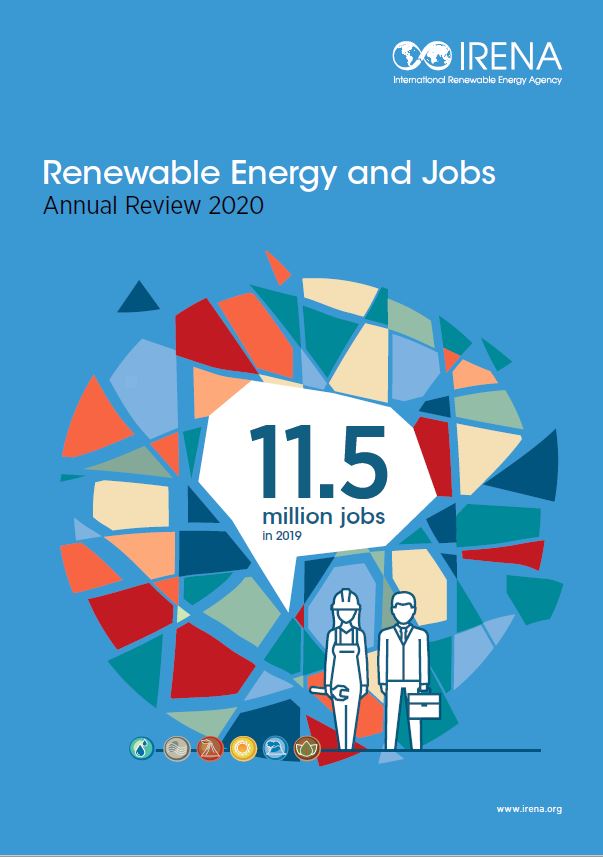
Lean manufacturing is a management technique that helps reduce waste and increase efficiency. It is based upon the philosophies of Henry Ford & KiichiroToyoda, who were presidents and CEOs of Toyota Motor Corporation in the years before World War II. Manufacturing is not only an assembly line, but a system. Lean manufacturing considers it to be a whole system. Lean is based on five principles: reduce waste; streamline the process; create knowledge; optimize the whole; and use continuous improvement.
Lean starts with identifying what you are not adding value. This can be done using qualitative or quantitative techniques. This can be done by looking at the price customers pay for your products. If the price you charge is more than the value that you provide, then you may have a problem.
Kaizen events are a great way to assess the amount waste in a process. This involves everyone in the organization working together to solve problems on an incremental basis. Kaizen events may be used either alone or in conjunction to other lean tools.
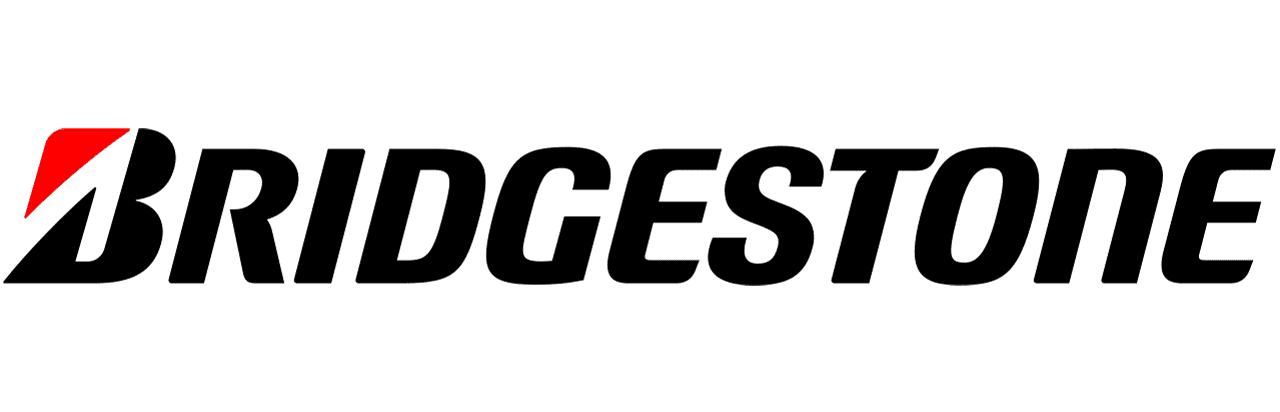
A value stream mapping can be used to identify and eliminate waste from a production plant. VSM helps manufacturers visualize the steps in a production process and determine which steps are the most time-consuming and least productive.
Waste areas include inventory, waiting, overproduction, motion, and defects. These areas will be identified by a lean team to help identify opportunities for improvement. They may be located in the supply line, in a production area or throughout the process.
Once you have identified the problem, you can begin to implement strategies to eliminate it. These include creating cross-functional groups, flattening your work load, and training employees to be multi-skilled. You might want to implement technologies such just-in-time and cellular manufacturing, depending on your business. You may also use other lean tools like total productive maintenance and Kanban management.
The system can also include standardized containers, which allow workers and other personnel to easily know exact quantities without counting. The standardized containers also make it easier to detect if food or other materials are mixed in the products. Safety mats are also available for machine areas. They can trigger an alarm if someone steps on them.
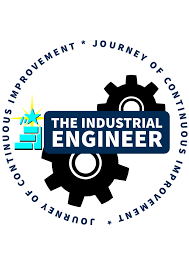
As with all lean initiatives, you will need a strong organizational culture in place. This culture should be able to communicate effectively, understand the goals of the initiative, and have a long-term view. A sustainable system of improvement is essential to the success of your business.
You can use value stream mapping to help you decide on a new machine. An inventory can be created that shows the future state of your products, raw materials, as well as customer requirements. This information allows you to more accurately predict when and how much equipment you will need. You can also create a schedule system to make sure you fulfill orders on-time.
You can increase your company's efficiency and help you reach your goals by incorporating five key principles of lean production. Find out more information about lean manufacturing techniques and the resources that are available at different websites.
FAQ
What are manufacturing and logistic?
Manufacturing is the production of goods using raw materials. Logistics encompasses the management of all aspects associated with supply chain activities such as procurement, production planning, distribution and inventory control. It also includes customer service. As a broad term, manufacturing and logistics often refer to both the creation and delivery of products.
What does manufacturing mean?
Manufacturing Industries refers to businesses that manufacture products. Consumers are those who purchase these products. This is accomplished by using a variety of processes, including production, distribution and retailing. These companies produce goods using raw materials and other equipment. This includes all types of manufactured goods, including food items, clothing, building supplies, furniture, toys, electronics, tools, machinery, vehicles, pharmaceuticals, medical devices, chemicals, and many others.
Is automation necessary in manufacturing?
Not only is automation important for manufacturers, but it's also vital for service providers. It allows them provide faster and more efficient services. It also helps to reduce costs and improve productivity.
How can efficiency in manufacturing be improved?
First, determine which factors have the greatest impact on production time. Then we need to find ways to improve these factors. If you don’t know how to start, look at which factors have the greatest impact upon production time. Once you've identified them all, find solutions to each one.
Are there any Manufacturing Processes that we should know before we can learn about Logistics?
No. It doesn't matter if you don't know anything about manufacturing before you learn about logistics. It is important to know about the manufacturing processes in order to understand how logistics works.
Statistics
- In 2021, an estimated 12.1 million Americans work in the manufacturing sector.6 (investopedia.com)
- You can multiply the result by 100 to get the total percent of monthly overhead. (investopedia.com)
- (2:04) MTO is a production technique wherein products are customized according to customer specifications, and production only starts after an order is received. (oracle.com)
- Job #1 is delivering the ordered product according to specifications: color, size, brand, and quantity. (netsuite.com)
- [54][55] These are the top 50 countries by the total value of manufacturing output in US dollars for its noted year according to World Bank.[56] (en.wikipedia.org)
External Links
How To
Six Sigma in Manufacturing
Six Sigma is "the application statistical process control (SPC), techniques for continuous improvement." Motorola's Quality Improvement Department developed it at their Tokyo plant in Japan in 1986. The basic idea behind Six Sigma is to improve quality by improving processes through standardization and eliminating defects. In recent years, many companies have adopted this method because they believe there is no such thing as perfect products or services. The main goal of Six Sigma is to reduce variation from the mean value of production. This means that if you take a sample of your product, then measure its performance against the average, you can find out what percentage of the time the process deviates from the norm. If it is too large, it means that there are problems.
Understanding the nature of variability in your business is the first step to Six Sigma. Once you've understood that, you'll want to identify sources of variation. These variations can also be classified as random or systematic. Random variations occur when people make mistakes; systematic ones are caused by factors outside the process itself. These are, for instance, random variations that occur when widgets are made and some fall off the production line. But if you notice that every widget you make falls apart at the exact same place each time, this would indicate that there is a problem.
After identifying the problem areas, you will need to devise solutions. This could mean changing your approach or redesigning the entire process. You should then test the changes again after they have been implemented. If they don't work, you will need to go back to the drawing boards and create a new plan.