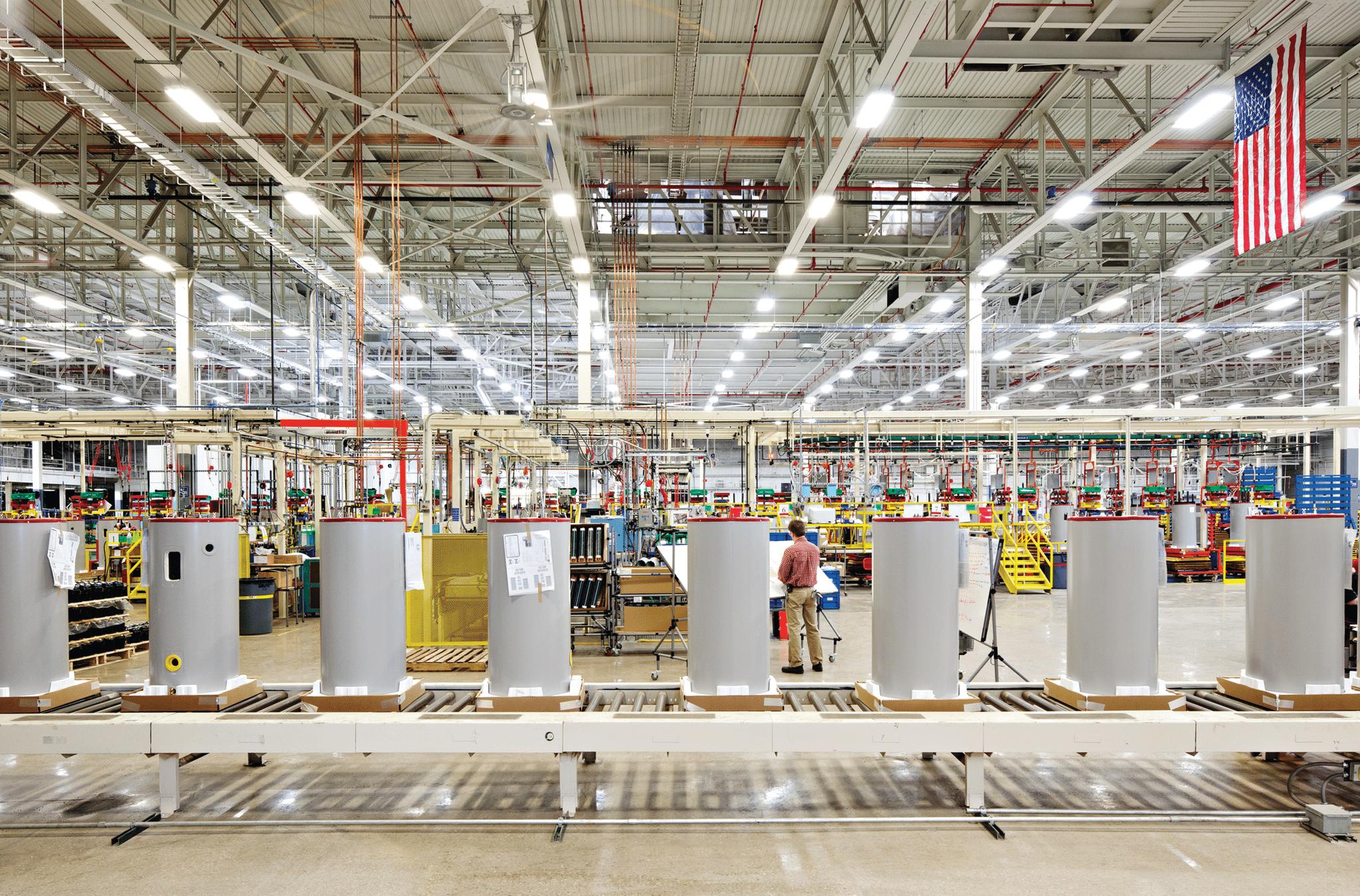
A paper company is a manufacturing firm that makes papers, such as newsprint, tissue, and paperboard. These firms may also make packaging, such as shipping boxes and bags. They are generally located in the United States.
The paper industry plays a large role in the US economy. It produces billions of dollars of goods each year and employs tens of thousands of people. Their products are used for all aspects of modern life, such as consumer goods, commercial applications, and industrial uses.
There are many paper companies in the United States. Some are more regionally-oriented while others specialize on particular types of product.
No matter where they are located, all of these companies share a common objective: creating and providing products that consumers can use in everyday life. Some of them are also focused on environmental sustainability.
The top paper companies in the USA are International Paper and WestRock. Both companies rank in Fortune 500 as the largest paper company in the World.
International Paper dominates the paper industry because it has the largest portfolio of forest lands in the United States. It has more than 42 million acres of forests in the country and a wide range of pulp, paper, and containerboard production facilities throughout North America.
International Paper’s dominance of the paper market is also due to its focus on diversity. A diverse workforce makes it easy for employees to work with each other and collaborate.
A diverse workforce allows companies to better understand their clients and prospects.
It can also assist them in providing the best products and services to their customers. They can improve their financial performance through a reduction in costs and expenses.
The diversity of their workforce can also be a great way to attract and retain good workers. A diverse workforce can help improve employee morale. That is crucial for companies like paper, which are constantly dealing with issues like globalization and economic expansion.
Focusing on sustainable development these companies implement policies that can reduce environmental impact while increasing energy efficiency. The companies also work with their suppliers to find new ways to reduce the amount of waste they produce and increase recycling.
FAQ
What is the difference between Production Planning, Scheduling and Production Planning?
Production Planning (PP), also known as forecasting and identifying production capacities, is the process that determines what product needs to be produced at any particular time. Forecasting demand is one way to do this.
Scheduling is the process of assigning specific dates to tasks so they can be completed within the specified timeframe.
Can some manufacturing processes be automated?
Yes! Yes! Automation has existed since ancient times. The Egyptians invented the wheel thousands of years ago. Nowadays, we use robots for assembly lines.
There are many uses of robotics today in manufacturing. They include:
-
Automation line robots
-
Robot welding
-
Robot painting
-
Robotics inspection
-
Robots that produce products
Manufacturing can also be automated in many other ways. For instance, 3D printing allows us make custom products and not have to wait for months or even weeks to get them made.
What are the products of logistics?
Logistics is the process of moving goods from one point to another.
They include all aspects associated with transport including packaging, loading transporting, unloading storage, warehousing inventory management customer service, distribution returns and recycling.
Logisticians ensure that the right product reaches the right place at the right time and under safe conditions. They assist companies with their supply chain efficiency through information on demand forecasts. Stock levels, production times, and availability.
They can also track shipments in transit and monitor quality standards.
What is it like to manage a logistics company?
You need to have a lot of knowledge and skills to manage a successful logistic business. You must have good communication skills to interact effectively with your clients and suppliers. You should be able analyse data and draw inferences. You must be able to work well under pressure and handle stressful situations. To increase efficiency and creativity, you need to be creative. Strong leadership qualities are essential to motivate your team and help them achieve their organizational goals.
To meet tight deadlines, you must also be efficient and organized.
Statistics
- Many factories witnessed a 30% increase in output due to the shift to electric motors. (en.wikipedia.org)
- In the United States, for example, manufacturing makes up 15% of the economic output. (twi-global.com)
- According to the United Nations Industrial Development Organization (UNIDO), China is the top manufacturer worldwide by 2019 output, producing 28.7% of the total global manufacturing output, followed by the United States, Japan, Germany, and India.[52][53] (en.wikipedia.org)
- Job #1 is delivering the ordered product according to specifications: color, size, brand, and quantity. (netsuite.com)
- According to a Statista study, U.S. businesses spent $1.63 trillion on logistics in 2019, moving goods from origin to end user through various supply chain network segments. (netsuite.com)
External Links
How To
How to Use the 5S to Increase Productivity In Manufacturing
5S stands for "Sort", "Set In Order", "Standardize", "Separate" and "Store". The 5S methodology was developed at Toyota Motor Corporation in 1954. It assists companies in improving their work environments and achieving higher efficiency.
This approach aims to standardize production procedures, making them predictable, repeatable, and easily measurable. It means tasks like cleaning, sorting or packing, labeling, and storing are done every day. Workers can be more productive by knowing what to expect.
Implementing 5S involves five steps: Sort, Set in Order, Standardize Separate, Store, and Each step requires a different action to increase efficiency. You can make it easy for people to find things later by sorting them. When you set items in an order, you put items together. Next, organize your inventory into categories and store them in containers that are easily accessible. Labeling your containers will ensure that everything is correctly labeled.
Employees need to reflect on how they do their jobs. Employees need to be able understand their motivations and discover alternative ways to do them. They will need to develop new skills and techniques in order for the 5S system to be implemented.
In addition to increasing efficiency, the 5S method also improves morale and teamwork among employees. They are more motivated to achieve higher efficiency levels as they start to see improvement.