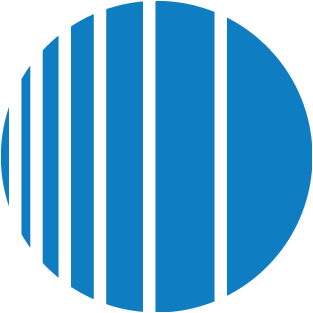
Mexico was one the major actors in DVA's trade network for global manufacturing exports, during the period under analysis. Compared to the textiles industry, which is a more important export sector, the automotive industry has not followed the same path. Both industries are still considered important in Mexico's export markets and relevant for job creation.
The Mexican automotive industry supplies the United States with the majority of its auto parts. It is also one the most rapidly growing industries in Mexico. But it has not been in a position to propel the rest of Mexico's economy onto a high expansion path. The transition of the automotive industry from a domestic-oriented sector to a regional parts/automobile chains is actually underway. This transition is driven by a combination foreign direct investment and regional processes.
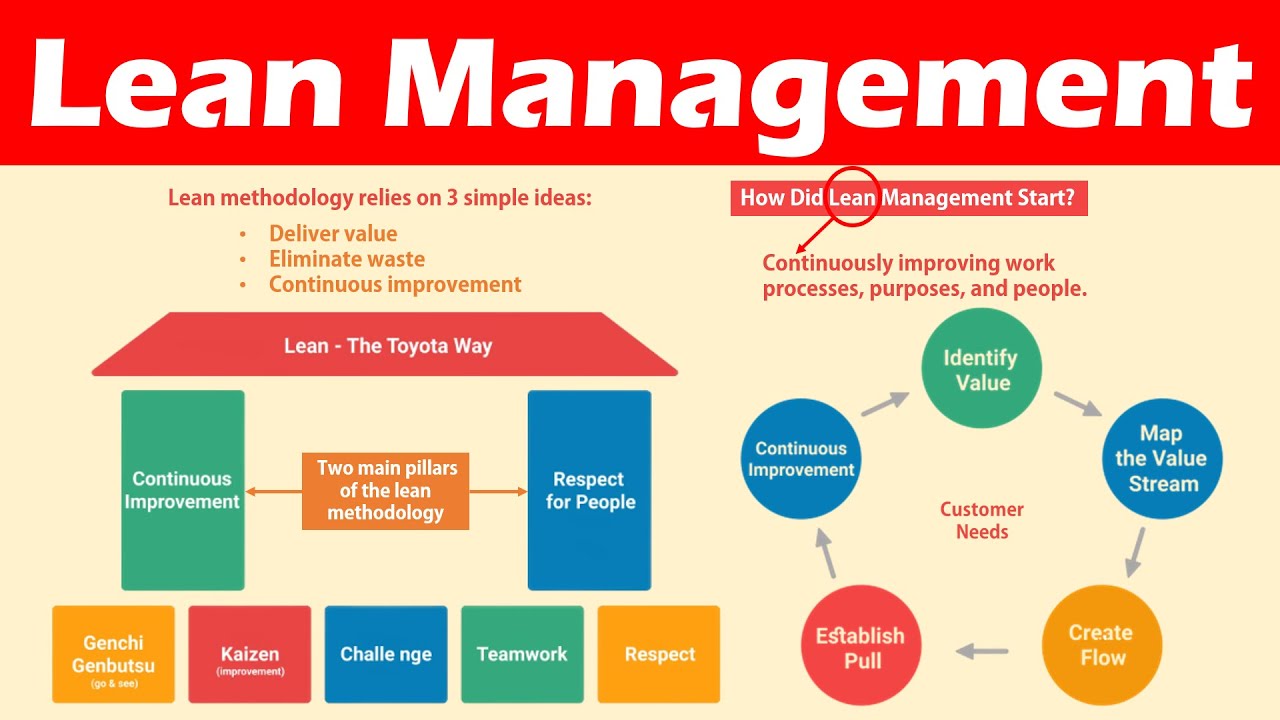
Mexico has many programs that have helped the automotive industry. It has become the most important supplier of U.S. auto parts and has experienced remarkable penetration into global markets. It also has received foreign direct investment which has helped to increase its position in global value chains.
The Mexican automotive industry is also a key player in the GVCs of Europe and the United States. Mexico's auto industry has played a significant role in its economy since the 1970s. However, it hasn't been able to penetrate the global market at the same rate as the textile sector. In addition, it has not achieved a high level of expansion in its output, although it has achieved remarkable penetration into the world market.
To analyze the relationship between international trade, labour and the Mexican manufacturing sector, the study employs the framework of decent-work indicators (ILO). The indicators are based primarily on official data and consider the interconnections between Mexico's labor regulations and trade agreements. The indicators also include the input-output analysis of international trade, which shows that Mexico plays a relatively small role in the domestic value-added of global manufacturing exports.
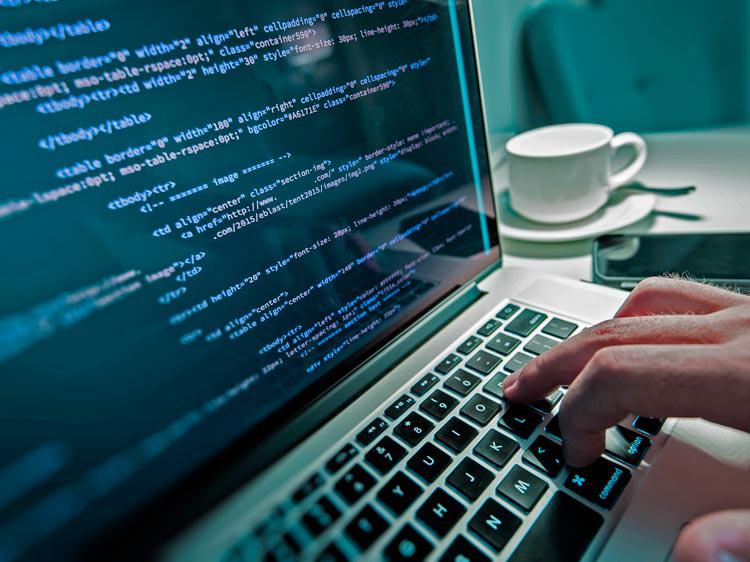
This study examines the impacts of trade liberalization in Mexico on employment in the Mexican manufacturing industry. The System of National Accounts Framework (SNA) framework is used to establish a set of decent job indicators for two major industrial sectors in Mexico, transport equipment and textiles. These indicators are compiled into a time series and used to analyze the Mexican evolution of decent employment. The study finds that the level of D V A G V C in the manufacturing sector is considerably lower than in the textile sector. In the same way, the study found that the level for employment in automobile industry is lower then in the textile. In addition, the study finds that the level of real wages has declined since the beginning of the analysis. The nominal wage adjustment did not compensate for the decline in real wages. The study finds that the level of DVA in transport equipment exports has increased in the past decade, while the level of DVA in textile exports has decreased.
FAQ
What are the goods of logistics?
Logistics refers to the movement of goods from one place to another.
They cover all aspects of transportation, such as packing, loading, transporting and unloading.
Logisticians ensure that the right product reaches the right place at the right time and under safe conditions. They assist companies with their supply chain efficiency through information on demand forecasts. Stock levels, production times, and availability.
They keep track and monitor the transit of shipments, maintain quality standards, order replenishment and inventories, coordinate with suppliers, vendors, and provide support for sales and marketing.
What does it mean to warehouse?
A warehouse or storage facility is where goods are stored before they are sold. It can be an outdoor or indoor area. In some cases, it may be a combination of both.
What jobs are available in logistics?
There are many kinds of jobs available within logistics. Some examples are:
-
Warehouse workers - They load trucks and pallets.
-
Transport drivers - These are people who drive trucks and trailers to transport goods or perform pick-ups.
-
Freight handlers: They sort and package freight in warehouses.
-
Inventory managers – They manage the inventory in warehouses.
-
Sales representatives: They sell products to customers.
-
Logistics coordinators – They plan and coordinate logistics operations.
-
Purchasing agents - They buy goods and services that are necessary for company operations.
-
Customer service representatives - Answer calls and email from customers.
-
Shipping clerks: They process shipping requests and issue bills.
-
Order fillers - They fill orders based on what is ordered and shipped.
-
Quality control inspectors - They check incoming and outgoing products for defects.
-
Other - Logistics has many other job opportunities, including transportation supervisors, logistics specialists, and cargo specialists.
How can we reduce manufacturing overproduction?
The key to reducing overproduction lies in developing better ways to manage inventory. This would reduce the time needed to manage inventory. By doing this, we could free up resources for other productive tasks.
One way to do this is to adopt a Kanban system. A Kanban Board is a visual display that tracks work progress. Kanban systems are where work items travel through a series of states until reaching their final destination. Each state is assigned a different priority.
To illustrate, work can move from one stage or another when it is complete enough for it to be moved to a new stage. A task that is still in the initial stages of a process will be considered complete until it moves on to the next stage.
This allows for work to continue moving forward, while also ensuring that there is no work left behind. Managers can monitor the work being done by Kanban boards to see what is happening at any given time. This allows them to adjust their workflows based on real-time information.
Lean manufacturing can also be used to reduce inventory levels. Lean manufacturing emphasizes eliminating waste in all phases of production. Anything that does nothing to add value to a product is waste. Here are some examples of common types.
-
Overproduction
-
Inventory
-
Unnecessary packaging
-
Exceed materials
Manufacturers can increase efficiency and decrease costs by implementing these ideas.
Statistics
- (2:04) MTO is a production technique wherein products are customized according to customer specifications, and production only starts after an order is received. (oracle.com)
- You can multiply the result by 100 to get the total percent of monthly overhead. (investopedia.com)
- [54][55] These are the top 50 countries by the total value of manufacturing output in US dollars for its noted year according to World Bank.[56] (en.wikipedia.org)
- Many factories witnessed a 30% increase in output due to the shift to electric motors. (en.wikipedia.org)
- In 2021, an estimated 12.1 million Americans work in the manufacturing sector.6 (investopedia.com)
External Links
How To
How to Use the Just-In-Time Method in Production
Just-in-time (JIT) is a method that is used to reduce costs and maximize efficiency in business processes. It's the process of obtaining the right amount and timing of resources when you need them. This means that you only pay for what you actually use. Frederick Taylor was the first to coin this term. He developed it while working as a foreman during the early 1900s. He saw how overtime was paid to workers for work that was delayed. He concluded that if workers were given enough time before they start work, productivity would increase.
JIT is about planning ahead. You should have all the necessary resources ready to go so that you don’t waste money. It is important to look at your entire project from beginning to end and ensure that you have enough resources to handle any issues that may arise. You will have the resources and people to solve any problems you anticipate. This will ensure that you don't spend more money on things that aren't necessary.
There are many JIT methods.
-
Demand-driven JIT: You order the parts and materials you need for your project every other day. This will allow you to track how much material you have left over after using it. This will let you know how long it will be to produce more.
-
Inventory-based: This allows you to store the materials necessary for your projects in advance. This allows you to forecast how much you will sell.
-
Project-driven: This approach involves setting aside sufficient funds to cover your project's costs. Knowing how much money you have available will help you purchase the correct amount of materials.
-
Resource-based JIT: This is the most popular form of JIT. You allocate resources based on the demand. If you have many orders, you will assign more people to manage them. If you don't have many orders, you'll assign fewer people to handle the workload.
-
Cost-based: This is a similar approach to resource-based but you are not only concerned with how many people you have, but also how much each one costs.
-
Price-based: This approach is very similar to the cost-based method except that you don't look at individual workers costs but the total cost of the company.
-
Material-based: This approach is similar to cost-based. However, instead of looking at the total cost for the company, you look at how much you spend on average on raw materials.
-
Time-based JIT: This is another variant of resource-based JIT. Instead of focusing on the cost of each employee, you will focus on the time it takes to complete a project.
-
Quality-based JIT is another variant of resource-based JIT. Instead of thinking about the cost of each employee or the time it takes to produce something, you focus on how good your product quality.
-
Value-based JIT: This is the latest form of JIT. In this instance, you are not concerned about the product's performance or meeting customer expectations. Instead, your focus is on the value you bring to the market.
-
Stock-based. This method is inventory-based and focuses only on the actual production at any given point. It's used when you want to maximize production while minimizing inventory.
-
Just-in-time (JIT) planning: This is a combination of JIT and supply chain management. It is the process of scheduling components' delivery as soon as they have been ordered. It's important as it reduces leadtimes and increases throughput.