive industry, with many benefits. These include higher customer satisfaction levels, reduced inventory levels as well as lower operating costs.
It can be applied to any aspect of an organisation. Lean manufacturing is most useful in the production sector of an organisation because it ensures that each step in the value-chain is efficient and productive.
There are three types of lean manufacturing.
-
Just-in Time Manufacturing, (JIT): This kind of lean manufacturing is also commonly known as "pull-systems." JIT refers to a system in which components are assembled at the point of use instead of being produced ahead of time. This approach reduces lead time, increases availability and reduces inventory.
-
Zero Defects Manufacturing - ZDM: ZDM focuses its efforts on making sure that no defective units leave a manufacturing facility. You should repair any part that needs to be repaired during an assembly line. This is true even for finished products that only require minor repairs prior to shipping.
-
Continuous Improvement (CI): CI aims to improve the efficiency of operations by continuously identifying problems and making changes in order to eliminate or minimize waste. Continuous improvement involves continuous improvement of processes and people as well as tools.