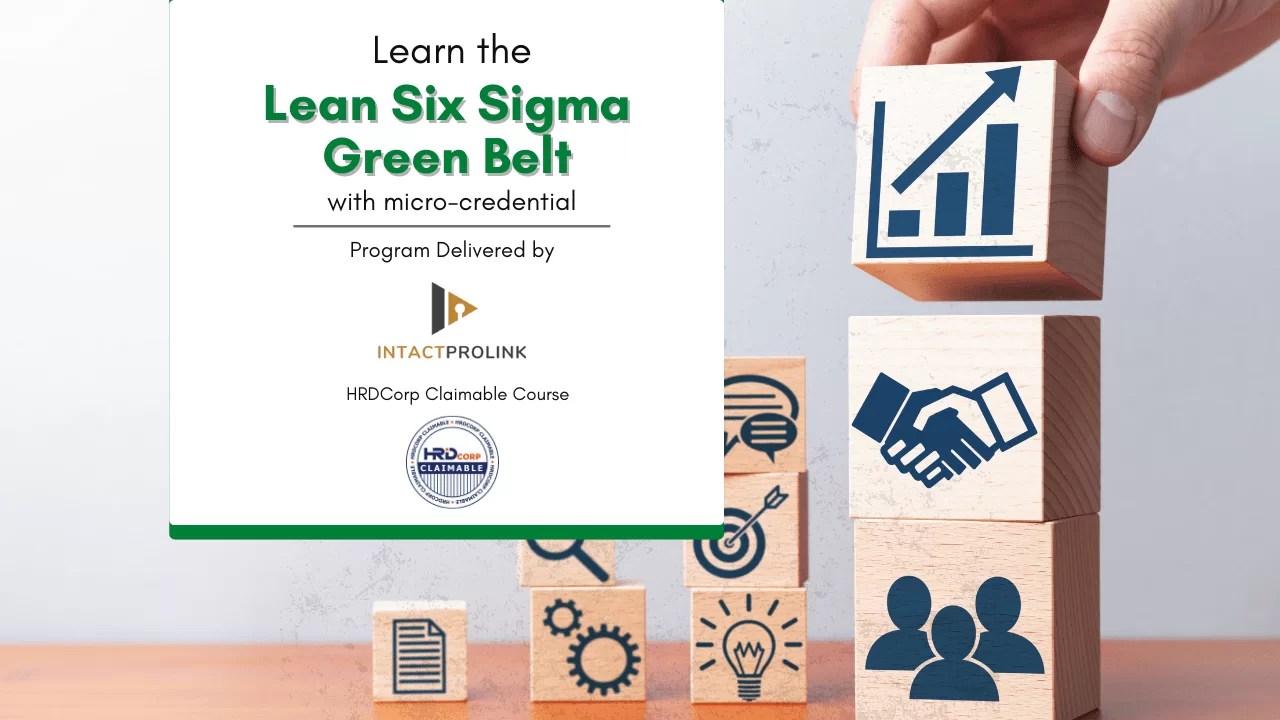
Industrial engineers are specialists who apply their knowledge of manufacturing technology in order to improve processes. They are responsible for developing and implementing new methods, analyzing existing systems, and educating workers on new policies. As a result of their expertise, they are highly valuable in research and development firms, engineering services, and consulting.
Although industrial engineers may work in many places, their primary focus is on improving the production process, reducing waste and internal costs. These engineers are creative and use logic to design better processes. Some industrial engineers work on automated manufacturing processes.
An industrial engineer has a strong background in mathematics and other scientific principles. They must also be skilled at problem-solving as well as critical thinking. They need to be able and willing to share their knowledge with others. Industrial engineers should be able to see the whole system and find weaknesses and strengths in alternative solutions.
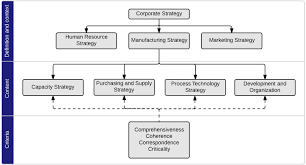
For industrial engineering careers, you must have a bachelor's degree with at least 4 years of experience. You can then apply for certification through the Society of Manufacturing Engineers. The master's degree will enable you to specialize in your chosen field.
The demand for industrial engineers is high. Their job openings will grow faster than the average national rate over the next ten year. This will lead to a 10 percent increase in the employment of industrial engineers. While most of the work is full-time, hours can vary depending upon the project. Nashville's median industrial engineer salary is $73,856 However, the wage can vary widely from one employer to the next, based on geographic location, employer, and individual qualifications.
If you are looking for an industrial engineering job, Nashville should be able to show off your professional and educational achievements. Industry-specific certifications are also required. A professional engineer license is required if you plan to work for a government agency.
Many companies hire interns in order to help them understand the intricacies behind industrial engineering. Interns can learn about lean manufacturing as well as value stream mapping and kaizen. You might be able to climb the ladder to management depending on your abilities and the company.
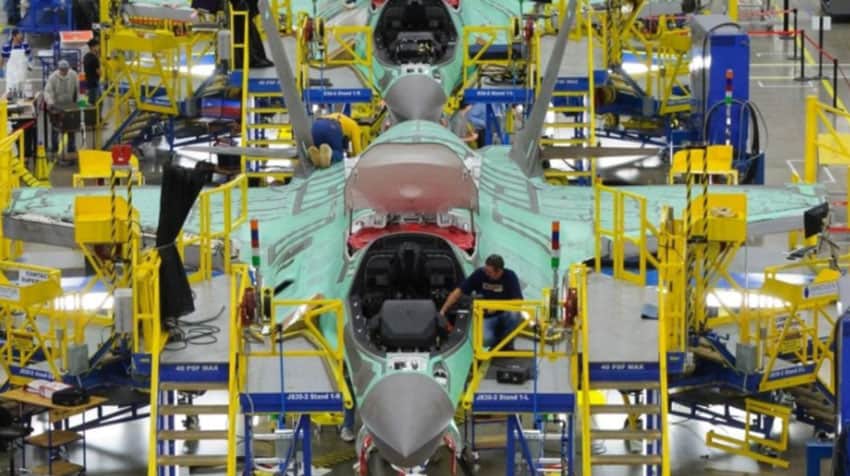
No matter if you work in a lab, an office, or both, you will need to have interpersonal communication skills to effectively communicate with your colleagues and managers. Not only will you need to communicate effectively with colleagues, but you also have to be able and willing to interact with customers or vendors.
There is a growing demand for professionals in industrial engineering. This means that you will be able to find employment in a wide range of industries. These include transport equipment manufacturers, electronic and computer manufacturers, and engineering services firms. Several colleges offer 5-year degree programs in industrial engineering. Many graduates can find entry-level jobs in many industries. However, some colleges offer programs that are more specific to certain areas such as automated manufacturing.
FAQ
What is the job of a logistics manger?
Logistics managers are responsible for ensuring that all goods arrive in perfect condition and on time. This is accomplished by using the experience and knowledge gained from working with company products. He/she should ensure that sufficient stock is available in order to meet customer demand.
What do you mean by warehouse?
A warehouse is an area where goods are stored before being sold. You can have it indoors or outdoors. Sometimes, it can be both an indoor and outdoor space.
What is the responsibility of a production planner?
A production planner makes sure all project elements are delivered on schedule, within budget, as well as within the agreed scope. They make sure that the product and services meet client expectations.
Statistics
- According to a Statista study, U.S. businesses spent $1.63 trillion on logistics in 2019, moving goods from origin to end user through various supply chain network segments. (netsuite.com)
- (2:04) MTO is a production technique wherein products are customized according to customer specifications, and production only starts after an order is received. (oracle.com)
- [54][55] These are the top 50 countries by the total value of manufacturing output in US dollars for its noted year according to World Bank.[56] (en.wikipedia.org)
- In the United States, for example, manufacturing makes up 15% of the economic output. (twi-global.com)
- Many factories witnessed a 30% increase in output due to the shift to electric motors. (en.wikipedia.org)
External Links
How To
Six Sigma in Manufacturing:
Six Sigma can be described as "the use of statistical process control (SPC), techniques to achieve continuous improvement." It was developed by Motorola's Quality Improvement Department at their plant in Tokyo, Japan, in 1986. Six Sigma is a method to improve quality through standardization and elimination of defects. Many companies have adopted Six Sigma in recent years because they believe that there are no perfect products and services. Six Sigma aims to reduce variation in the production's mean value. You can calculate the percentage of deviation from the norm by taking a sample of your product and comparing it to the average. If this deviation is too big, you know something needs fixing.
Understanding how variability works in your company is the first step to Six Sigma. Once you have this understanding, you will need to identify sources and causes of variation. You'll also want to determine whether these variations are random or systematic. Random variations happen when people make errors; systematic variations are caused externally. If you make widgets and some of them end up on the assembly line, then those are considered random variations. You might notice that your widgets always fall apart at the same place every time you put them together.
Once you identify the problem areas, it is time to create solutions. This could mean changing your approach or redesigning the entire process. Test them again once you've implemented the changes. If they don’t work, you’ll need to go back and rework the plan.