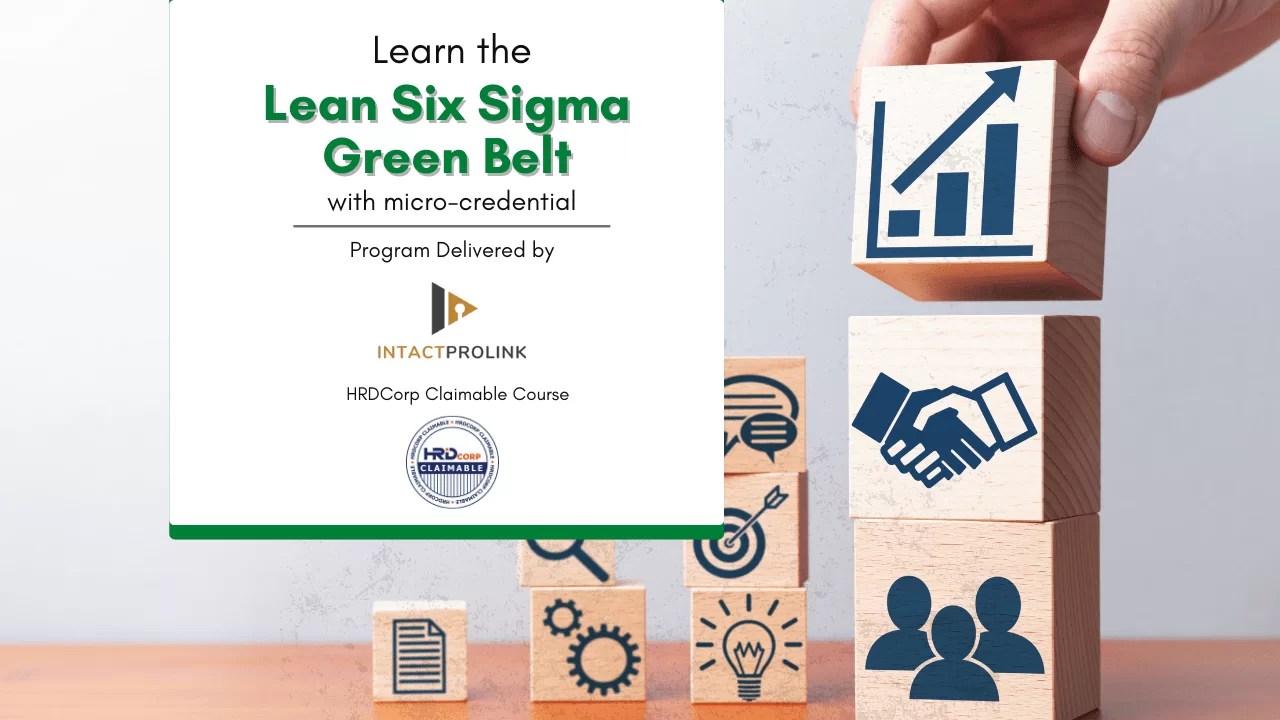
Toyota Production System, formerly known as Just in Time Production, is an integrated sociotechnical system that reduces waste and improves process. It is used to organize manufacturing, logistics, as well as customer interaction. It encourages continuous improvement and employee growth. It's also the foundation for Lean Manufacturing. Numerous manufacturing facilities, both in the United States of America and overseas, have adopted the Toyota Production System.
Sakichi Toyoda, the founder of Toyota developed the Toyota Production System. Sakichi Toyoda analyzed each phase of his company's production, and removed all unnecessary parts. The result was a 20% reduction in the build time. Toyota was able to make a vehicle in half as fast as GM. However, Toyota was on the verge of bankruptcy by the early 1950s.
Taiichi Ohno was a Toyota executive who observed how supermarket shelves were stockpiled in the mid-1940s. He realized that using Just-in-Time methods in vehicle production could save time. He collaborated with EijiToyoda, Toyota's president, to develop the Toyota Production System in 1948-1975.
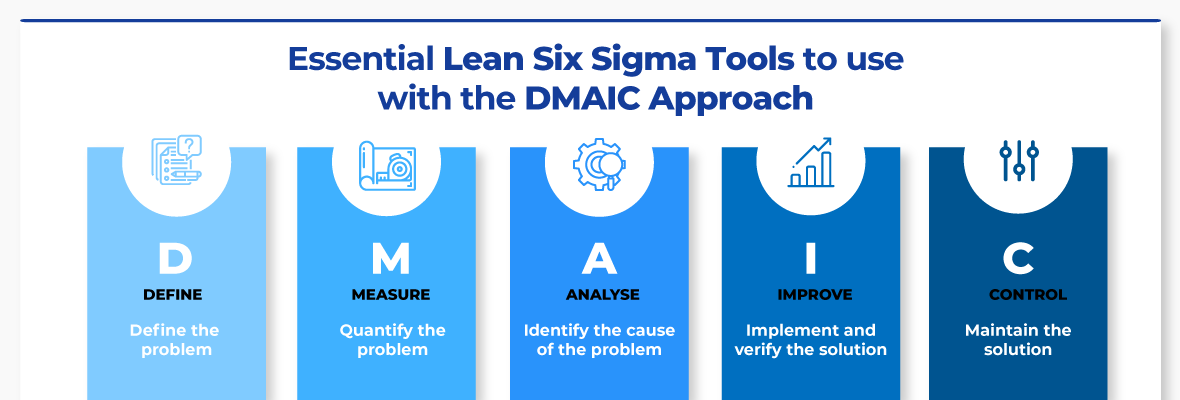
Toyota Production System was developed to eliminate wastefulness and inconsistency. The underlying philosophy was built on the concept of Kaizen, which is Japanese for continuous improvement. Toyota's Production System is continually improved to meet company needs. It encourages learning within the company by using simple, but effective, low-tech tools in conjunction with advanced production techniques. It also uses advanced information technology and unique social/management practices.
The Toyota Production System was built around six core principles. This system has been modified by many companies, including Boeing and Porsche. These companies reengineered processes in order to copy Toyota's production systems.
Toyota Production System also offers team building activities. These activities include weekly safety rounds for local leaders that assess staff performance in key safety initiatives. The team is encouraged to exchange ideas and look for ways to improve. This has influenced the culture of the company.
Jidoka, another concept, refers automating processes with human touch. Jidoka encourages workers check their work, and stop production when they spot problems. Jidoka emphasizes the importance to build things correctly the first time and not ignore problems.
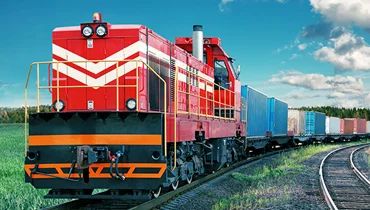
Visual control is an integral part of the Toyota Production System. This system makes instructions for workers visible on the factory floor. This helps workers follow instructions precisely. The poka-yoke device is used to check the quality of products. These devices can also verify identification of red rabbits.
Toyota Production System can be used to produce plants as well as health care. It can be used in improving patient satisfaction. It can also help in critical care or the operating room.
It's possible to improve patient care and satisfaction using the Toyota Production System. In 2003, an EPA case study reported that Toyota's efforts in waste reduction had caught the EPA’s attention. This led to a partnership with several companies, including the St. Bernard Project, which employs military veterans.
FAQ
What skills is required for a production planner?
Production planners must be flexible, organized, and able handle multiple tasks. Effective communication with clients and colleagues is essential.
What is the responsibility of a manufacturing manager?
A manufacturing manager must make sure that all manufacturing processes run smoothly and effectively. They should be alert for any potential problems in the company and react accordingly.
They must also be able to communicate with sales and marketing departments.
They must also keep up-to-date with the latest trends in their field and be able use this information to improve productivity and efficiency.
What kind of jobs are there in logistics?
There are different kinds of jobs available in logistics. Here are some examples:
-
Warehouse workers: They load and unload trucks, pallets, and other cargo.
-
Transportation drivers - They drive trucks and trailers to deliver goods and carry out pick-ups.
-
Freight handlers are people who sort and pack freight into warehouses.
-
Inventory managers – These people oversee inventory at warehouses.
-
Sales representatives - They sell products.
-
Logistics coordinators – They plan and coordinate logistics operations.
-
Purchasing agents – They buy goods or services necessary to run a company.
-
Customer service representatives - They answer calls and emails from customers.
-
Shippers clerks - They process shipping order and issue bills.
-
Order fillers: They fill orders based off what has been ordered and shipped.
-
Quality control inspectors are responsible for inspecting incoming and outgoing products looking for defects.
-
Other - Logistics has many other job opportunities, including transportation supervisors, logistics specialists, and cargo specialists.
How can manufacturing reduce production bottlenecks?
To avoid production bottlenecks, ensure that all processes run smoothly from the moment you receive your order to the time the product ships.
This includes planning to meet capacity requirements and quality control.
Continuous improvement techniques such Six Sigma can help you achieve this.
Six Sigma management is a system that improves quality and reduces waste within your organization.
It's all about eliminating variation and creating consistency in work.
What are the 7 R's of logistics?
The acronym 7R's for Logistics stands to represent the seven basic principles in logistics management. It was created by the International Association of Business Logisticians and published in 2004 under its "Seven Principles of Logistics Management".
The following letters form the acronym:
-
Responsible - ensure that actions are in compliance with legal requirements and do not cause harm to others.
-
Reliable - You can have confidence that you will fulfill your promises.
-
It is reasonable to use resources efficiently and not waste them.
-
Realistic - Consider all aspects of operations, including environmental impact and cost effectiveness.
-
Respectful – Treat others fairly and equitably.
-
Be resourceful: Look for opportunities to save money or increase productivity.
-
Recognizable provides value-added products and services to customers
What is the responsibility of a logistics manager?
Logistics managers make sure all goods are delivered on schedule and without damage. This is done by using his/her experience and knowledge of the company's products. He/she must also ensure sufficient stock to meet the demand.
Statistics
- According to the United Nations Industrial Development Organization (UNIDO), China is the top manufacturer worldwide by 2019 output, producing 28.7% of the total global manufacturing output, followed by the United States, Japan, Germany, and India.[52][53] (en.wikipedia.org)
- In the United States, for example, manufacturing makes up 15% of the economic output. (twi-global.com)
- According to a Statista study, U.S. businesses spent $1.63 trillion on logistics in 2019, moving goods from origin to end user through various supply chain network segments. (netsuite.com)
- You can multiply the result by 100 to get the total percent of monthly overhead. (investopedia.com)
- Many factories witnessed a 30% increase in output due to the shift to electric motors. (en.wikipedia.org)
External Links
How To
Six Sigma and Manufacturing
Six Sigma refers to "the application and control of statistical processes (SPC) techniques in order to achieve continuous improvement." Motorola's Quality Improvement Department, Tokyo, Japan, developed it in 1986. The basic idea behind Six Sigma is to improve quality by improving processes through standardization and eliminating defects. In recent years, many companies have adopted this method because they believe there is no such thing as perfect products or services. Six Sigma seeks to reduce variation between the mean production value. This means that you can take a sample from your product and then compare its performance to the average to find out how often the process differs from the norm. If this deviation is too big, you know something needs fixing.
Understanding the nature of variability in your business is the first step to Six Sigma. Once you understand this, you can then identify the causes of variation. It is important to identify whether the variations are random or systemic. Random variations occur when people do mistakes. Symmetrical variations are caused due to factors beyond the process. You could consider random variations if some widgets fall off the assembly lines. However, if you notice that every time you assemble a widget, it always falls apart at exactly the same place, then that would be a systematic problem.
Once you've identified where the problems lie, you'll want to design solutions to eliminate those problems. The solution could involve changing how you do things, or redesigning your entire process. To verify that the changes have worked, you need to test them again. If they don't work, you will need to go back to the drawing boards and create a new plan.